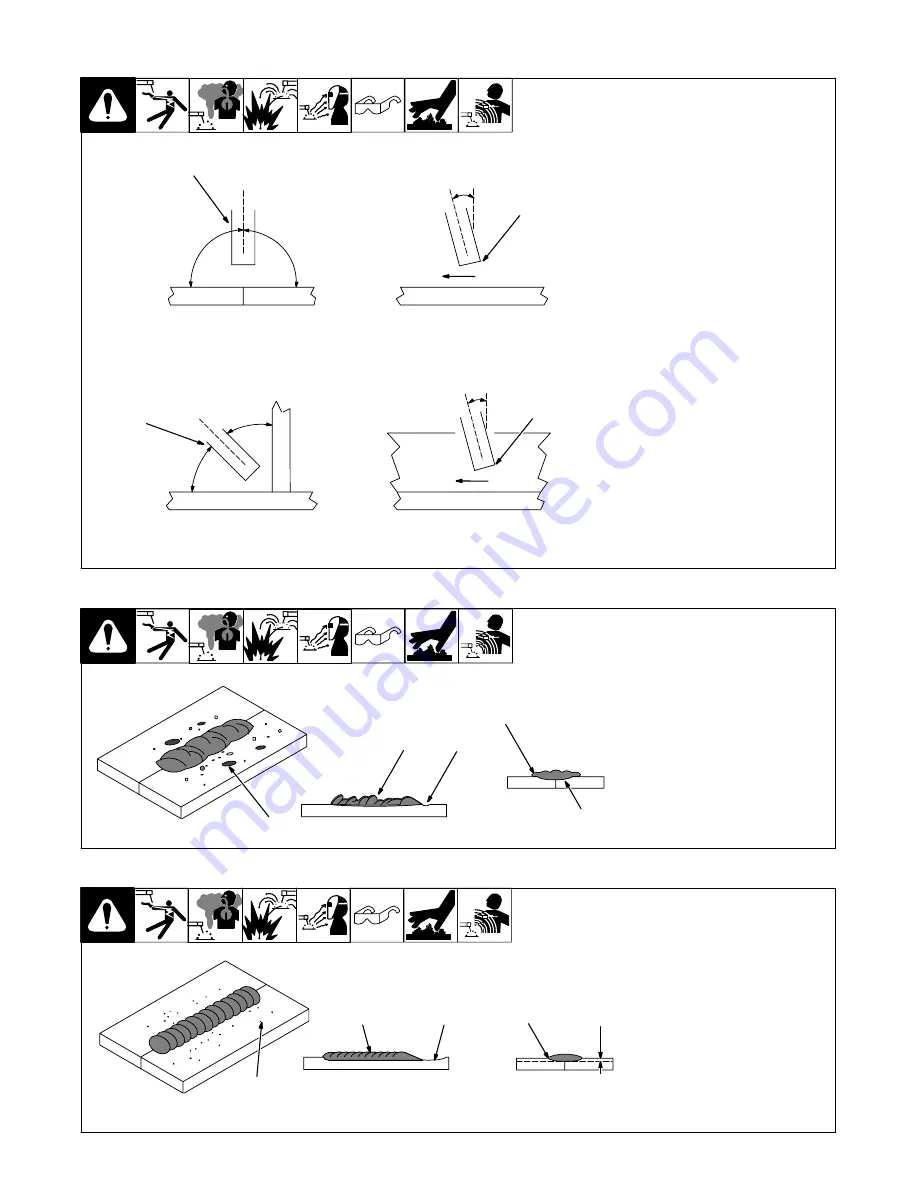
OM-2226 Page 68
14-4. Positioning Electrode Holder
S-0060
90
°
90
°
10
°
-30
°
45
°
45
°
10
°
-30
°
1
End View Of Work Angle
2
Side View Of Electrode
Angle
1
1
2
2
Groove Welds
Fillet Welds
14-5. Poor Weld Bead Characteristics
S-0053-A
1
Large Spatter Deposits
2
Rough, Uneven Bead
3
Slight Crater During Welding
4
Bad Overlap
5
Poor Penetration
5
4
2
3
1
14-6. Good Weld Bead Characteristics
S-0052-B
1
Fine Spatter
2
Uniform Bead
3
Moderate Crater During
Welding
Weld a new bead or layer for each
1/8 in. (3.2 mm) thickness in met-
als being welded.
4
No Overlap
5
Good Penetration into Base
Metal
1
5
2
3
4
Summary of Contents for Maxstar 200 DX
Page 6: ...Notes...
Page 16: ...OM 2226 Page 10...
Page 65: ...OM 2226 Page 59 SECTION 8 ELECTRICAL DIAGRAMS Figure 8 1 Circuit Diagram 237 566 B...
Page 79: ...OM 2226 Page 73 Notes...
Page 89: ...OM 2226 Page 83 Notes...