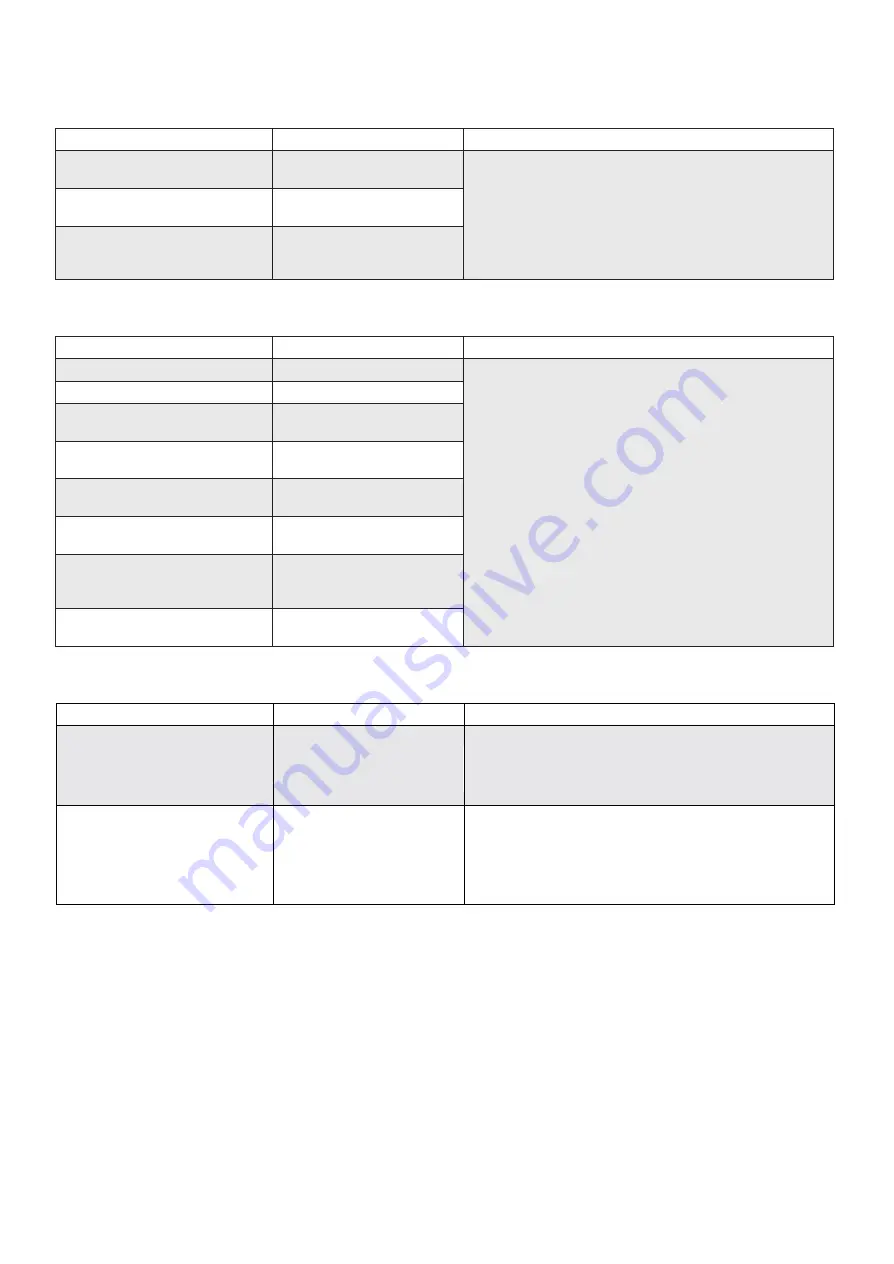
6.3.11.
Alarms related to the control loops
Fault
Cause
Check
Velocity Control Monitoring
The maximum speed
allowed by the application
has been exceeded
Following Error
The maximum follow
error allowed by the
application has been
exceeded
Check:
•The command signals and their consistency with
configured data
•The correct functioning of the drive and of the
machine being commanded
6.3.9. Synchronization, Interrupt Time and Task Time Error
Fault
Cause
Check
synchronization_error
Irregular internal frequency
interrupt
Reprogramming of drive (
�
rmware and parameters); if the
alarm persists, replace the drive
Interrupt_time_exceeded
Internal interrupt signal not
detected
Task_time_exceeded
The execution of the task has
exceeded the maximum time
limit
6.3.10. EtherCAT fault
Fault
Cause
Check
EtherCAT_communication_fault
Communication error
Check the wiring con
�
guration of the communication of
the drive and/or the EtherCAT master
EtherCAT_link_fault
Eth link not present
EtherCAT_rpdo_data
PDO data received not
correct
EtherCAT_rpdo_time_out
PDO data not received or
received after time-out
EtherCAT_tpdo_data
PDO data received not
transmitted
EtherCAT_tpdo_time_out
PDO data not transmitted or
transmitted after time-out
Internal_transmit_pdo_time_out
Error in internal PDO
communication error (dual-
axis)
Internal_receive_pdo_time_out
PDO internal communication
time-out (dual-axis)
Check command signals and their consistency with
con
�
gured data and correct operation of the drive.
DR2020
MAR2-E-191
76
fi
fi