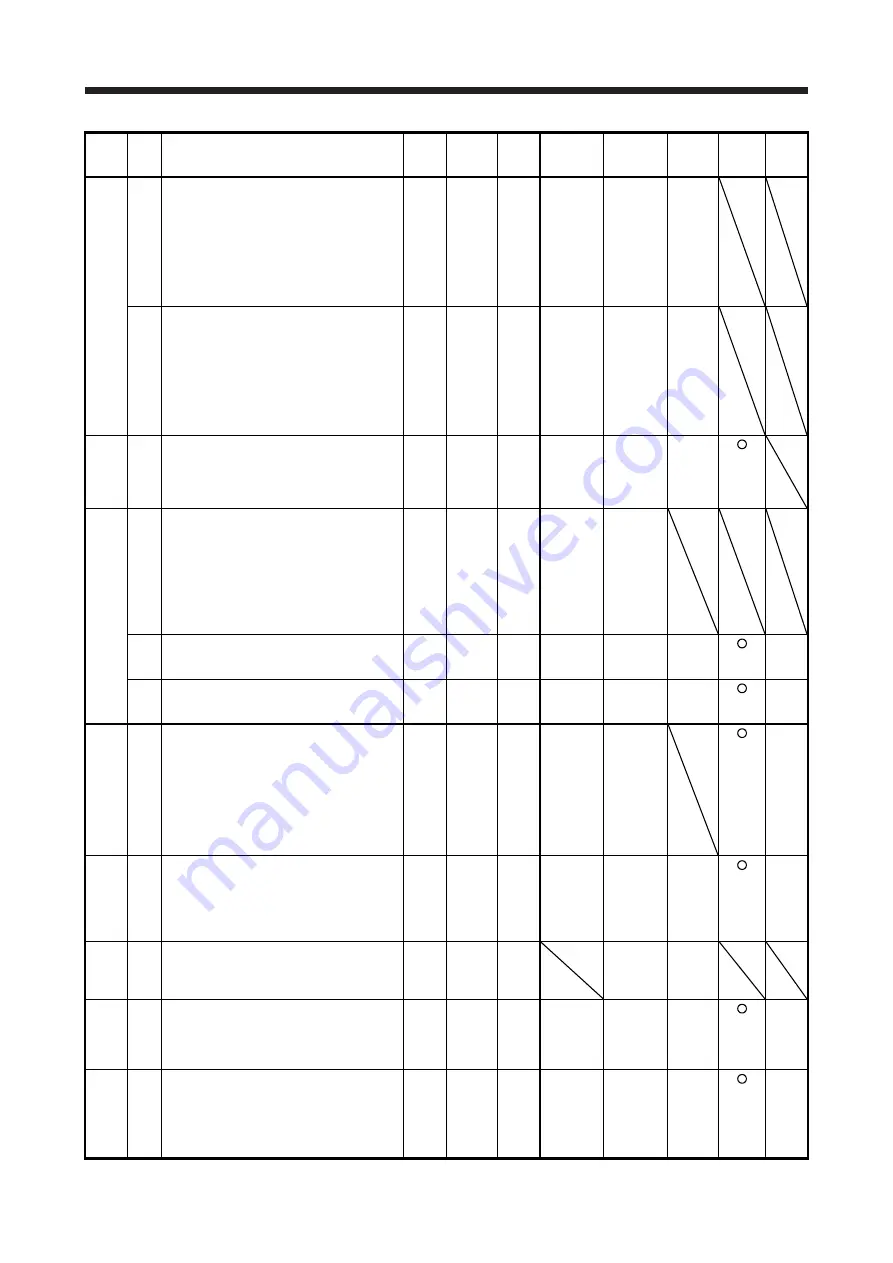
7. OBJECT LIBRARY
7 - 13
Index
Sub
Index
Name and function
Data
type
Read/
write
Variable
mapping
Initial value
Range
Unit
Saved
to EEP-
ROM
Para-
meter
607B
1
Command value limit (lower limit) (Min position
range limit)
Set the range for limiting the command position
(lower limit value). The settable values vary
depending on the setting of [Pr. PT01].
