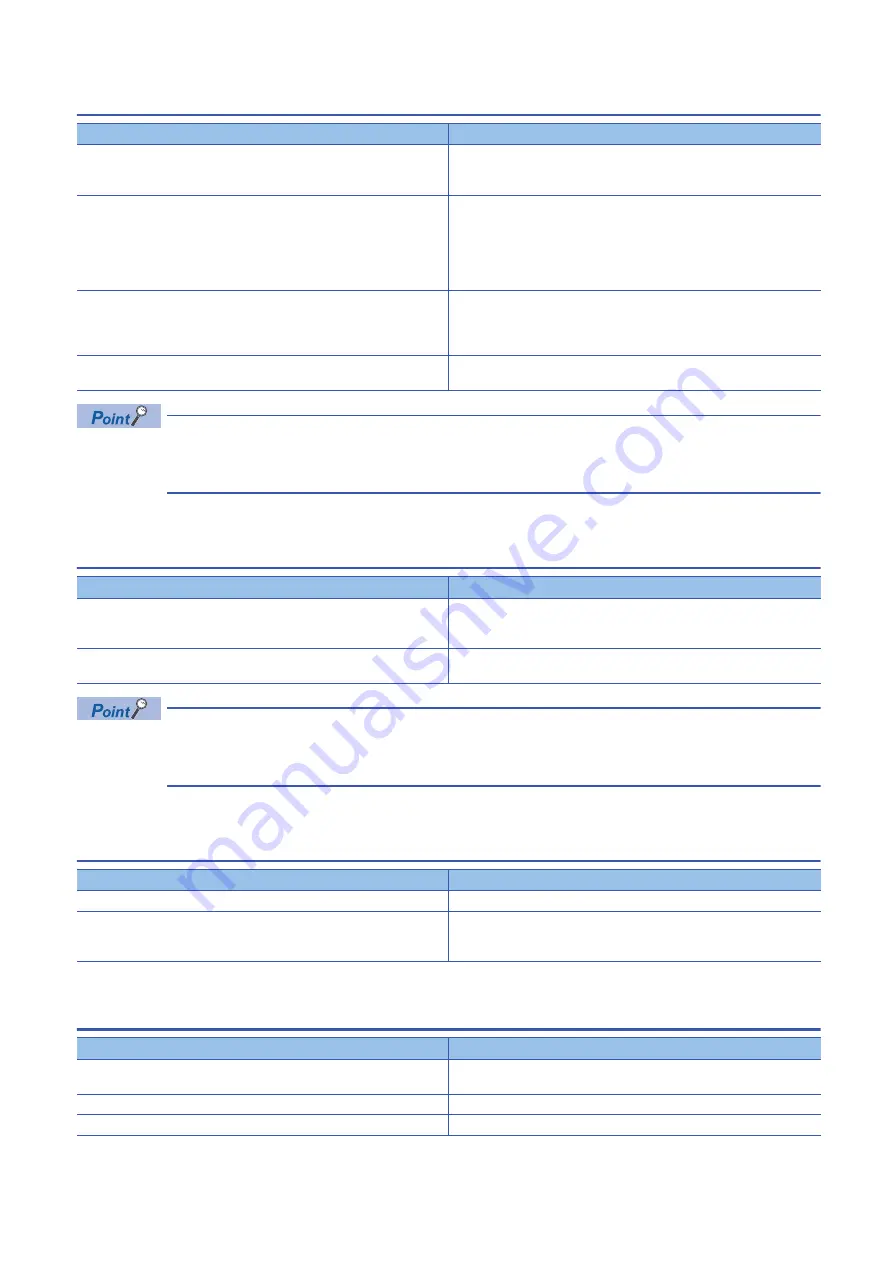
66
3 TROUBLESHOOTING
3.3 Troubleshooting by Symptom
When the ON/OFF state of an external output cannot be changed
If the ON/OFF state of the external output still cannot be changed even after the actions described above are
taken, the possible cause is a failure of the output module with diagnostic functions. Please consult your local
Mitsubishi representative.
When a disconnection or short-circuit in the output wiring cannot
be detected
If a disconnection or short-circuit in the output wiring still cannot be detected even after the actions described
above are taken, the possible cause is a failure of the output module with diagnostic functions. Please consult
your local Mitsubishi representative.
When a disconnection or short-circuit in the output wiring cannot
be detected correctly
When a disconnection or short-circuit was detected in the output
wiring
Check item
Action
Check whether the corresponding I/O status indicator LED (Y0 to YF) of the
output module with diagnostic functions turns on when 'Output signal 0 to F'
(Y0 to YF) is turned on.
When the LED turns on, the output wiring has problems.
Review the output wiring. Check whether the output wiring has been
disconnected or short-circuited, and review the wiring.
Check whether the output delay function has been properly used.
When the output delay function is enabled, output signals will turn on or off
according to the set output delay type when the delay time has elapsed after
the external output signal turn on or off. Disable the output delay function, or
review the delay time.
For details on the output delay function, refer to the following.
Check whether the system parameter "Inter-module Synchronous Setting" is
correct.
• If "Use Inter-module Synchronous Function in System" is set to "Not Use",
change the setting to "Use".
• If an expected value has not been set in "Fixed Scan Interval Setting of
Inter-module Synchronization", set a correct cycle.
Check whether the module has been selected as the synchronization target
module.
If the output module with diagnostic functions has not been selected as the
synchronization target module, select it as the target module.
Check item
Action
Check whether the corresponding I/O status indicator LED (Y0 to YF) of the
output module with diagnostic functions turns on when 'Output signal 0 to F'
(Y0 to YF) is turned on.
When the LED turns on, the output wiring has problems.
Review the output wiring. Check whether the output wiring has been
disconnected or short-circuited, and review the wiring.
Check whether "Output disconnection detection setting Y
" and "Output
short-circuit detection setting Y
" have been set to "To detect".
If the parameter settings of the output point have been set to "Not detected",
set "To detect".
Check item
Action
Check whether the wiring is influenced by noise.
Check the wiring status.
Check whether a wireless communication device such as a cellular phone or
PHS (Personal Handy-phone System) is close to the programmable controller.
Use any wireless communication device such as a cellular phone or PHS
(Personal Handy-phone System) more than 25cm away in all directions from
the programmable controller.
Check item
Action
Check whether the output wiring has any problems.
Check whether the output wiring is disconnected or short-circuited, and review
the wiring.
Check whether the external power supply is supplied.
Check that the supply voltage to the module is within the rated range.
Check whether the wiring is influenced by noise.
Check the wiring status.
Summary of Contents for MELSEC iQ-RX40NC6B
Page 1: ...MELSEC iQ R I O Module With Diagnostic Functions User s Manual Application RX40NC6B RY40PT5B ...
Page 2: ......
Page 125: ...4 OVERVIEW 123 4 MEMO ...
Page 191: ...12 MAINTENANCE AND INSPECTION 189 12 MEMO ...
Page 227: ......