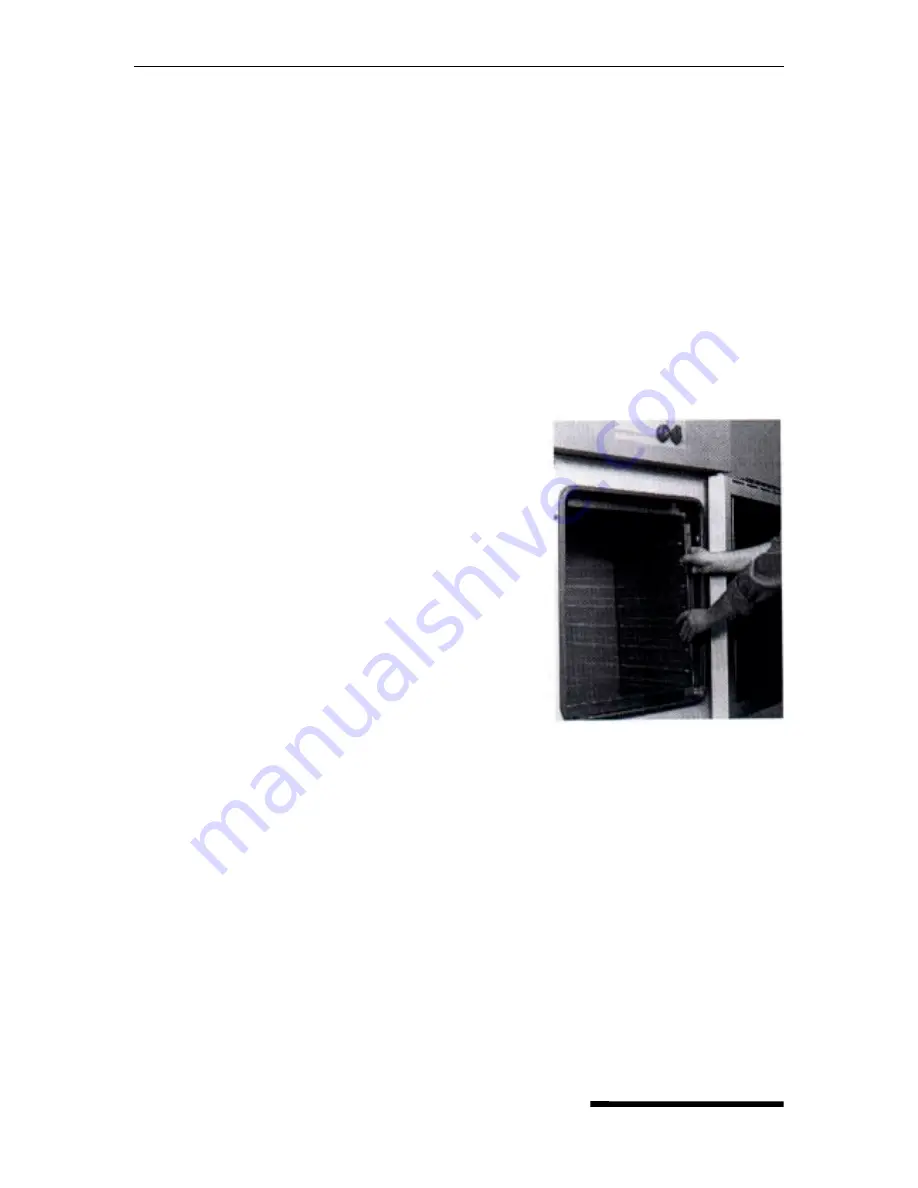
Operating instructions
CLIMACELL
Page 33
CLIMACELL_PCH_en_np_mmm
!
0208
V1.07_Blue Line
5.2
Container for collecting the condensed water steam
During the operation of the cabinet, especially in case of higher humidity, a condensate can
be collected in the lower part of the space between the inner glass door and the outer door.
The collecting container is hung under the opening in the outer chamber jacket.
During the operation of the cabinet with built-in exposure lighting some air humidity can
condense on the inner glass surface of the outer door in the cooling mode. This humidity
runs down to a special shaped sheet with a drain discharging in a condensate container.
(The container is hung under the opening in the outer chamber jacket).
The condensate container is discharged to the steam generator.
5.3
Cleaning the cooling incubator
After cleaning the unit put it together by following the reverse procedure. Take care that the
bottom and side walls are shifted behind the four projections in the front part of the chamber.
In case of leakage of some contaminated stuff into the chamber the user is responsible for a
proper decontamination of all contaminated surfaces with a suitable and approved
disinfecting agent.
Before using another cleaning or decontamination method, with the exception of the by us
recommended methods, the user should consult the producer, whether the considered
method could not cause a damage to the device.
5.4 Melting
During the operation with temperatures below 5 °C there occurs a gradual frosting of the
condensate on the cooling exchanger. The melting is carried out by putting the cabinet out of
operation untill the full defrosting of the cabinet is achieved. The defrosting can be checked
visually after removing all sheets of the inner chamber. The melting can be accelerated by
short heating the chamber on condition that the temperature rise in the chamber does not
cause a damage to the treated material eventually placed in the chamber.
Cleaning must be carried out only after cooling
down of the unit and after disconnecting the cord
from the mains. Clean the inner walls with water
and detergent, eventually with appropriate
chemical stuffs; outer surface of the unit should
be cleaned only with a cloth wetted by water
with detergent. Abrasive agents could cause
scoring of sheets.
If you wish to clean also the
external chamber jacket, remove the inner
chamber walls in following way:
Shift the upper chamber wall out of the unit,
remove the side walls, bottom and rear wall.