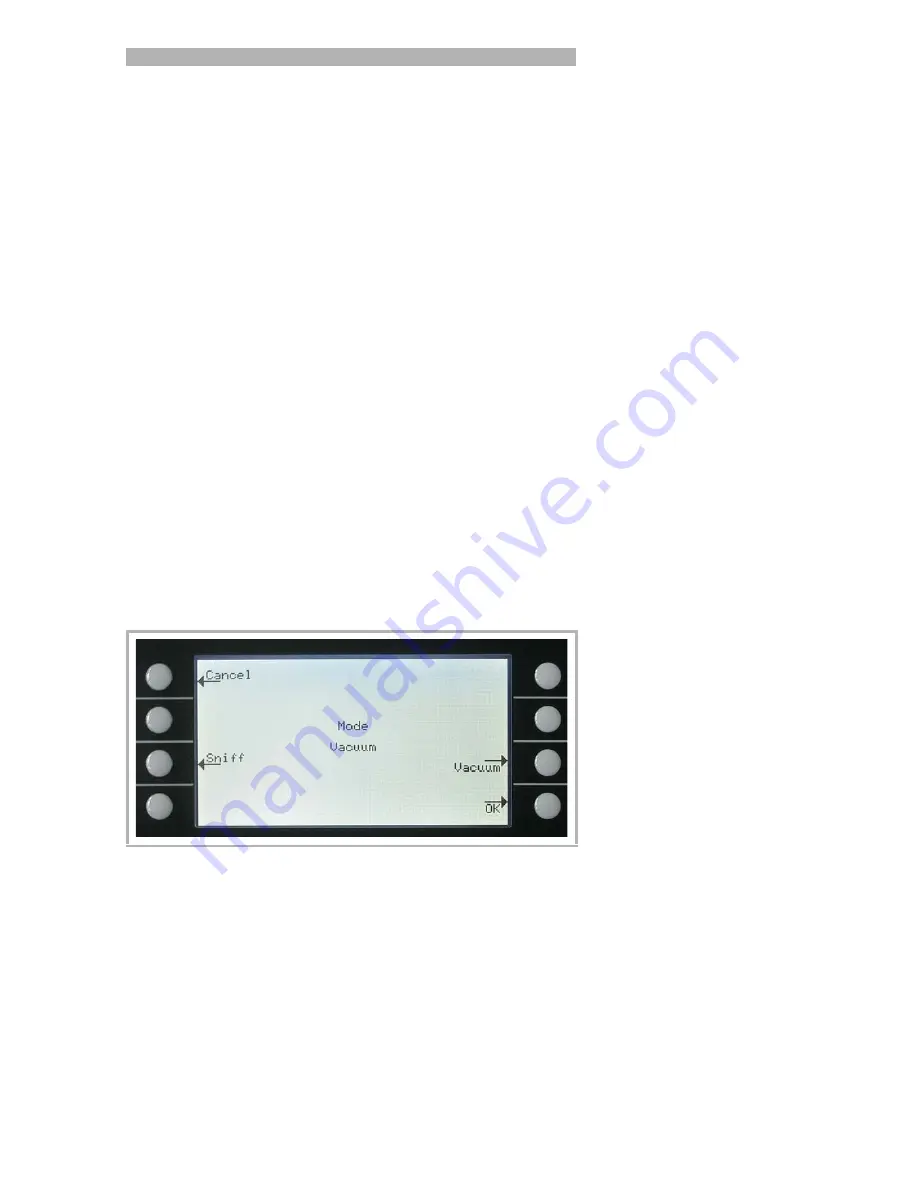
Head
GA10218_0101 - 5/2002
⏐
54
the net leak rate from the part under test is measured.
When switched to Stand-by / Vent again a new internal background is cal-
culated after 25 s. The updated value is underlined. This means that if you
press START when the value is underlined, the actual background signal
will be subtracted. If you press START when the value is not underlined,
the old background signal from the last Stand-by will be subtracted.
6.2.6 Lower display limit
Main menu
>
View
>
Lower display limit
This mode limits the lower detection limit of the measured leak rate. This is
valid for vacuum mode only.
6.3 Mode
Main menu
>
Mode
The mode menu
Fig. 19
enables the submenu to select the different wor-
king modes.
Softkey 3, 7:
↑ ↓
Changing of the lower detection limit between 1 · 10
-9
and 1 · 10
-12
The lower limit for the PhoeniXL
300 dry
ranges between 1 · 10
-9
and 1 · 10
-
11
mbarl/s.
Softkey 5:
?
Help text
Fig. 19 Display: Mode Menu