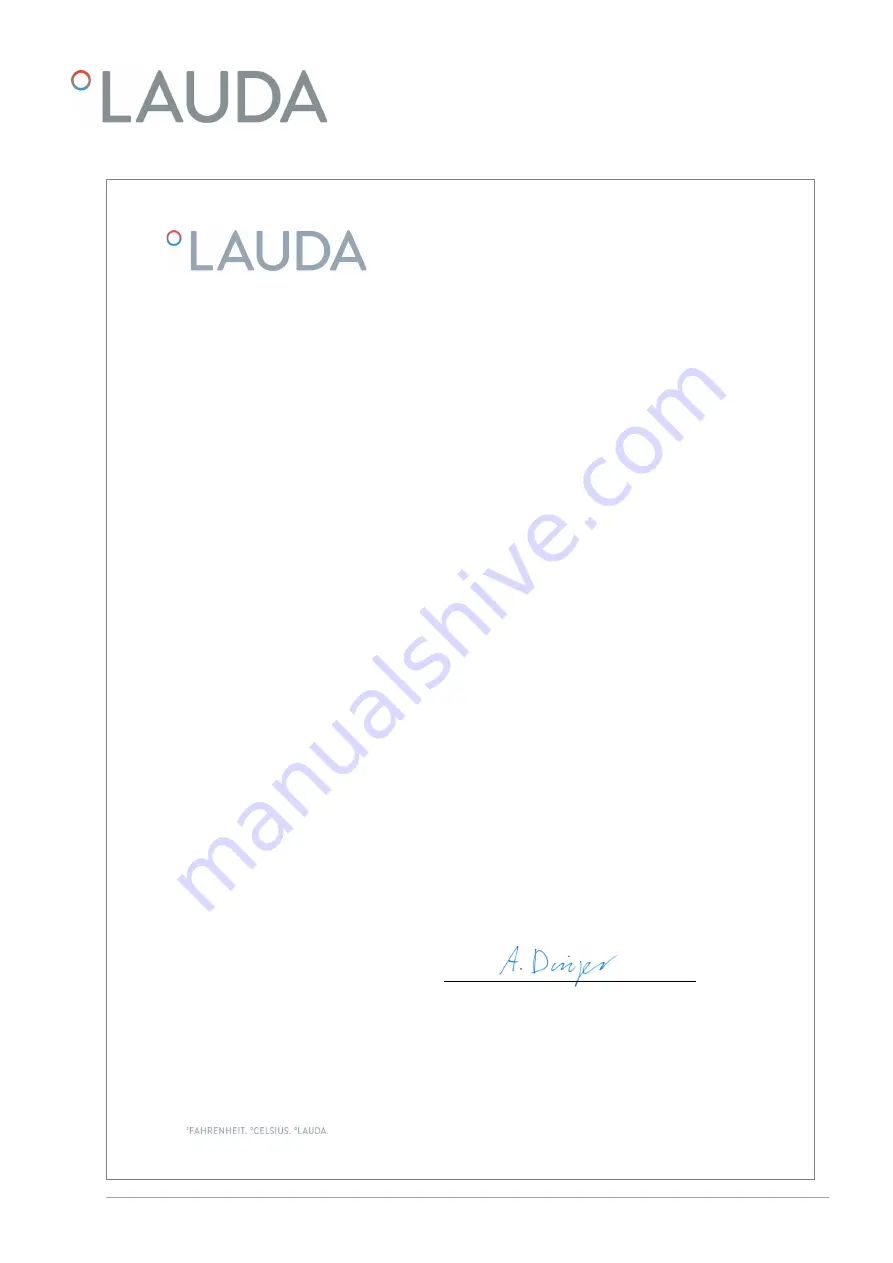
Document number: Q5WA-QA13-020-EN Version 01
EC DECLARATION OF INCORPORATION
Manufacturer: LAUDA DR. R. WOBSER GMBH & CO. KG
Pfarrstrasse 41/43 97922 Lauda-Königshofen Germany
We hereby declare under our sole responsibility that the machines described below
Product Line:
MID 80
Serial number: from S210000001
comply with all relevant provisions of the EC Directives listed below due to their design and type of construction in
the version brought on the market by us:
Machinery Directive
2006/42/EC
Low voltage directive
2014/35/EU
EMC Directive
2014/30/EU
RoHS Directive
2011/65/EU
The equipment is not covered by the Pressure Equipment Directive 2014/68/EU, as the maximum classification of
the equipment is Category 1 and it is covered by the Machinery Directive.
The protective objectives of the Machinery Directive with regard to electrical safety are complied with in accordance
with Annex I Paragraph 1.5.1 in conformity with the Low Voltage Directive 2014/35/EU.
The equipment may only be operated when incorporated or connected in accordance with the operating instructions,
and must not be put into service until the final machinery, into which it is to be incorporated or connected, has been
declared in conformity with the relevant provisions of the Machinery Directive 2006/42/EC.
Applied harmonized standards:
•
EN ISO 12100:2010
•
EN 61326-1:2013
•
EN 61010-1:2010/A1:2019/AC:2019-04
Authorized representative for the composition of the technical documentation:
Dr. Jürgen Dirscherl, Head of Research & Development
Lauda-Königshofen, 25.01.2021
Dr. Alexander Dinger, Head of Quality Management
V2
Flow controller MID 80
35 / 38