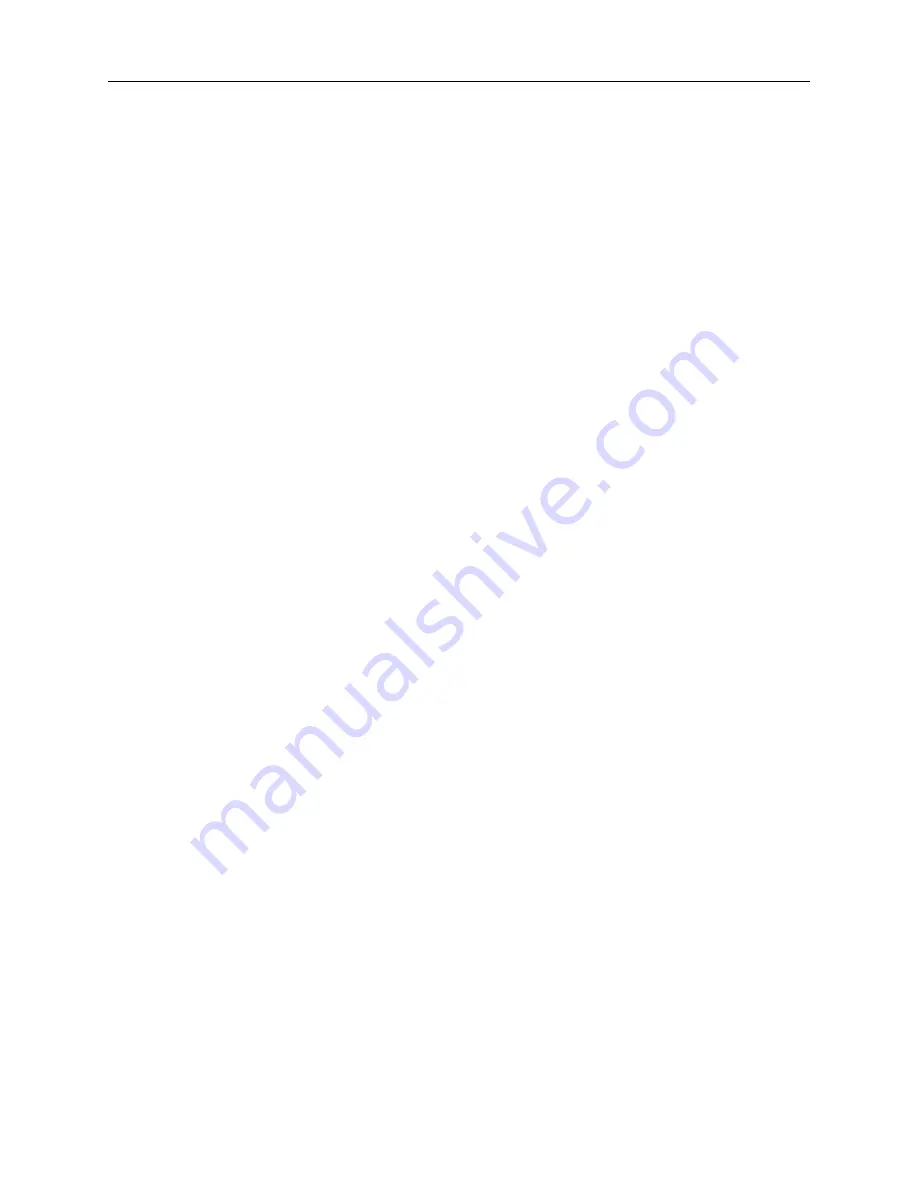
Power Drive Circuit
10 - 3
head is pressed, the signal will go through either D15 or D16, then
R59 and Q12, making Q13 conduct. This produces an active low
FWD/REV IND (to the SCC Card), which prompts the system to with-
draw the SAFRELEN.
Reverse Relay
Enable Circuits
K2, Q10, Q11
When Reverse loading, both Safe Relay K1 and Reverse Relay K2
must be energized. K2 reverses the polarity of the plunger. When
REVERSE load is pressed, Q11 and Q10 conduct, ap26 volts
through on-board jumper JU1, energizing K2. JU1 must be set in posi-
tion “1-2”.
System Override
The SYSTEM OVERRIDE shuts down the PDCI if the system detects
the presence of a “System Monitor’ type condition (Overpressure,
Overvolume, or Overrate [via Aux Monitor]). When the SYSTEM
OVERRIDE signal from U16 (PIO3) on the SCC goes high, Q4 and
Q5 (PDCI) conduct, al15 volts to: Disable the Safe Relay cir-
cuit (Q6), activate the brake (D2 and Q1), and disable pulses to the
SCR bridge controller (Q9). SYSTEM OVERRIDE and AUX MONI-
TOR are OR’ed on the PDCI to form a redundant shut-down circuit.
Zero Crossing
Detector
U4A, U4D
The Zero Crossing Detector circuit establishes a timing reference for
triggering of the SCR bridge. This is done by producing a positive
pulse (-10v to +10v) which resets Ramp Generator U5C when the
input sine-wave passes through zero. These pulses are also applied
to Full Error Trigger Q9, through D6 and R30, to fire the SCR bridge
when needed.
Input to this circuit is the added, positive half-waves, from the 36 VAC
created by a circuit on the Motherboard (MBRI), forming a full-wave
input to U4A. U4A, an inverting amplifier with a gain of 2.06, together
with D30 and C15, form a peak detector which produces an output
voltage proportional to the incoming line voltage. This voltage sets the
input reference for “Window Detector” U4D, which produces a positive
output pulse when the input sine-wave is below the reference estab-
lished by U4A (sine-wave passes through zero). All other times, the
output of U4D is negative saturation. The positive pulse, applied to the
gate of Q16, resets the Ramp Generator. The pulse width is approxi-
mately 1.2 mS @ 60 Hz, and 1.5 mS @ 50 Hz, and is clamped to +/-
10 volts by zener diodes D28 and D29 in the feedback loop of U4D.
Ramp Generator
U5C, Q16
Integrator U5C generates 2 volt (-2 to 0 volt) ramp waveforms
between each zero crossing that are used to establish a reference
level for Trigger Comparator U5B. DC level and amplitude of the
ramps are adjusted by R90 and R112, respectively. The integrator is
reset when the sine-wave passes through zero (U4D applies a posi-
tive pulse to the gate of Q16).
Summary of Contents for ProVis Mark V
Page 1: ...Service Manual KMP 870 98411 T 205 Rev D...
Page 2: ......
Page 3: ......
Page 4: ......
Page 15: ...Operating Guide 3 1 3 Operating Guide...
Page 16: ...Mark V ProVis Injection System 3 2...
Page 30: ...Mark V ProVis Injection System 7 4 Figure 7 1 Block Diagram Servo Control Card...
Page 31: ...Servo Control Card 7 5...
Page 37: ...Mark V ProVis Injection System 9 4 Figure 9 1 Block Diagram Control Panel Digital Logic...
Page 39: ...Mark V ProVis Injection System 9 6 Figure 9 2 Block Diagram Control Panel DC to DC Converter...
Page 49: ...Mark V ProVis Injection System 10 10 NOTES...
Page 60: ...Injector Head 13 7 Figure 13 1 Block Diagram Head Card...
Page 61: ...Mark V ProVis Injection System 13 8 NOTES...
Page 64: ...Imaging System Interface 14 3 Figure 14 1 Connector Locations...
Page 67: ...Mark V ProVis Injection System 14 6 Figure 14 2 Block Diagram Imaging System Interface...
Page 71: ...Mark V ProVis Injection System 14 10 NOTES...