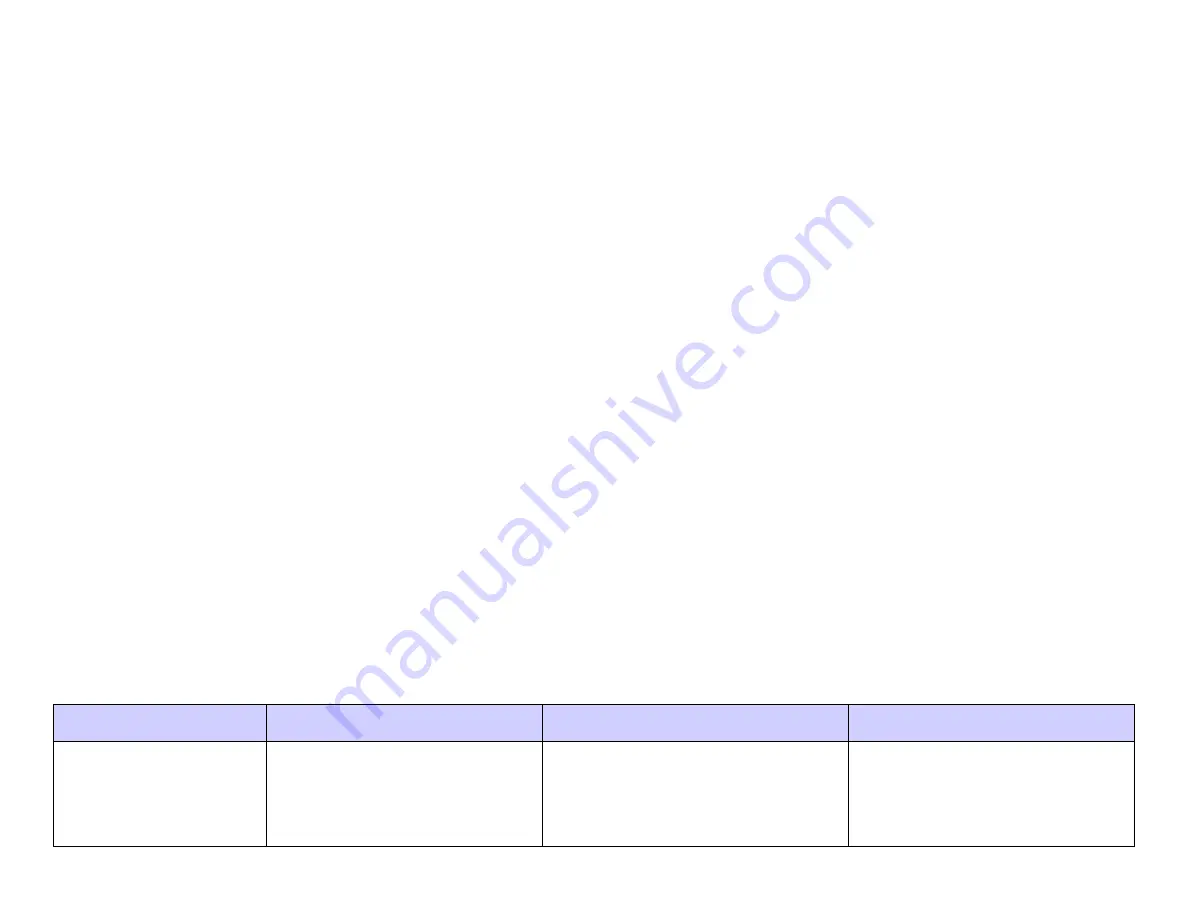
a sensor at the exact same location. For example do not attempt to calibrate a ceiling mounted temperature sensor by measuring air temperature near the
floor. The calibration may be off by ten (10) degrees or more.
Sensor Calibration Procedure
To calibrate a sensor:
1. From the Configuration and Diagnostics menu, select Calibrate Sensors.
2. Select the desired sensor to display its calibration settings.
3. Type in the new, accurate reading in the Enter Correct Value setpoint and then select Save Changes.
The Span and Offset adjustments are automatically recalculated and permanently saved to the Agility unit. Span describes the pre-programmed range in
proportion to the electrical signal (typically 4-20ma). Offset defines the "starting point" by comparing the minimum range value with the electrical
signal. Because both factors are dynamically adjusted, calibration is most effective when the sensor is close to either extreme of its sensing range, i.e. calibrate a
0 - 300 PSIG pressure sensor when the pressure is at or near 0 PSIG then again at or near 300 PSIG.
Analog Output Troubleshooting
The Agility Controller’s two analog outputs generate an active 4-20mA signal to control variable speed or position devices including modulating valves and
variable speed motors. Since the Agility Controller
actively
generates the control signal, no other source of power should be connected to the current loop.
Additionally, each 4-20mA current loop is optically isolated to eliminate troublesome ground loop conditions.
The surest method to determine if the analog output is functional is to entirely remove the field wiring from the pair of analog output terminals and, using a high
quality digital DC milliamp meter, directly measure the signal. A reading between 4mA and 20mA indicates a functional analog output.
Digital Output Troubleshooting
Digital Outputs are solid state relays driven by an isolated low voltage signal from the Agility microcontroller. Some sections also apply to a faulty Input module.
Problem
Test
Possible Solution
Comments
Digital Output fails
to energize.
Verify that the microcontroller is
trying to energize the output by
viewing View I/O Status.
Enable (or disable) the control
mechanism that energizes the
output.
Some outputs, such as suction
pilot valves or compressor
unloaders may be energized when
the control routine is off ("Reverse
Logic").