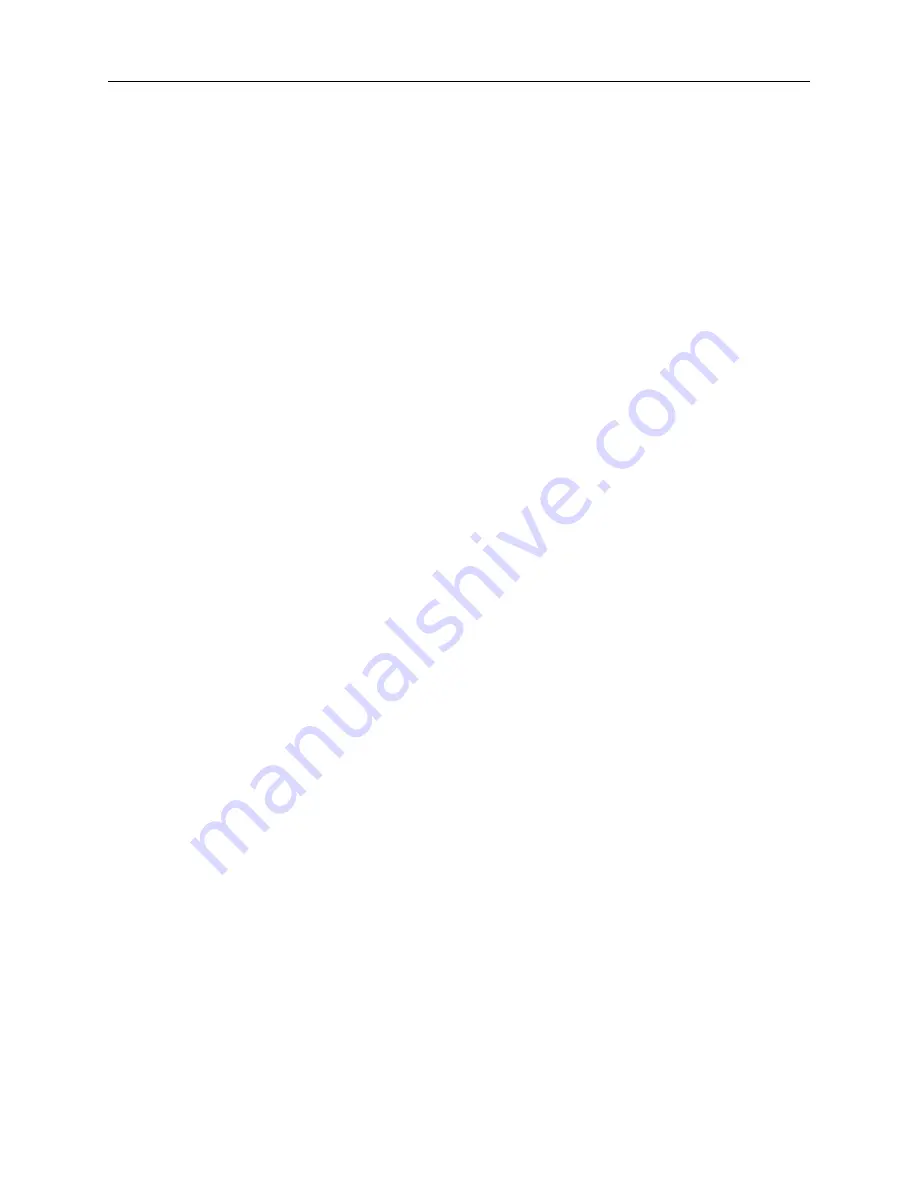
Mark V ProVis Injection System
13 - 2
Drive Systems
There are two motors and drive systems in the injector head: The
Syringe piston, and Automatic Mechanical Stop. The piston motor
(M1), is larger than the Mechanical Stop motor (M2). Both motors
incorporate belt drives for smooth, quiet operation.
Rotary motion of the piston motor (M1) is converted to linear motion
by a ballscrew. The Mechanical Stop Motor (M2), drives two acme
screws, one on each side of the piston. These acme screws move the
Mechanical Stop Plate between the ball nut plate and the front of the
head. The function of this drive system is to position the Mechanical
Stop as an over-volume prevention backup.
Feedback Pots
There are two independent feedback pots in the injector head which
share a common reference voltage. R1 monitors plunger position, and
R2 monitors Mechanical Stop position.
•
The wiper voltage from R1 is sent to the SCC, then buff-
ered and filtered to derive the plunger position signal. This
signal represents the actual plunger position.
•
The wiper voltage from R2 is sent to the Mechanical Stop
Drive Card and the SCC, representing the actual Mechani-
cal Stop position.
Syringe Heat
Maintainer
The syringe heat maintainer is used to maintain the temperature of
contrast media in the syringe. Syringe temperature is maintained
through thermostats, and an over-temperature sensor/indicator in the
pod. Supply voltage (+26 VDC) comes from the power supply. A 2-pin
connector allows quick replacement.
Forward/Reverse/
Enable Circuit
This circuit provides variable forward and reverse load speed control,
using a “soft pot” which varies voltage applied to the PDCI load circuit.
A “soft pot” is a flat, membrane-type potentiometer, that alters resis-
tance according to what point on the potentiometer is pressed. The
ENABLE button is a safeguard against accidental loading if either the
forward or reverse load button should fail in the closed position.
Forward/Reverse Loading:
When ENABLE is pressed, +15 volts is supplied to one side of the soft
pot; the other is connected to a voltage divider (referenced at 8.5
volts) through Q2. When both FORWARD and ENABLE are pressed,
soft pot wiper voltage is sent to RN1, then to transistor Q3. Q3 func-
tions as a emitter follower, to buffer the forward load command, before
it is sent to the PDCI. When REVERSE and ENABLE are pressed,
soft pot wiper voltage is sent to RN1, then to transistor Q5. Q5 also
functions as a emitter follower, buffering the reverse load (REV) com-
mand before it is sent to the PDCI. The voltage range of the Forward
or Reverse load command is +9.1 to 15 volts (slow to fast). If both
Forward and Reverse load are pressed, there is no piston movement.
Summary of Contents for ProVis Mark V
Page 1: ...Service Manual KMP 870 98411 T 205 Rev D...
Page 2: ......
Page 3: ......
Page 4: ......
Page 15: ...Operating Guide 3 1 3 Operating Guide...
Page 16: ...Mark V ProVis Injection System 3 2...
Page 30: ...Mark V ProVis Injection System 7 4 Figure 7 1 Block Diagram Servo Control Card...
Page 31: ...Servo Control Card 7 5...
Page 37: ...Mark V ProVis Injection System 9 4 Figure 9 1 Block Diagram Control Panel Digital Logic...
Page 39: ...Mark V ProVis Injection System 9 6 Figure 9 2 Block Diagram Control Panel DC to DC Converter...
Page 49: ...Mark V ProVis Injection System 10 10 NOTES...
Page 60: ...Injector Head 13 7 Figure 13 1 Block Diagram Head Card...
Page 61: ...Mark V ProVis Injection System 13 8 NOTES...
Page 64: ...Imaging System Interface 14 3 Figure 14 1 Connector Locations...
Page 67: ...Mark V ProVis Injection System 14 6 Figure 14 2 Block Diagram Imaging System Interface...
Page 71: ...Mark V ProVis Injection System 14 10 NOTES...