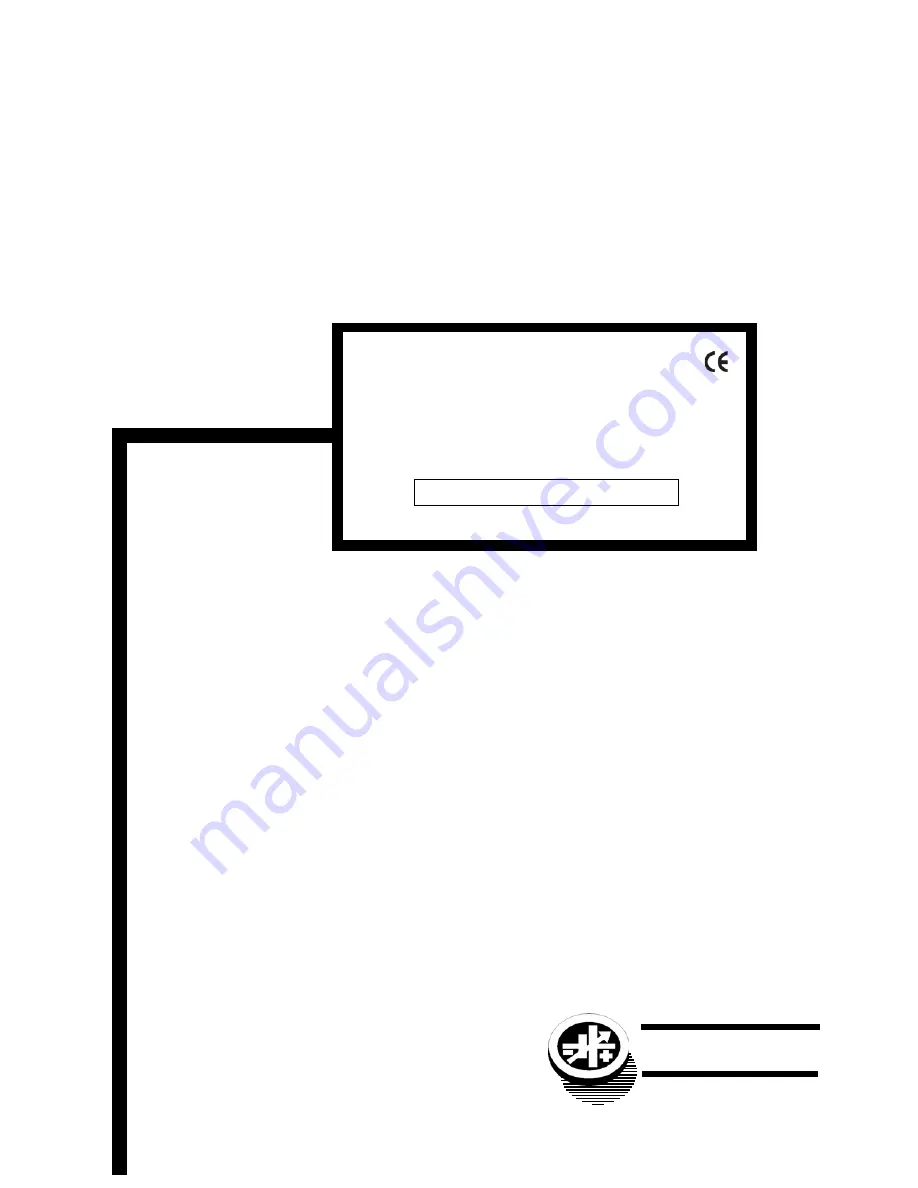
KEPCO
®
THE POWER SUPPLIER™
MODEL
OPERATOR’S MANUAL
ORDER NO.
KEPCO, INC.
z
131-38 SANFORD AVENUE
z
FLUSHING, NY. 11355 U.S.A.
z
TEL (718) 461-7000
z
FAX (718) 767-1102
email: [email protected]
z
World Wide Web: http://www.kepcopower.com
KEPCO INC.
An ISO 9001 Company.
BOP-MG 1KW
HIGH POWER BIPOLAR POWER SUPPLY
BOP-MG 1KW
POWER SUPPLY
©2012, KEPCO, INC
P/N 243-1027-r15b
IMPORTANT NOTES:
1)
This manual is valid for the following Firmware Versions:
FIRMWARE VERSION
NOTE.
2)
A Change Page may be included at the end of the manual. All applicable changes and
revision number changes are documented with reference to the equipment serial num-
bers. Before using this Instruction Manual, check your equipment firmware version num-
ber to identify your model. If in doubt, contact your nearest Kepco Representative, or the
Kepco Documentation Office in New York, (718) 461-7000, requesting the correct revision
for your particular model and firmware version number.
3)
The contents of this manual are protected by copyright. Reproduction of any part can be
made only with the specific written permission of Kepco, Inc.
Data subject to change without notice.
3.05 and higher
Summary of Contents for BOP-MG
Page 2: ......
Page 10: ......
Page 20: ...x BOP 1K 031912 FIGURE 1 1 HIGH POWER BOP SERIES POWER SUPPLY...
Page 37: ...BOP HIPWR 031912 1 17 FIGURE 1 3 BOP OUTPUT CHARACTERISTICS...
Page 53: ...BOP HIPWR 031912 2 15 FIGURE 2 4 PARALLEL CONFIGURATION LOCAL SENSING TYPICAL...
Page 54: ...2 16 BOP HIPWR 031912 FIGURE 2 5 PARALLEL CONFIGURATION REMOTE SENSING TYPICAL...
Page 64: ......
Page 132: ......
Page 192: ......