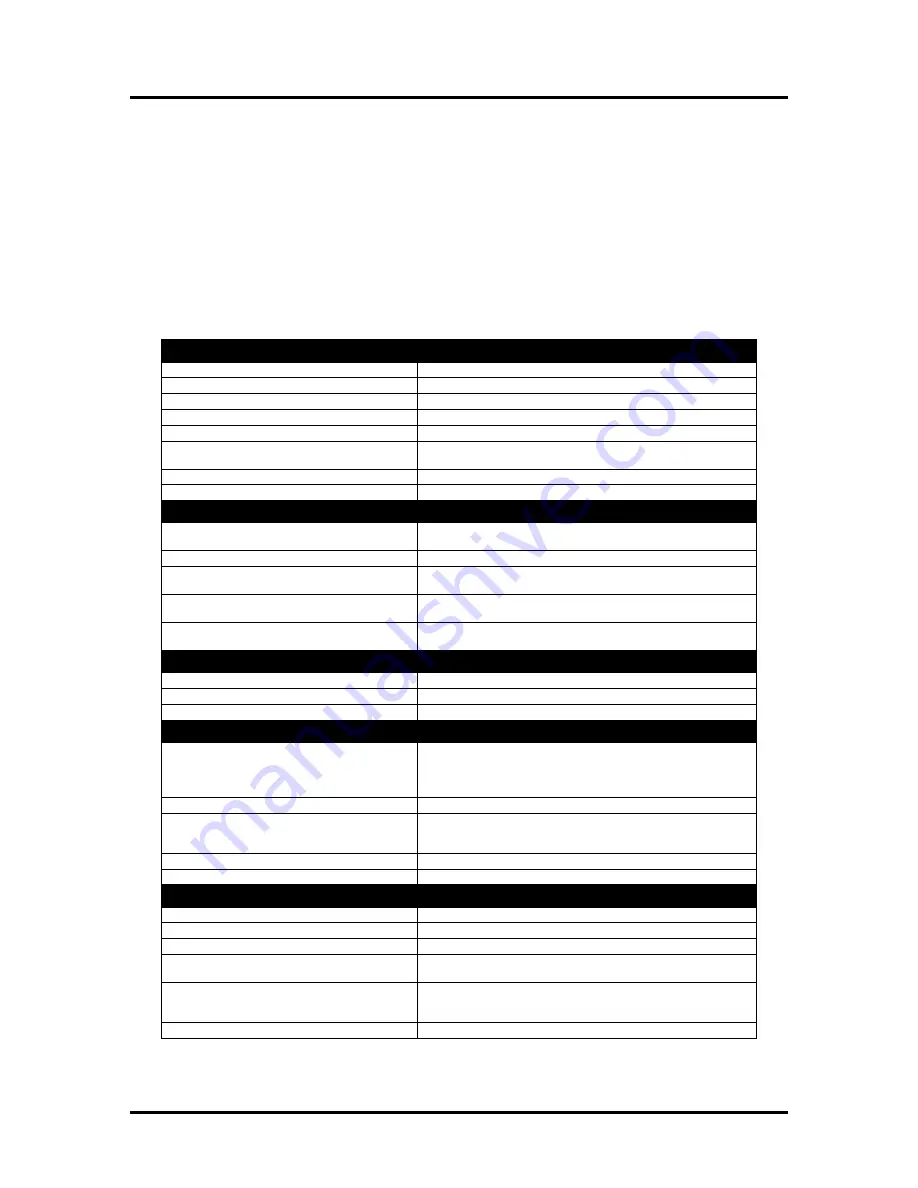
SECTION 5
MAINTENANCE
138
SECTION 5 - Maintenance
General, periodic maintenance is needed to keep the Printer in good working order. Many tasks can be
performed by operators with basic supplies, no special tools needed. Other tasks should only be performed
by trained service personnel.
NOTE:
High volume usage may require more frequent maintenance.
Maintenance Supplies & Equipment:
Flashlight, small telescoping mirror, hard-bristled toothbrush,
tweezers, small flathead screwdriver, powder-free nitrile gloves, protective clothing and eyewear, vacuum
with wand, deionized/distilled water, Super Lube 21030 synthetic grease (
or equivalent
), Loctite 38650
copper anti-seize (
or equivalent
), can of compressed air, foam or lint-free cotton swabs, lint-free wipes,
disposable shop towels.
AS NEEDED MAINTENANCE (Depending on Printer usage)
Cleaning
(Remove media fibers and ink residue):
Media path, Service Station (Wiper Roller, Platen), Sensors, Rollers
Ink Revolver Couplings
Inspect and clean after every Printhead removal.
Printhead
Wipe as needed to maintain print quality.