[Pr. PT01] = _ 2 _ _ (degree): 00000000h to
00057E3Fh (0 to 359999)
[Pr. PT01] = _ 3 _ _ (pulse): 80000000h to
7FFFFFFFh (-2147483648 to 2147483647)
4
bytes
Read/
write
Possible 00000000h
(degree)
80000000h
(pulse)
80000000h
to
7FFFFFFFh
pos
units
2
Command value limit (upper limit) (Max position
range limit)
Set the range for limiting the command position
(upper limit value). The settable values vary
depending on the setting of [Pr. PT01].
[Pr. PT01] = _ 2 _ _ (degree): 00000000h to
00057E3Fh (0 to 359999)
[Pr. PT01] = _ 3 _ _ (pulse): 80000000h to
7FFFFFFFh (-2147483648 to 2147483647)
4
bytes
Read/
write
Possible 00057E3Fh
(degree)
7FFFFFFFh
(pulse)
80000000h
to
7FFFFFFFh
pos
units
607C
0
Home position (Home offset)
The home position is returned. Only reading the
value is available.
Do not perform writing because doing so causes
an error.
4
bytes
Read/
write
Possible 0 80000000h
to
7FFFFFFFh
pos
units
607D
0
Software limit (Software position limit)
Set the range for limiting the command position.
Target position (607Ah) is limited within the range
between Min position limit (607Dh: 1) and Max
position limit (607Dh: 2). When the set value of
Min position limit (607Dh: 1) is equal to or greater
than the set value of Max position limit (607Dh: 2),
the function of Software position limit (607Dh) is
disabled.
1
bytes
Reading Impos-
sible
2 02h
(fixed)
1
Stroke limit - (Min position limit)
The stroke limit value in the reverse direction is
returned in units of commands.
4
bytes
Read/
write
Possible 0 80000000h
to
7FFFFFFFh
pos
units
PT17/
PT18
2
Stroke limit + (Max position limit)
The stroke limit value in the forward direction is
returned in units of commands.
4
bytes
Read/
write
Possible 0 80000000h
to
7FFFFFFFh
pos
units
PT15/
PT16
607E
0
Rotation direction selection (Polarity)
The rotation direction selection can be set.
Bit 7: position polarity
Bit 6: velocity polarity
Bit 5: torque polarity
Turn on or off both bit 6 and bit 7 to set the
rotation direction to position commands and speed
commands. Turn on or off all of bit 5 to bit 7 to set
the rotation direction to torque commands.
1
bytes
Read/
write
Possible
00h
00h to FFh
PA14/
PC29
607F
0
Maximum speed command (Max profile velocity)
Set the maximum speed command for the profile
position mode (pp) and profile velocity mode (pv).
When a value exceeding this object is set to
Target velocity (60FFh) or Profile velocity (6081h),
the speed is limited with the value of this object.
4
bytes
Read/
write
Possible 2000000 00000000h
to
001E8480h
(2000000)
0.01
r/min
PT51
6080
0
Servo motor maximum speed (Max motor speed)
The maximum speed of the servo motor is
returned. Operation cannot be performed at a
speed exceeding the speed set with this object.
4
bytes
Read/
write
Possible 00000000h
to
FFFFFFFFh
r/min
6081
0
Command speed (Profile velocity)
The current speed command value can be read.
The speed command value can also be set. Set a
value in units of 0.01 r/min.
4
bytes
Read/
write
Possible 10000 00000000h
to
permissible
instantane-
ous speed
0.01
r/min
PT50
6083
0
Acceleration time constant (Profile acceleration)
The current acceleration time constant can be
read.
The acceleration time constant can also be set.
Set the length of time until the servo motor
accelerates to the rated speed in units of ms.
4
bytes
Read/
write
Possible 0 00000000h
to
FFFFFFFFh
ms
PC01
Summary of Contents for MR-JE series
Page 9: ...A 8 MEMO...
Page 21: ...2 CC Link IE FIELD NETWORK BASIC PROTOCOL 2 4 MEMO...
Page 39: ...5 PARAMETERS 5 8 MEMO...
Page 45: ...6 MANUFACTURER FUNCTIONS 6 6 MEMO...
Page 89: ...7 OBJECT LIBRARY 7 44 MEMO...
Page 91: ...MEMO...