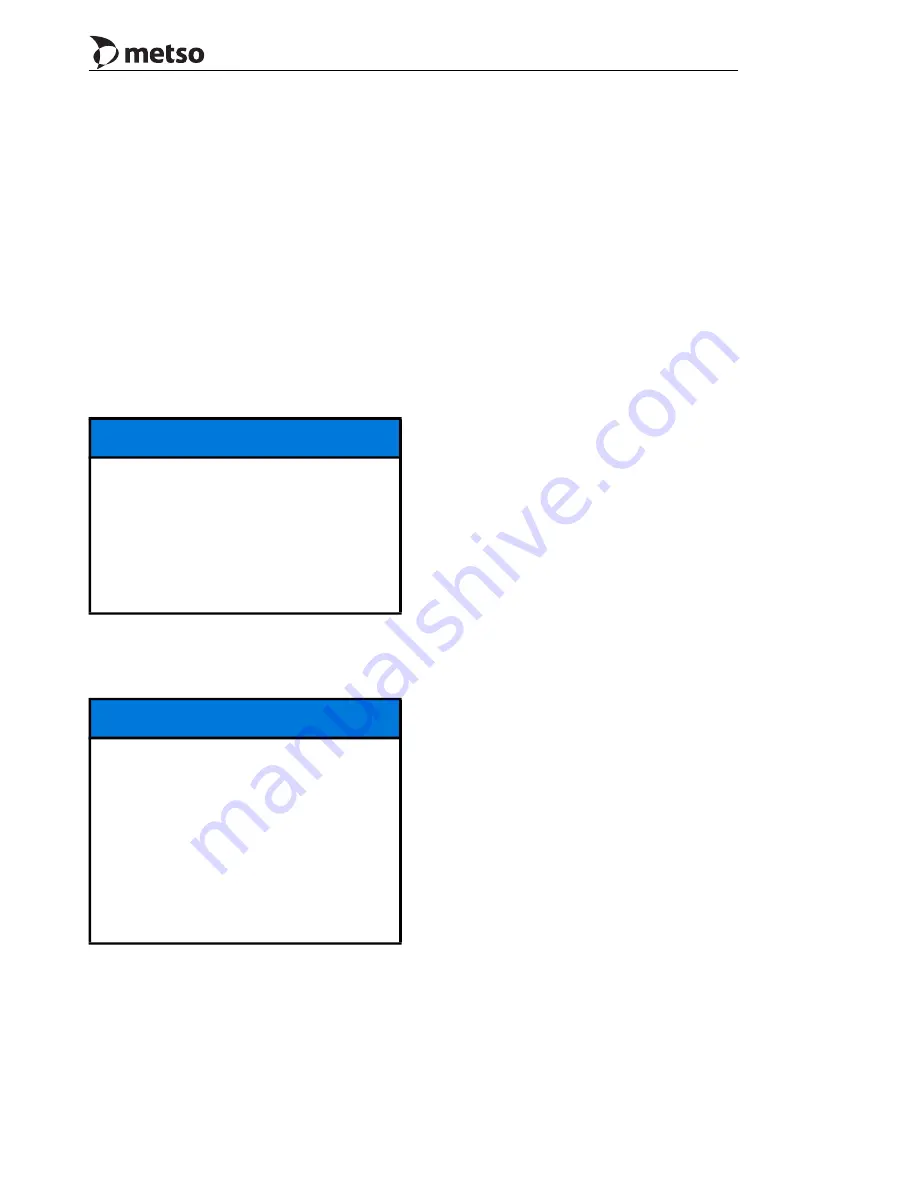
SECTION 2 - GENERAL INSTALLATION INFORMATION
MP SERIES CONE CRUSHER TECHNICAL REFERENCE MANUAL
2-11
Lesser feed arrangements will have a direct effect
on the performance of the Crusher. If the feed rate
control point is farther from the Crusher or if a
scalping screen is located between the feed rate
control and the Crusher, the additional lag time for
the change in feed rate will mean that the Crusher
will have to run at a lower average feed rate to
avoid overload.
If the velocity of the feed material is too high, the
feed can drop too far down into the Crusher,
especially when the feed is first introduced to the
Crusher. This will result in very erratic power draw
and could lead to ring bounce due to the high
reduction done in the first blow to the feed
particles.
A preferred circuit diagram is shown as Figure 2-6.
The feeding equipment must be of adequate size so
as to maintain maximum feed conditions to the
Crusher. Various crusher feed plate configurations
are available to suit your operating conditions.
The correct and incorrect methods of feed and feed
box construction are shown in Figure 2-5. Also
refer to the suggested feed arrangement drawing,
which was furnished with the installation drawing
package for your Crusher.
Whenever possible, the control philosophy should
be to operate the Crusher in a choke fed manner.
This means that there will be an excess of feed
material that will build up in the crushing cavity to
fill the crushing chamber and cover the feed plate.
The target level in the crushing cavity should be
300 mm (12") above the top of the feed plate. This
will ensure uniform spread of feed around the
crushing cavity and prevent offset feed conditions
from developing. It also evens out the power draw
to allow a higher average power draw which
translates into higher production. It is also a fact
that a choke fed Crusher will produce a finer
product size at the same setting as another unit
operated without a choke fed cavity.
In order to maintain a consistent feed level in the
crushing chamber, consideration must be given in
the design of the feed arrangement for the
installation of a level sensing device. We normally
recommend ultrasonic type level sensors which can
provide an analog output proportional to the cavity
level for good control of the feeder. Contact
resistance probes and microwave devices have also
been used with success.
NOTICE
Regardless of application, place a screen
ahead of the Crusher in the circuit to remove
fine or sticky material from the feed prior to
crushing. This will eliminate packing,
excessive adjustment ring movement and
inefficient operation. A metal detector can
also be installed to remove metallic objects,
such as tramp iron which would cause
adjustment ring movement.
NOTICE
It is important to control the speed of
material entering the Crusher. Material
dropped from a high distance into the
Crusher can pass almost entirely through
the open side of the cavity. Material falling to
the bottom of the cavity without being
crushed will cause an abnormal amount of
ring bounce. This results in severe main
frame seat damage. A rock ladder, rock box,
or similar velocity reduction device must be
used if the material drop into the cavity
exceeds 2.4 m (96") or more.
Summary of Contents for MP1000
Page 1: ...Nordberg MP Series Cone Crusher ...
Page 2: ......
Page 4: ......
Page 6: ......
Page 8: ......
Page 64: ...SECTION 0 SAFETY 0 56 MP SERIES CONE CRUSHER TECHNICAL REFERENCE MANUAL ...
Page 66: ......
Page 74: ......
Page 154: ...Countershaft and Countershaft Box Callout Description 1 Countershaft 2 Countershaft box 1 2 ...