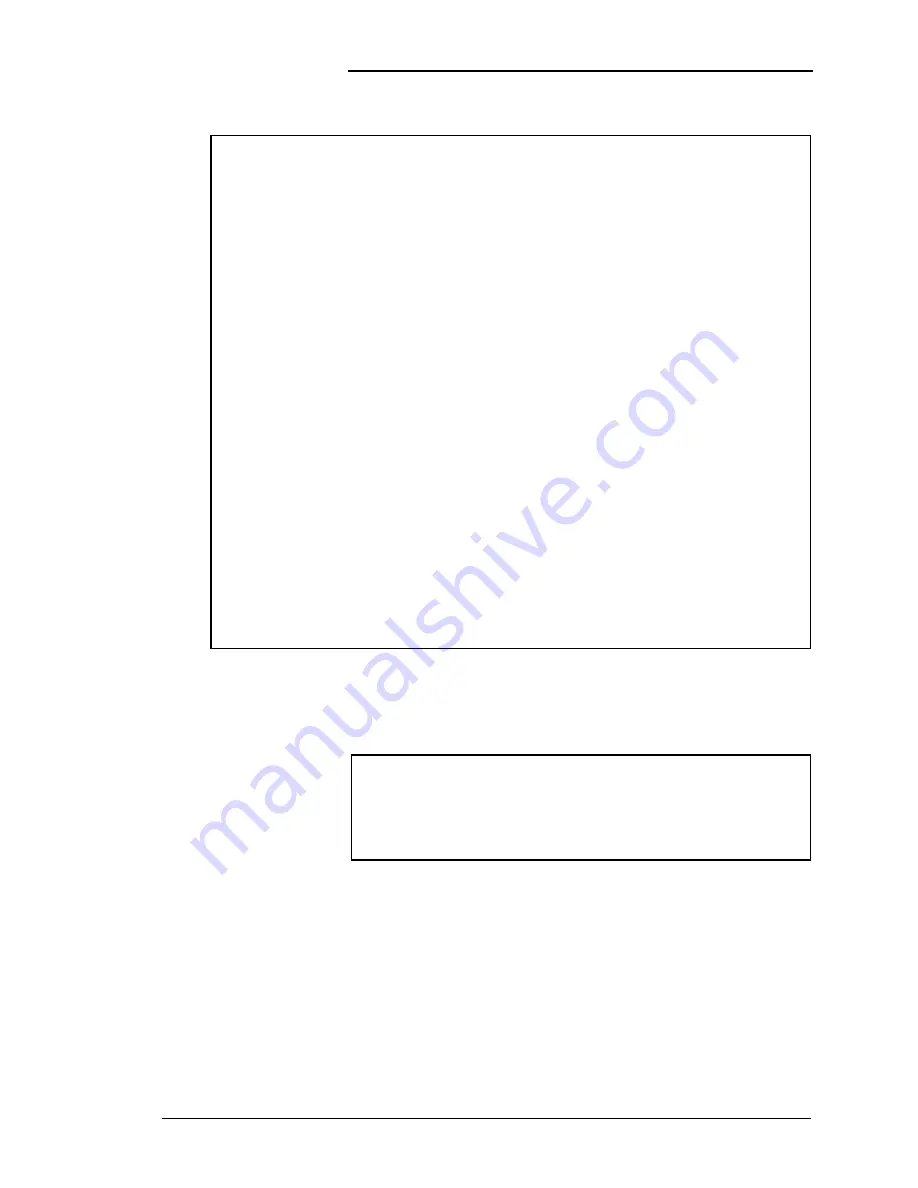
Lucent Technologies Lineage
®
2000 125A Ferroresonant Rectifier J85502C-1
Issue 8 July 1999
Spare Parts and Replacement Procedures 8 - 13
Replacing
Components
Disconnect the rectifier as described in “Disconnecting a
Rectifier” in this section. Refer to Figures 5-3 and 8-1 for
component locations and to the diagram on the inside of the
rectifier door.
Notes:
1. Slotted machine screws should be the pan-head type.
2. Slotted machine and hex cap screws should be SAE Grade 2 steel or
equivalent.
3. Socket cap screws should have 100,000 psi minimum tensile strength.
4. Steel flat washers should be furnished under heads of socked cap screws.
5. Ferrous screws and washers should have a corrosion protective finish.
6. Locking means is only required for connections subject to vibration.
Belleville type washers or jam nuts are the preferred means.
7. For less that 1/4 inch thick tapped copper bars, use slotted No. 8, No. 10, or
1/4-inch machine screws to minimize applicable torque. When larger size
screws are required, provide captive-type steel nuts or reduce torques.
8. Torque recommendations are also suitable for all non-ferrous fasteners,
except aluminum.
9. Where application permits, hex cap screws should be used.
Table 8-E: Minimum Torque for all Electrical Connections
DANGER
The following disassembly or reinstallation procedures MUST
be performed only on a rectifier completely disconnected from
the plant battery buses, AND with no input from the ac service
panel connected to the rectifier. The plant control cable J2A
should also be disconnected from the CM2 board.