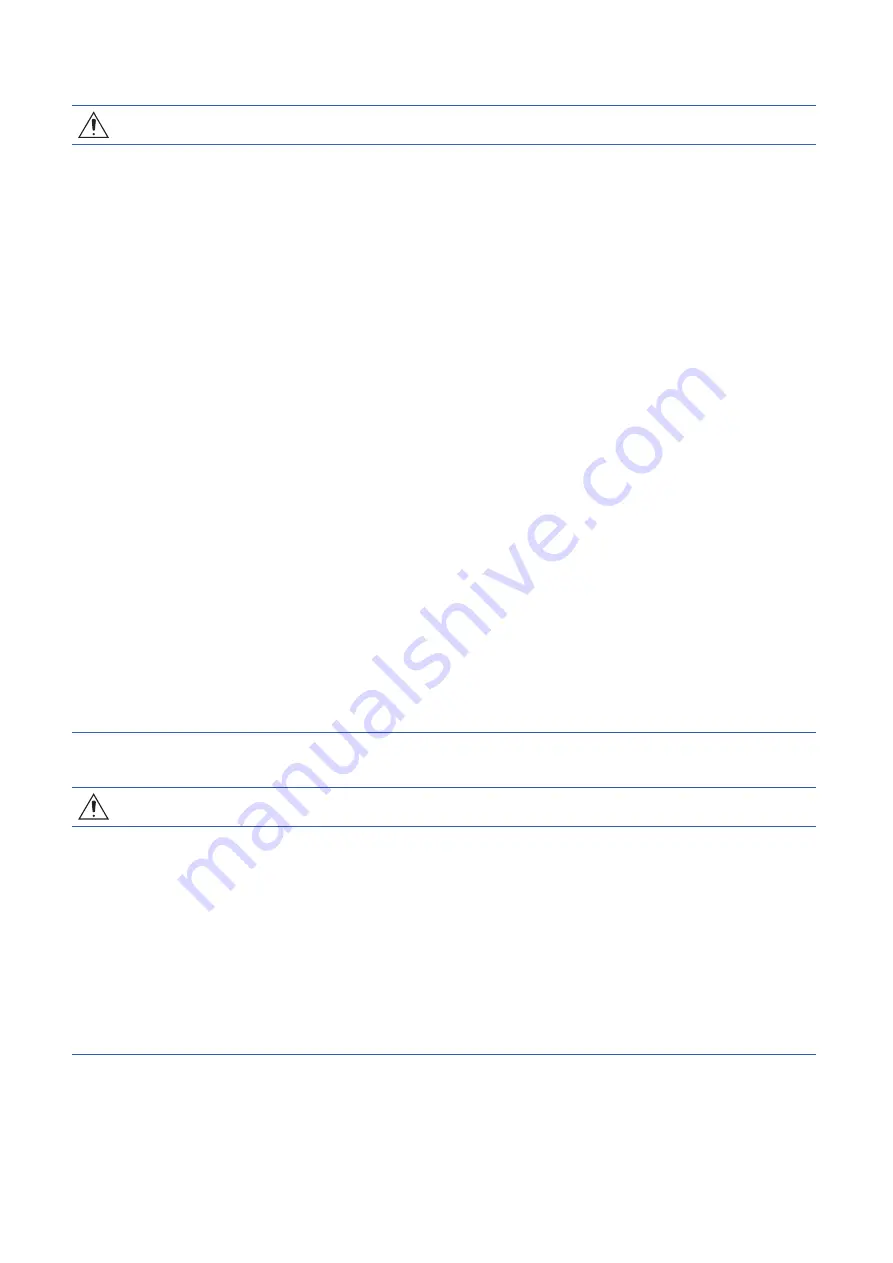
4
[WIRING PRECAUTIONS]
[STARTUP AND MAINTENANCE PRECAUTIONS]
CAUTION
●
Perform class D grounding (grounding resistance: 100
Ω
or less) of the grounding terminal on the
CPU module and extension modules with a wire 2 mm
2
or thicker.
Do not use common grounding with heavy electrical systems (refer to the User's Manual (Hardware)
of the CPU module used).
●
Connect the power supply wiring to the dedicated terminals described in this manual. If an AC power
supply is connected to a DC input/output terminal or DC power supply terminal, the programmable
controller will burn out.
●
Do not wire vacant terminals externally. Doing so may cause damage to the product.
●
Install module so that excessive force will not be applied to terminal blocks, power connectors, I/O
connectors, communication connectors, or communication cables. Failure to do so may result in wire
damage/breakage or programmable controller failure.
●
Make sure to observe the following precautions in order to prevent any damage to the machinery or
accidents due to malfunction of the programmable controller caused by abnormal data written to the
programmable controller due to the effects of noise.
-
Do not bundle the power line, control line, and communication cables together with or lay them
close to the main circuit, high-voltage line, load line, or power line. As a guideline, lay the power
line, control line and connection cables at least 100 mm away from the main circuit, high-voltage
line, load line or power line.
-
Ground the shield of the shield wire or shielded cable at one point on the programmable controller.
However, do not use common grounding with heavy electrical systems.
●
Use a cable dedicated for the PROFIBUS system. Otherwise, the performance of the PROFIBUS
system cannot be guaranteed. Also, for the total extension length of the cables and cable length
between stations, make sure to follow the specifications described in this manual. If wiring not in
accordance with the specifications is performed, normal data transmission cannot be guaranteed.
●
Check the interface type and correctly connect the cable. Incorrect wiring (connecting the cable to an
incorrect interface) may cause failure of the module and external device.
WARNING
●
Do not touch any terminal while the programmable controller's power is on. Doing so may cause
electric shock or malfunctions.
●
Before cleaning or retightening terminals, cut off all phases of the power supply externally. Failure to
do so in the power ON status may cause electric shock.
●
Before modifying the program in operation, forcible output, running or stopping the programmable
controller, read through this manual carefully, and ensure complete safety. An operation error may
damage the machinery or cause accidents.
●
Do not change the program in the programmable controller from two or more peripheral equipment
devices at the same time. (i.e. from an engineering tool and a GOT) Doing so may cause destruction
or malfunction of the programmable controller program.
Summary of Contents for FX5-DP-M
Page 1: ...MELSEC iQ F FX5 User s Manual PROFIBUS ...
Page 2: ......
Page 9: ...7 MEMO ...
Page 12: ...10 INDEX 168 REVISIONS 170 WARRANTY 171 TRADEMARKS 172 ...
Page 13: ...11 CONTENTS ...
Page 19: ...1 DESCRIPTION 17 1 MEMO ...
Page 100: ...98 9 PROGRAMMING 9 2 DP Master settings DP Slave FDL address 2 ...
Page 101: ...9 PROGRAMMING 9 2 DP Master settings 99 9 DP Slave FDL address 3 ...
Page 108: ...106 9 PROGRAMMING 9 8 Program Example of the Global Control Function ...
Page 109: ...9 PROGRAMMING 9 8 Program Example of the Global Control Function 107 9 ...
Page 110: ...108 9 PROGRAMMING 9 8 Program Example of the Global Control Function ...
Page 112: ...110 9 PROGRAMMING 9 9 Program Example of Acyclic Communication Acyclic Communication ...
Page 114: ...112 9 PROGRAMMING 9 10 Program Example of the Alarm Acquisition Function ...
Page 169: ...APPX Appendix 4 Processing Time 167 A MEMO ...
Page 175: ......