Printhead Pen Driver PCA
Clean contacts after every Printhead removal.
Wiper Roller
Replace with Printhead to help avoid possible damage to new head.
Lubrication (
Super Lube 21030)
Service Station (cams, lifting arm pivot points and guide tracks), Lift
Motor Gear
Printhead, Head Media Guide, Lip of Cap
Wipe these areas clean after system is primed or as needed.
Replacement
Rollers, Ink Waste Tray, Ink Revolver Couplings, Tubing, Belts.
DAILY MAINTENANCE
Ink Cartridge(s)
Clean manually prior to installing, after paper jams and when
automated servicing does not clear nozzles.
Media Path
Clean to remove excess ink residue and debris.
Print Engine: System Components, Paper Path
surfaces (upper and lower.)
Clean to remove excess ink residue and debris.
NOTE: DO NOT wipe Starwheel Assemblies.
Printhead
Clean after:
Installing and priming, removing and replacing, priming
or repriming, contamination.
Service Station:
Capping Station and Platen
Empty/clean excess ink residue and debris.
BI-WEEKLY MAINTENANCE
Media Sensors
Clean to remove excess ink residue and debris.
Print Engine
Clean to remove excess ink residue and debris.
Wiper Roller, Cap Station Seal
Inspect for proper operation and wear.
MONTHLY MAINTENANCE
Lubrication (white lithium grease)
Media Table Lift Assembly
(Threaded Rods, Roller Guide Tracks)
Optional Receiving Tray/Stacker Lift Assembly
(Threaded Rod)
Grit Rollers
Inspect for proper operation and residue build-up.
Ink Tubing, Connections, Peristaltic Pump,
Pinch Valve & Vents, Buffer Boxes, Ink
Revolver Couplings
Inspect for leaks, kinks, pinches, proper operation.
Ink Waste Tray
Inspect for excessive ink saturation or leakage.
Lift Motor Gear
Inspect for proper operation, debris and wear.
YEARLY MAINTENANCE
Check Firmware Version
Verify latest version and update if needed.
Grit Rollers
Clean to remove excess ink residue and debris.
Ink Tank Latches/Ink Tank Bay
Inspect for proper operation, wear, debris, leakage.
Inspect Moving Parts: Media Path, Pump, Pinch
Valves and Service Station
Verify smooth operation. Listen for unusual noise indicating damage
or wear.
Lubrication (
Super Lube 21030)
Lifter Motor Gear, Grit Roller Ground Springs and Washers,
Service Station (cams, lifting arm pivot points, wiper roller gears,
guide tracks)
Service Station: Wiper Motor Assy, Sled Assy
Clean to remove excess ink residue and debris.
Summary of Contents for AS-1180C
Page 75: ...SECTION 4 DISASSEMBLY AND ASSEMBLY 73 a J1002 Cable J1002 Socket Location Connection ...
Page 76: ...SECTION 4 DISASSEMBLY AND ASSEMBLY 74 b J1000 Cable J1000 Socket Location Connection ...
Page 77: ...SECTION 4 DISASSEMBLY AND ASSEMBLY 75 c J551 Cable J551 Socket Location Connection ...
Page 78: ...SECTION 4 DISASSEMBLY AND ASSEMBLY 76 d J703 Cable J703 Socket Location Connection ...
Page 79: ...SECTION 4 DISASSEMBLY AND ASSEMBLY 77 e P2002 Cable P2002 Socket Location Connection ...
Page 80: ...SECTION 4 DISASSEMBLY AND ASSEMBLY 78 f P2004 Cable P2004 Socket Location Connection ...
Page 81: ...SECTION 4 DISASSEMBLY AND ASSEMBLY 79 g P2006 Cable P2006 Socket Location Connection ...
Page 82: ...SECTION 4 DISASSEMBLY AND ASSEMBLY 80 h J35 Cable J35 Socket Location Connection ...
Page 83: ...SECTION 4 DISASSEMBLY AND ASSEMBLY 81 i P1 Cable P1 Socket Location Connection ...
Page 84: ...SECTION 4 DISASSEMBLY AND ASSEMBLY 82 j P2005 Cable P2005 Socket Location Connection ...
Page 85: ...SECTION 4 DISASSEMBLY AND ASSEMBLY 83 k P2003 Cable P2003 Socket Location Connection ...
Page 86: ...SECTION 4 DISASSEMBLY AND ASSEMBLY 84 l J20 Cable J20 Socket Location Connection ...
Page 87: ...SECTION 4 DISASSEMBLY AND ASSEMBLY 85 m J2001 Cable J2001 Socket Location Connection ...
Page 180: ......
Page 181: ...Copyright Neopost USA 2014 ...