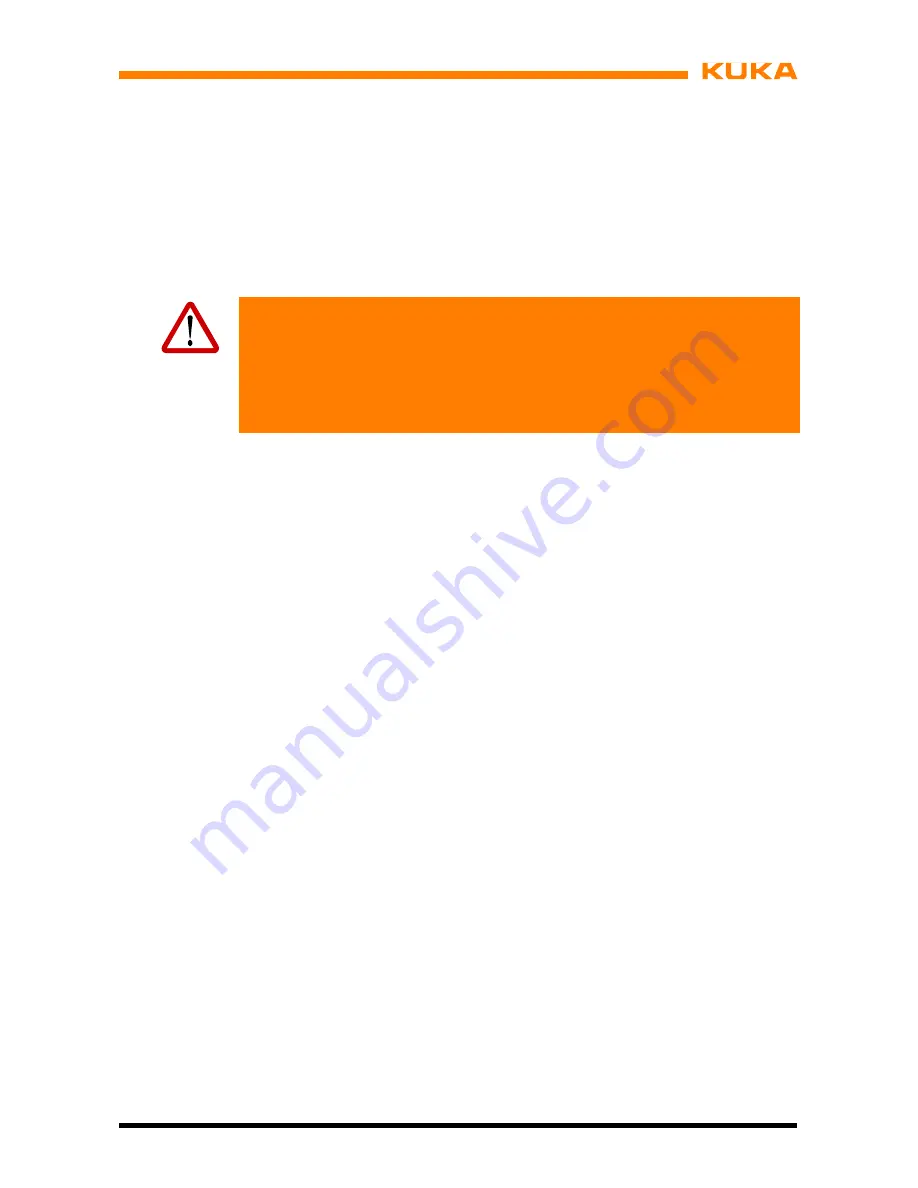
5
Safety (continued)
53 of 122
MA KR 30, 60 HA, KR C4 04.11.02 en
KCP/smartPAD
The user must ensure that the industrial robot is only operated with the KCP/smartPAD by
authorized persons.
If more than one KCP/smartPAD is used in the overall system, it must be ensured that each
device is unambiguously assigned to the corresponding industrial robot. They must not be
interchanged.
Warning!
The operator must ensure that decoupled KCPs/smartPADs are immediately
removed from the system and stored out of sight and reach of personnel
working on the industrial robot. This serves to prevent operational and
non--operational EMERGENCY STOP devices from becoming interchanged.
Failure to observe this precaution may result in death, severe injuries or
considerable damage to property.
External keyboard, external mouse
An external keyboard and/or external mouse may only be used if the following conditions are
met:
G
Start--up or maintenance work is being carried out.
G
The drives are switched off.
G
There are no persons in the danger zone.
The KCP/smartPAD must not be used as long as an external keyboard and/or external
mouse are connected to the control cabinet.
The external keyboard and/or external mouse must be removed from the control cabinet as
soon as the start--up or maintenance work is completed or the KCP/smartPAD is connected.
Modifications
After modifications to the industrial robot, checks must be carried out to ensure the required
safety level. The valid national or regional work safety regulations must be observed for this
check. The correct functioning of all safety circuits must also be tested.
New or modified programs must always be tested first in Manual Reduced Velocity mode
(T1).
After modifications to the industrial robot, existing programs must always be tested first in
Manual Reduced Velocity mode (T1). This applies to all components of the industrial robot
and includes modifications to the software and configuration settings.
Faults
The following tasks must be carried out in the case of faults in the industrial robot:
G
Switch off the robot controller and secure it (e.g. with a padlock) to prevent unauthorized
persons from switching it on again.
G
Indicate the fault by means of a label with a corresponding warning (tagout).
G
Keep a record of the faults.
G
Eliminate the fault and carry out a function test.
Summary of Contents for KR 30 HA
Page 6: ...Assembly Instructions 6 of 122 MA KR 30 60 HA KR C4 04 11 02 en...
Page 8: ...Assembly Instructions 8 of 122 MA KR 30 60 HA KR C4 04 11 02 en...
Page 22: ...Assembly Instructions 22 of 122 MA KR 30 60 HA KR C4 04 11 02 en...
Page 42: ...Assembly Instructions 42 of 122 MA KR 30 60 HA KR C4 04 11 02 en...
Page 60: ...Assembly Instructions 60 of 122 MA KR 30 60 HA KR C4 04 11 02 en...
Page 84: ...Assembly Instructions 84 of 122 MA KR 30 60 HA KR C4 04 11 02 en...
Page 96: ...Assembly Instructions 96 of 122 MA KR 30 60 HA KR C4 04 11 02 en...
Page 106: ...Assembly Instructions 106 of 122 MA KR 30 60 HA KR C4 04 11 02 en...