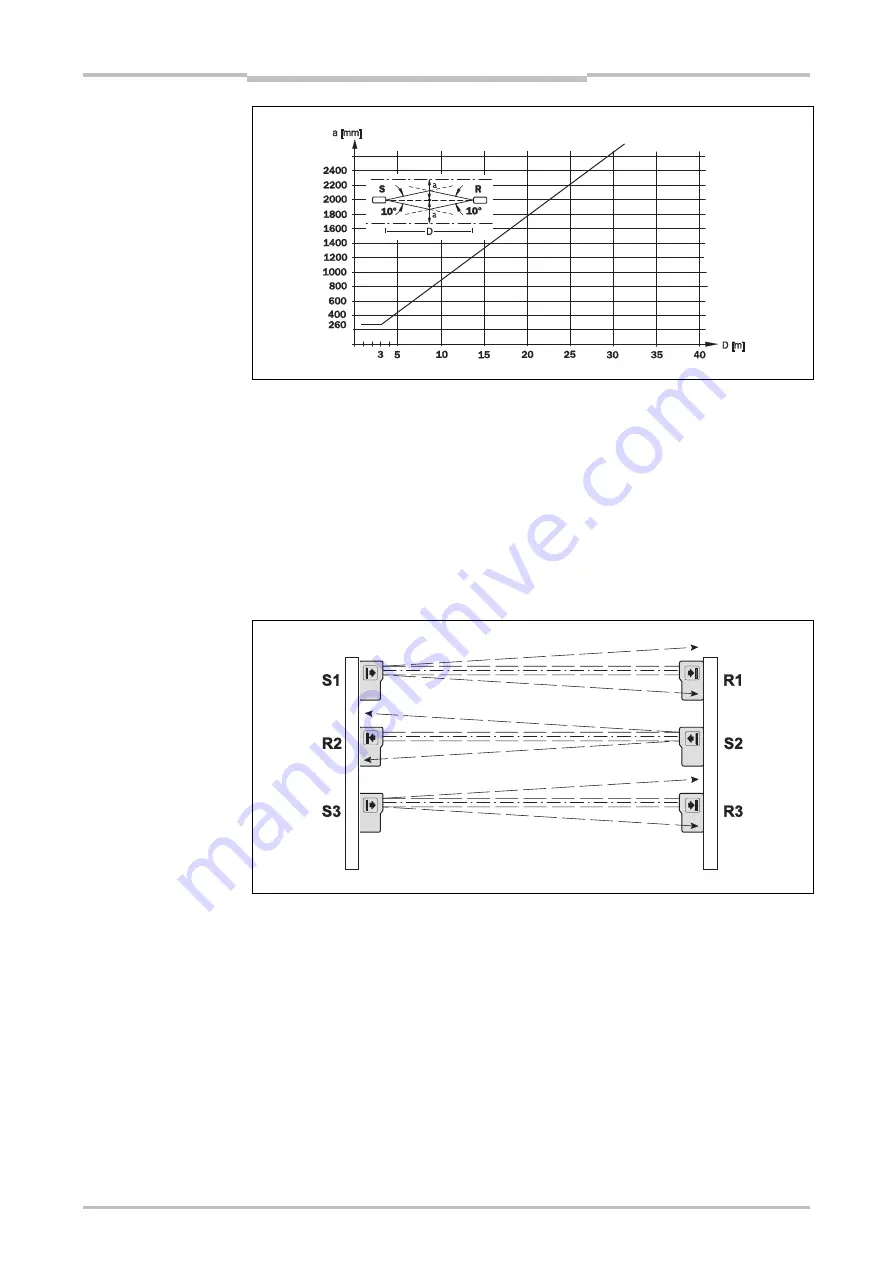
Chapter 4
58
Connecting devices
Diagrams for SICK L21 and L41 are available in the respective manual.
Avoiding mutual influence at single-beam photoelectric safety switches and
between cascades
If several single-beam photoelectric safety switch pairs are used, the field of view of
the sensors has to be observed in order to prevent mutual influence.
If the senders are only mounted on one side, the light beams may not overlap on
the receiver side so that the light beam of one sender does not reach two receivers.
If the senders and receivers are mounted alternatively, ensure that the light beam of
Sender S1 cannot be received by Receiver R3 and that the light beam of Sender
S3 cannot be received by Receiver R1.
Figure 17:
Minimum distance “a” as a
factor of the distance “D” for
testable single-beam
photoelectric safety switches
with a field of view of 10°
(e.g. SICK Wx12/18/24/27,
Vx18)
Note
Figure 18:
Mounting to avoid mutual
optical influence
Summary of Contents for MELSEC-WS series
Page 1: ...Safety Controller User s Manual WS0 CPU0 WS0 CPU1 WS0 CPU3 WS0 XTDI WS0 XTIO WS0 4RO ...
Page 2: ......
Page 117: ...Chapter 14 114 Annex ...
Page 134: ...Chapter 14 131 Annex ...
Page 151: ......