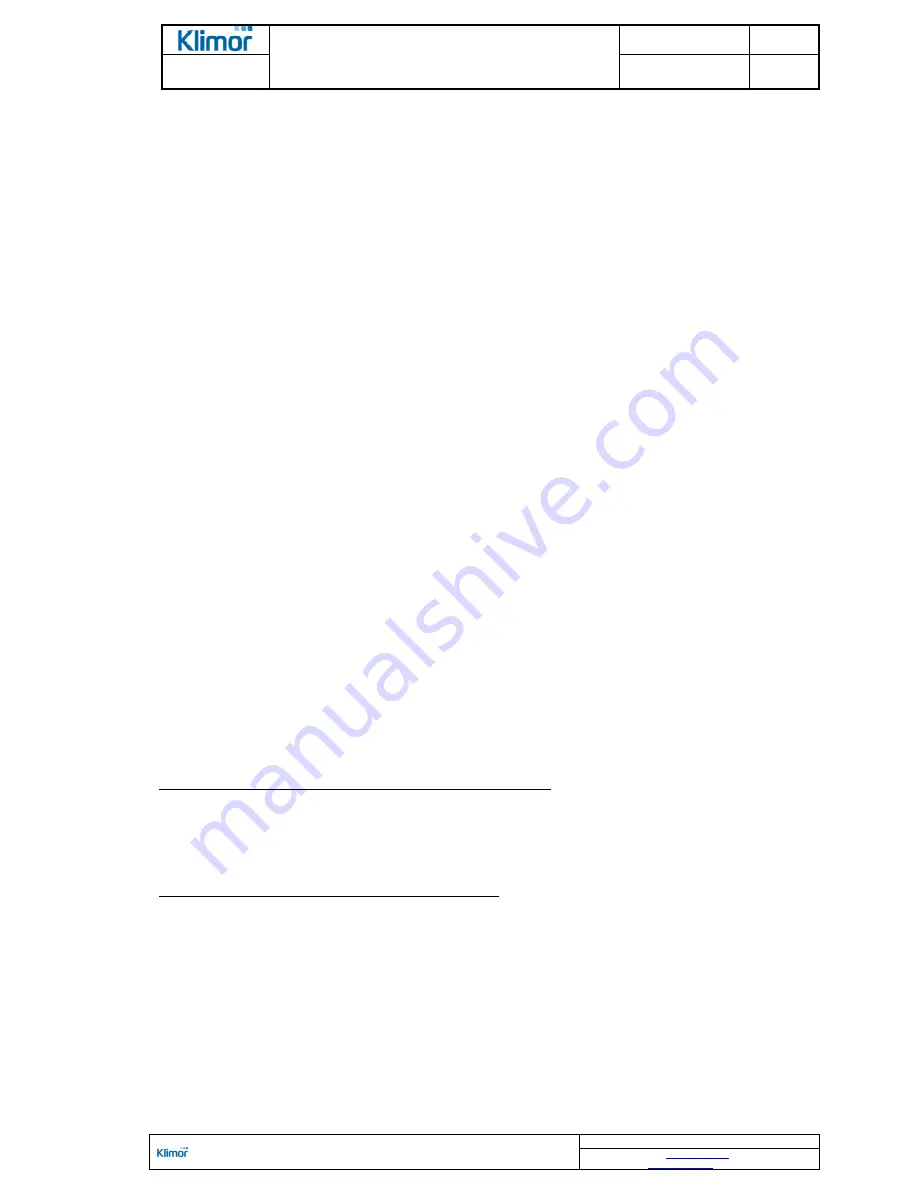
OPERATION AND MAINTENANCE MANUAL
DTR MCK v.2.4
PAGE
GDYNIA
MODULAR AIR HANDLING UNITS
MCKS, MCKH, MCKP
2017 EN
36/45
KLIMOR Spółka z ograniczon
ą
odpowiedzialno
ś
ci
ą
Sp.k., 81-035 Gdynia, ul. B. Krzywoustego 5
Fax: (+48 58) 783-98-88; Tel.: (+48 58) 783-99-99
Service -
Fax: (+48 58) 783-98-88; Tel.: (+48 58) 783-99-50/51 Mobile: (+48) 510 098 081
Information in this document is subject to change
email:
-
office
-
service
d)
DX cooler
The maintenance is similar to the water cooler, allowing for the following indications: before washing the direct expansion (DX) cool-
er with warm water it is necessary to suck out the medium from the cooling system. Otherwise the gas pressure may increase which
may damage the system.
