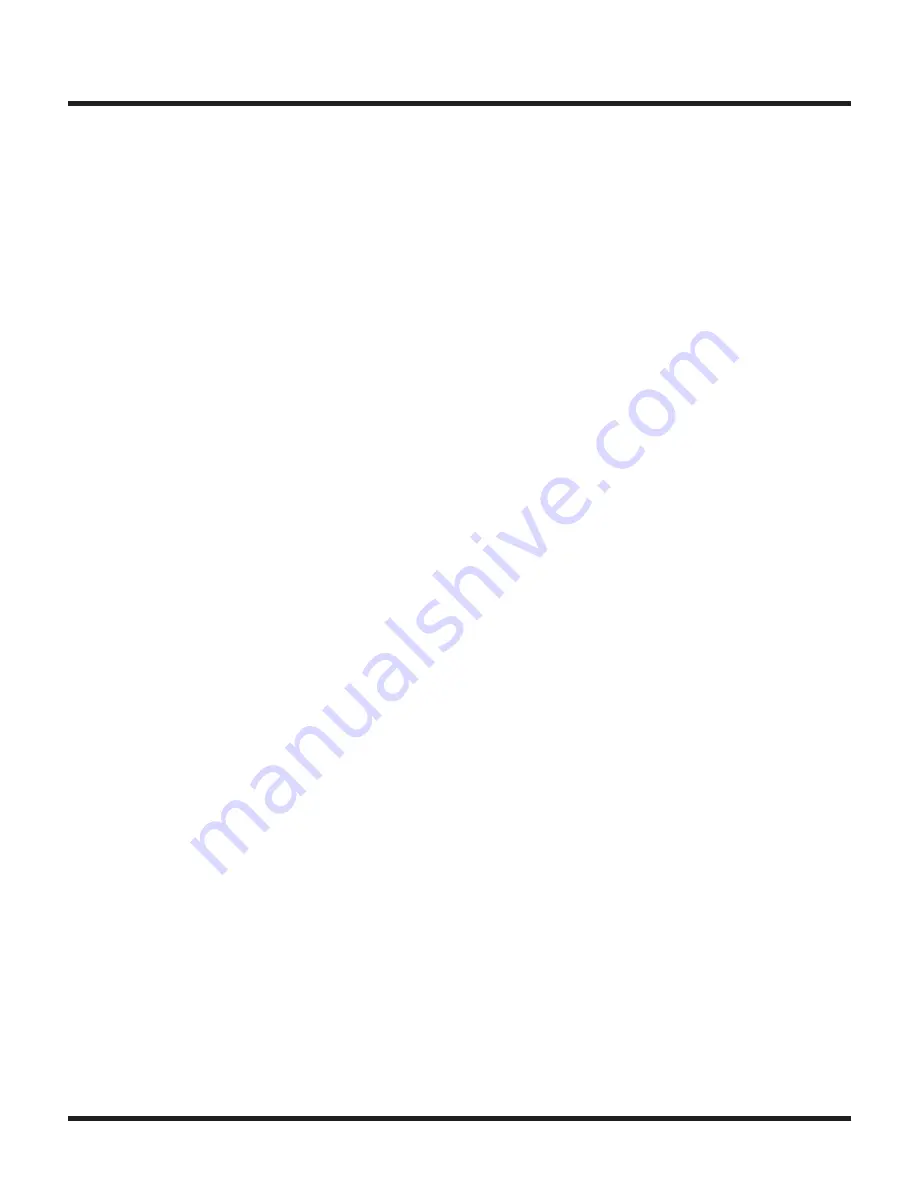
LTC3115-1
15
Rev. C
OPERATION
Reverse Current Limit
In PWM mode operation, the LTC3115-1 synchronously
switches all four power devices. As a result, in addition to
being able to supply current to the output, the converter
has the ability to actively conduct current away from the
output if that is necessary to maintain regulation. If the
output is held above regulation, this could result in large
reverse currents. This situation can occur if the output
of the LTC3115-1 is held up momentarily by another
supply as may occur during a power-up or power-down
sequence. To prevent damage to the part under such con-
ditions, the LTC3115-1 has a reverse current comparator
that monitors the current entering power switch D from
the load. If this current exceeds 1.5A (typical) switch D
is turned off for the remainder of the switching cycle in
order to prevent the reverse inductor current from reach-
ing unsafe levels.
Output Current Capability
The maximum output current that can be delivered by the
LTC3115-1 is dependent upon many factors, the most
significant being the input and output voltages. For V
OUT
= 5V and V
IN
≥ 3.6V, the LTC3115-1 is able to support
up to a 1A load continuously. For V
OUT
= 12V and V
IN
≥
12V, the LTC3115-1 is able to support up to a 2A load
continuously. Typically, the output current capability is
greatest when the input voltage is approximately equal
to the output voltage. At larger step-up voltage ratios, the
output current capability is reduced because the lower
duty cycle of switch D results in a larger inductor current
being needed to support a given load. Additionally, the
output current capability generally decreases at large step-
down voltage ratios due to higher inductor current ripple
which reduces the maximum attainable inductor current.
The output current capability can also be affected by
inductor characteristics. An inductor with large DC resis-
tance will degrade output current capability, particularly
in boost mode operation. Larger value inductors generally
maximize output current capability by reducing induc-
tor current ripple. In addition, higher switching frequen-
cies (especially above 750kHz) will reduce the maximum
output current that can be supplied (see the Typical
Performance Characteristics for details).
Burst Mode OPERATION
When the PWM/SYNC pin is held low, the buck-boost
converter employs Burst Mode operation using a vari-
able frequency switching algorithm that minimizes the
no-load input quiescent current and improves efficiency
at light load by reducing the amount of switching to the
minimum level required to support the load. The output
current capability in Burst Mode operation is substantially
lower than in PWM mode and is intended to support light
standby loads (typically under 50mA). Curves showing
the maximum Burst Mode load current as a function of
the input and output voltage can be found in the Electrical
Characteristics section of this data sheet. If the converter
load in Burst Mode operation exceeds the maximum Burst
Mode current capability, the output will lose regulation.
Each Burst Mode cycle is initiated when switches A and
C turn on producing a linearly increasing current through
the inductor. When the inductor current reaches the Burst
Mode current limit (1A typically) switches B and D are
turned on, discharging the energy stored in the inductor
into the output capacitor and load. Once the inductor cur-
rent reaches zero, all switches are turned off and the cycle
is complete. Current pulses generated in this manner are
repeated as often as necessary to maintain regulation of
the output voltage. In Burst Mode operation, the error
amplifier is not used but is instead placed in a low current
standby mode to reduce supply current and improve light
load efficiency.
SOFT-START
To minimize input current transients on power-up, the
LTC3115-1 incorporates an internal soft-start circuit with
a nominal duration of 9ms. The soft-start is implemented
by a linearly increasing ramp of the error amplifier refer-
ence voltage during the soft-start duration. As a result,
the duration of the soft-start period is largely unaffected
by the size of the output capacitor or the output regula-
tion voltage. Given the closed-loop nature of the soft-start
implementation, the converter is able to respond to load
transients that occur during the soft-start interval. The
soft-start period is reset by thermal shutdown and UVLO
events on both V
IN
and V
CC
.