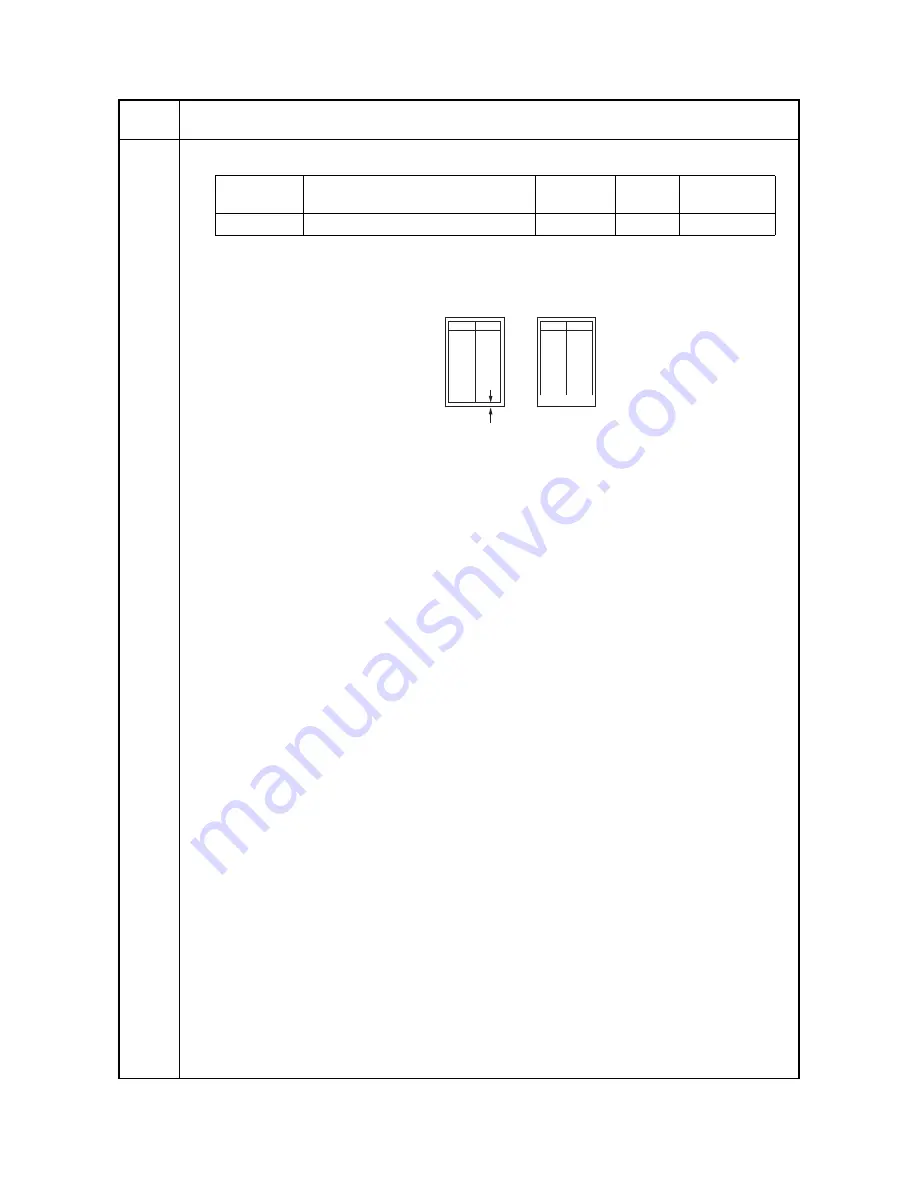
3MH
1-3-19
U034
Adjustment: Trailing edge margin adjustment
1. Select [MGN REAR].
2. Press the interrupt key.
3. Press the start key to output a test pattern.
4. Change the setting value using the cursor left/right keys.
For output example, increase the value.
Figure 1-3-9
5. Press the start key. The value is set.
Completion
Press the stop/clear key. The screen for selecting a maintenance item No. is displayed.
Maintenance
item No.
Description
Display
Description
Setting
range
Initial
setting
Change in
value per step
MGN REAR
Trailing edge margin adjustment
-4.0 to 10.0
2.0
0.1 ms
Correct image
Output
example
Trailing edge margin
Summary of Contents for DF-420
Page 3: ...Revision history Revision Date Replaced pages Remarks ...
Page 4: ...This page is intentionally left blank ...
Page 10: ...This page is intentionally left blank ...
Page 11: ...First Edition DP 420 ...
Page 17: ...3MX 1 1 4 This page is intentionally left blank ...
Page 21: ...3MX 1 2 4 This page is intentionally left blank ...
Page 65: ...3MX 1 5 10 This page is intentionally left blank ...
Page 69: ...3MX 2 1 4 This page is intentionally left blank ...
Page 82: ...First Edition PF 420 ...
Page 87: ...3MH 1 1 3 1 1 3 Machine cross section Figure 1 1 2 Machine cross section Paper path ...
Page 88: ...3MH 1 1 4 This page is intentionally left blank ...
Page 94: ...3MH 1 2 6 This page is intentionally left blank ...
Page 128: ...3MH 1 4 12 This page is intentionally left blank ...
Page 136: ...3MH 1 5 8 This page is intentionally left blank ...
Page 142: ...3MH 2 2 4 This page is intentionally left blank ...
Page 146: ...3MH 2 3 4 This page is intentionally left blank ...
Page 149: ...First Edition DF 420 ...
Page 151: ...3MJ This page is intentionally left blank ...
Page 155: ...3MJ 1 1 4 This page is intentionally left blank ...
Page 159: ...3MJ 1 2 4 3 Remove the tape from the process table Figure 1 2 4 Tape Process table ...
Page 175: ...3MJ 1 5 4 This page is intentionally left blank ...
Page 181: ...3MJ 2 1 6 This page is intentionally left blank ...
Page 185: ...3MJ 2 2 4 This page is intentionally left blank ...
Page 192: ...First Edition JS 420 ...
Page 194: ...3MK This page is intentionally left blank ...
Page 196: ...3MK 1 1 2 1 1 2 Parts names Figure 1 1 1 1 2 1 Job separator tray 2 LED ...
Page 197: ...3MK 1 1 3 1 1 3 Machine cross section Figure 1 1 2 Machine cross section Paper path ...
Page 198: ...3MK 1 1 4 This page is intentionally left blank ...
Page 212: ...3MK 2 2 2 This page is intentionally left blank ...
Page 215: ...First Edition FAX System R ...
Page 217: ...3MZ This page is intentionally left blank ...
Page 227: ...3MZ 1 2 4 This page is intentionally left blank ...
Page 285: ...3MZ 1 6 2 This page is intentionally left blank ...
Page 287: ...3MZ 2 1 2 This page is intentionally left blank ...
Page 293: ...3MZ 2 2 6 This page is intentionally left blank ...
Page 295: ...3MZ 2 3 2 This page is intentionally left blank ...
Page 296: ......