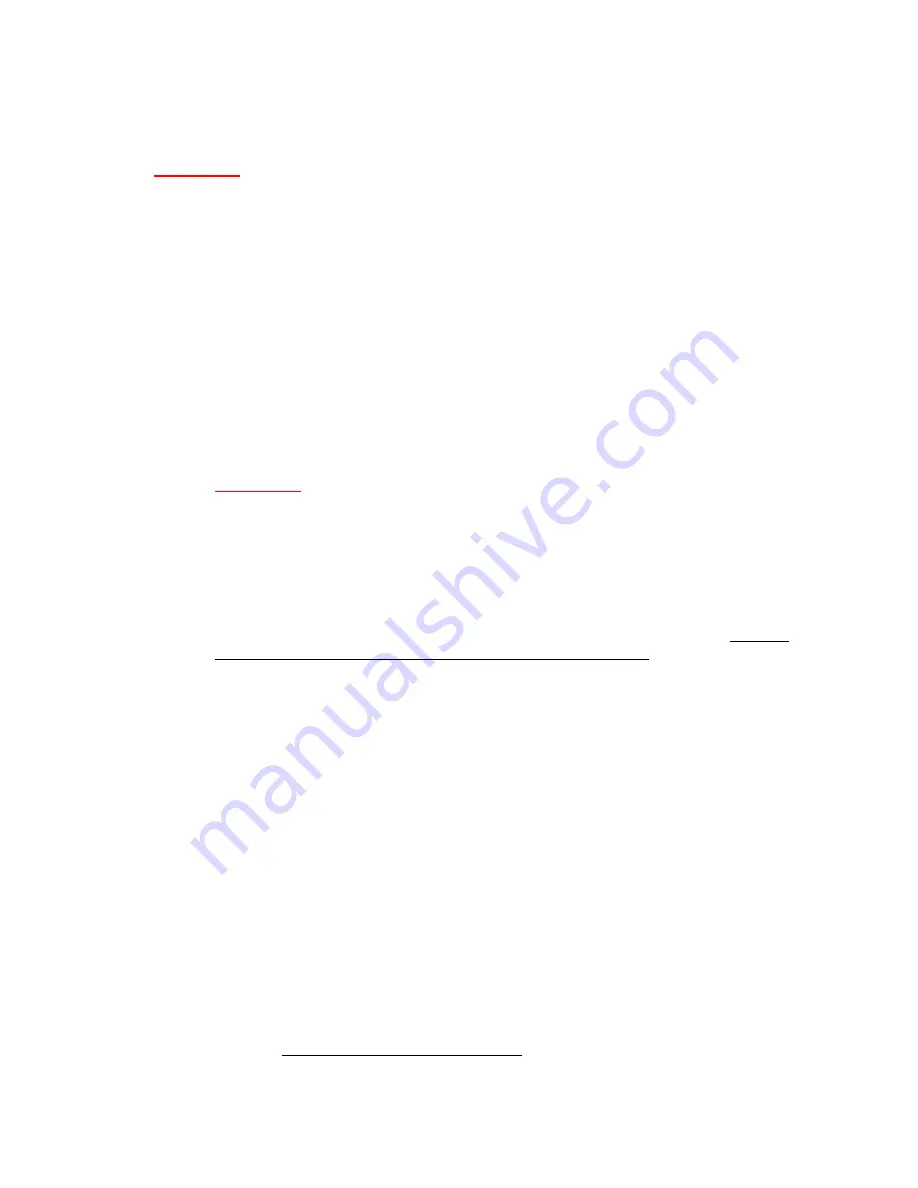
21
5.0
INSTALLATION TO ELECTRICAL AND GAS SERVICES. WELD HEAD CONNECTION.
EQUIPMENT WARNING LABELS
ATTENTION
: Inspect all precautionary labels on the equipment.
5.1
General Assembly Instructions
It is not always possible to install the Pipemaster in optimal environments for electrical
equipment. As much as possible, avoid locations exposed to high humidity, dust, high
ambient temperatures and corrosive fumes. Adequate air circulation is needed at all times.
Make sure that ventilation openings are unobstructed and provide a clearance of
approximately 30cm (12") around the unit of free air space.
5.2
Filling Model 905 Cooling Module with Coolant
(See Section 16 for further information on the Water Circulator Module and Integral Flow
Switch)
Fill the water tank with 8
R
(2 gallons) of Magnatech torch coolant fluid, P/N 7280, or
equivalent. This will provide freezing protection to -10
E
C (14
E
F). If this is unavailable, use
standard ethylene glycol (antifreeze) mixed 3 parts water to 1 part antifreeze.
ATTENTION
: A special mix allowing lower temperature use is available. Distilled or
demineralized water is strongly recommended to prevent bacterial and fungal
growth. The amount of cooling fluid required will depend on the cable length
of the weld Head. (It will be necessary to check the level of coolant after
several minutes of first turning on power to top up the coolant level as
required.)
5.3
Connecting Power Source to Input Power
Before proceeding further, carefully review all cautions covered in the section DO NOT
PROCEED FURTHER UNTIL YOU HAVE READ THIS SECTION.
The Power Source can be operated on any input voltage from 100 to 480 VAC, single phase
or 3 phase 50 - 60 Hz.
The Pipemaster comes equipped with a 2.4mm (8') input power cord.
Wire an appropriate connector to the end of the power input cable. Please note that the
green/yellow wire is "ground". Always connect the Pipemaster to line using a fused
disconnect switch.
WARNING: ELECTRIC SHOCK CAN KILL. DO NOT MAKE ANY CONNECTIONS OR
PERFORM ANY ELECTRICAL MAINTENANCE INSIDE PIPEMASTER WHILE UNIT IS
CONNECTED TO A POWER LINE
5.4
Connecting Pipemaster Power Source to Gas Supply
Connect the inlet gas hose provided to the brass quick-disconnect coupling on the rear
panel of the Pipemaster marked "Gas In". A pressure regulator/flowmeter of appropriate
flow rating should be used (customer provided).
An internal gas solenoid is mounted within the Pipemaster. Control circuitry sequences pre
and post purge time periods with the operation of the weld Head.
5.4.1
Compressed Gas Cylinder Handling