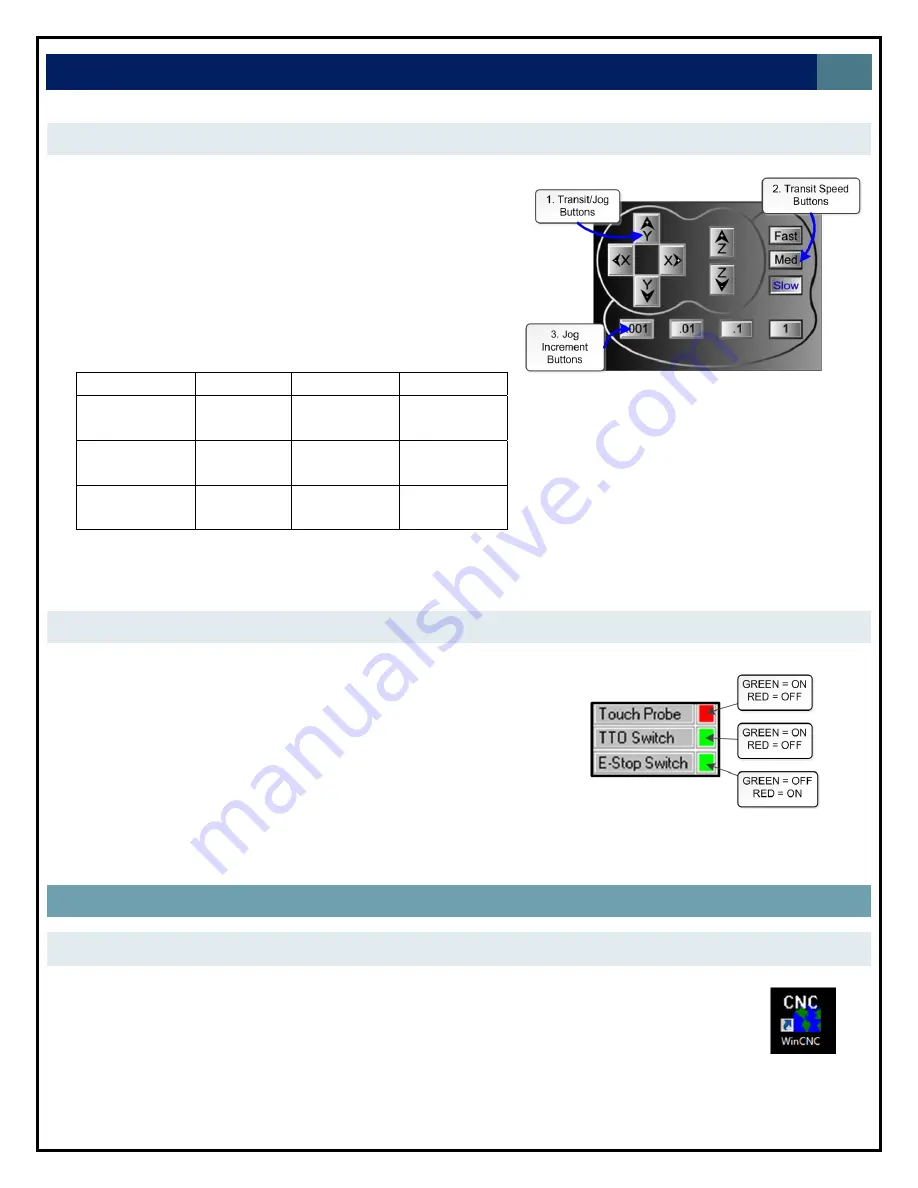
LAGUNA
TOOLS
18
TRANSIT
SPEED
BUTTONS
1.
Transit/Jog
Buttons
1.1.
Manual
transit
buttons.
Hold
the
directional
button
down
to
continuously
move
the
machine.
2.
Transit
Speed
Buttons
2.1.
Allows
the
user
to
adjust
between
three
predefined
transit
speeds.
The
speeds
can
vary
for
each
axis.
The
table
below
shows
the
default
settings.
Transit
Speed
Fast
Med
Slow
X
400
in/min
200
in/min
50
in/min
Y
400
in/min
200
in/min
50
in/min
Z
100
in/min
50
in/min
25
in/min
3.
Jog
increment
Buttons
3.1.
These
buttons
allow
you
to
specify
the
increment
of
a
jog
move.
The
default
unit
of
measure
is
inches.
INPUT
INDICATORS
1.
Touch
Probe
–
Indicates
if
touch
probe
has
been
triggered.
2.
TTO
Switch
–
Indicates
whether
or
not
the
tool
touch
pad
has
been
grounded.
3.
E
‐
Stop
Switch
–
Indicates
if
the
Emergency
Stop
Switch
has
been
triggered.
BASIC
MACHINE
OPERATIONS
TURNING
ON
THE
MACHINE
1.
Power
ON
the
PC.
2.
Start
WinCNC
by
either
clicking
on
the
desktop
shortcut,
or
locating
the
executable
file
winCNC.exe
on
the
(C:)
drive
in
the
WinCNC
folder.
Figure
16.
Controller
transit/jog
buttons
Figure
17.
Controller
feedback
indicators
Figure
18.
WinCNC
desktop
shortcut
Summary of Contents for CNC Swift Series
Page 54: ...LAGUNA TOOLS 54 SPECIFICATIONS...