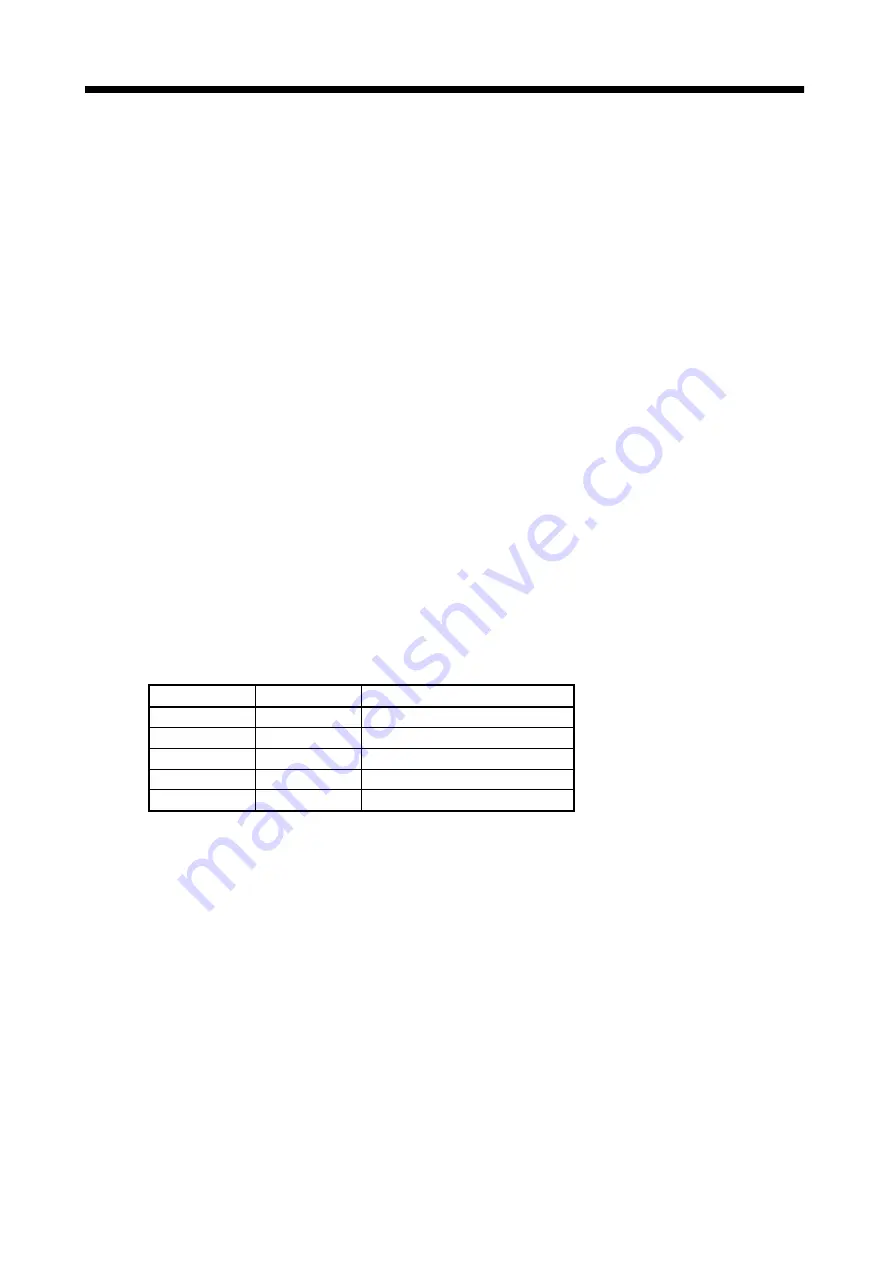
6 - 7
6. ADJUSTMENT
6.4.2 When the machine vibrates due to machine resonance frequency
(1) Machine condition
The servo motor shaft is oscillating at high frequency (100Hz or more).
The servo motor shaft motion cannot be confirmed visually. However, if the machine generates large
noise and vibrates, make Adjustment 1.
If higher "response setting" of auto tuning increases vibration, make Adjustment 2.
(2) Adjustment procedure
(a) Adjustment 1
1) Perform auto tuning with the response selection of low response.
Set parameter No. 8 to "0001" and parameter No. 9 to "0003" or less.
2) Set 563Hz or 375Hz to the notch filter (parameter No. 18).
3) Alternate a start and a stop several times, execute auto tuning, and check whether the machine
does not vibrate.
4) Decrease the notch filter value gradually and repeat step 3).
The optimum value is provided at the point where vibration is minimum.
5) To further shorten the settling time, gradually increase the response selection (parameter No. 9)
and repeat steps 1) to 4).
(b) Adjustment 2
1) Select the response selection of low response.
Set parameter No. 8 to "0001" and parameter No. 9 to "0003" or less.
2) Set the load inertia moment ratio (machine inertia moment ratio in parameter No. 12).
If an exact machine inertia moment ratio is unknown, enter an approximate value.
When the value is set in this parameter, the following parameters are set automatically. When
there is no machine resonance, the value of each parameter is set to the ideal gain for the load
inertia moment ratio (parameter No. 12) value.
Parameter No.
Symbol
Name
13
PG1
Position loop gain 1
15
PG2
Position loop gain 2
14
VG1
Speed loop gain 1
16
VG2
Speed loop gain 2
17
VIC
Speed integral compensation
3) Set "not executed" (parameter No. 8: 0002) by the auto tuning selection.
4) Decrease the speed loop gain 2 (parameter No. 16) to a value about 100 to 200 smaller than the
automatically set value.
The optimum value is provided at the point just before vibration increases.
5) Set 563Hz or 375Hz to the notch filter (parameter No. 18).
6) Alternate a start and a stop several times, execute auto tuning, and check whether the machine
does not vibrate.
7) Decrease the notch filter value gradually and repeat step 6).
The optimum value is provided at the point where vibration is minimum.
8) When there is no machine resonance, check the operating status and gradually increase the
speed loop gain 2 (parameter No. 16) and repeat steps 5) to 7).
Set the value about 50 to 100 smaller than the value at which gear sound begins to be generated.
Make this gain a little if there is variation in the machine because a timing belt or the like is
used.
9) To further shorten the settling time, gradually increase the response setting (parameter No. 9)
and repeat steps 1) to 8).
Summary of Contents for MR-J2-03B5
Page 11: ...A 10 MEMO ...
Page 15: ...4 MEMO ...
Page 21: ...1 6 1 FUNCTIONS AND CONFIGURATION MEMO ...
Page 27: ...2 6 2 INSTALLATION MEMO ...
Page 61: ...5 8 5 PARAMETERS MEMO ...
Page 73: ...7 2 7 INSPECTION MEMO ...
Page 81: ...8 8 8 TROUBLESHOOTING MEMO ...
Page 87: ...9 6 9 OUTLINE DIMENSION DRAWINGS MEMO ...
Page 91: ...10 4 10 CHARACTERISTICS MEMO ...
Page 111: ...11 20 11 OPTIONS AND AUXILIARY EQUIPMENT MEMO ...