If any scale residues are observed in the drip tray, wash it with water with addition of descaling agent. Wash the cooler droplet sepa-
rator with warm water with detergent and also with descaling agent, if necessary.
Replacement of CuAl exchangers in case of their failure is possible after removing the covers and bolts or screws fixing the ex-
changer to the AHU partitions. In the order for a new exchanger please indicate its full designation which is located at the rating
plate.
e) Cross-flow exchanger
The cross-flow exchanger is subject to technical inspection every four months. Aluminum fins get contaminated and excess soil may
accumulate on the plate edges (down to a depth of 50mm).
Before cleaning cross-flow exchanger sections, the neighboring sections should be secured.
Clean with a vacuum cleaner with a soft suction nozzle on the side of air inlets or blow through with air in the direction opposite to
the airflow in the exchanger. It is acceptable to wash the fins with water and cleaning agent that does not cause aluminum corrosion
or to rinse them with a water jet under heavy pressure (for considerable dirt).
When performing all the operations, care should be taken so as not to deform the aluminum plates.
If maintenance and cleaning of the exchanger is done in outdoor temperature below 0
°
C, the unit should be completely dried before
restart.
During the inspection you also have to check operation and cleanliness of the dampers, droplet separator and drip tray and check if
the condensate outlet is not obstructed.
f) Rotary exchanger
The rotary exchanger is subject to technical inspection every 6 months. The aluminum fins become contaminated. Before cleaning
rotary exchanger sections, the neighboring sections should be secured.
Clean with a vacuum cleaner with a soft suction nozzle on the side of air inlets or blow through with air in the direction opposite to
the airflow in the exchanger.
The rotary exchanger drive belt is an operating element and if incorrect tightness is observed, it has to be replaced.
The rotary exchanger in the standard AHU version (standard AHU version has got dimensions as stated in the
Table No. 1
) is
equipped with a spare belt. If the exchanger version does not involve a spare rotor drive belt, contact the service department in or-
der to determine its type and length
.
8.4 Silencer
The silencing section is fitted with slotted levers filled with non-flammable mineral wool and they should be checked for cleanliness.
The slotted levers are removable, but they may be cleaned when they are in the AHU.
Clean with a vacuum cleaner with a soft suction nozzle.
8.5 Humidifier
The humidification section should be washed with warm water with detergent. If any scale residues are observed in the drip tray,
wash it with water with addition of descaling agent.
8.6 Fan
Prior to commencing any works on the unit and when removing the inspection panels, one should make sure that the
unit has been disconnected from power supply, the rotor is not turning, the fan motor has cooled down and that the
system has been secured against accidental start-up.
In case of a fan with a skeleton rotor the following should be checked:
- whether the rotor is clean (clean with a vacuum cleaner and clean wet with a mild cleaning agent),
- whether the rotor turns easily,
- whether the rotor is balanced and does not run out,
- whether it has not moved in relation to the funnel (dimensions of appropriate slots retained),
- condition of vibration isolators,
- all mounting bolts (if necessary they should be tightened).
In case of an electric motor the following should be checked:
- correct fixing of all mechanical and power connections,
- the quality of wires and insulations
–
if there is no discoloring,
- insulation resistance of motor winding,
- whether there are no grease leaks,
- casing soiling (clean dry with a soft brush or blow through with compressed air).
The AHU as standard uses direct-drive ER and RLM
„
plug-fans
”
.
Types of applied fan and motor bearings are stated in the Quality control certificate.
The bearings are factory-filled with lithium grease which provides high mechanical stability, aging protection, good anti-corrosion
properties and operation range of 30
÷
+130
°
C.
Amount of the grease in standard operating conditions is designed for lifelong bearing operation.