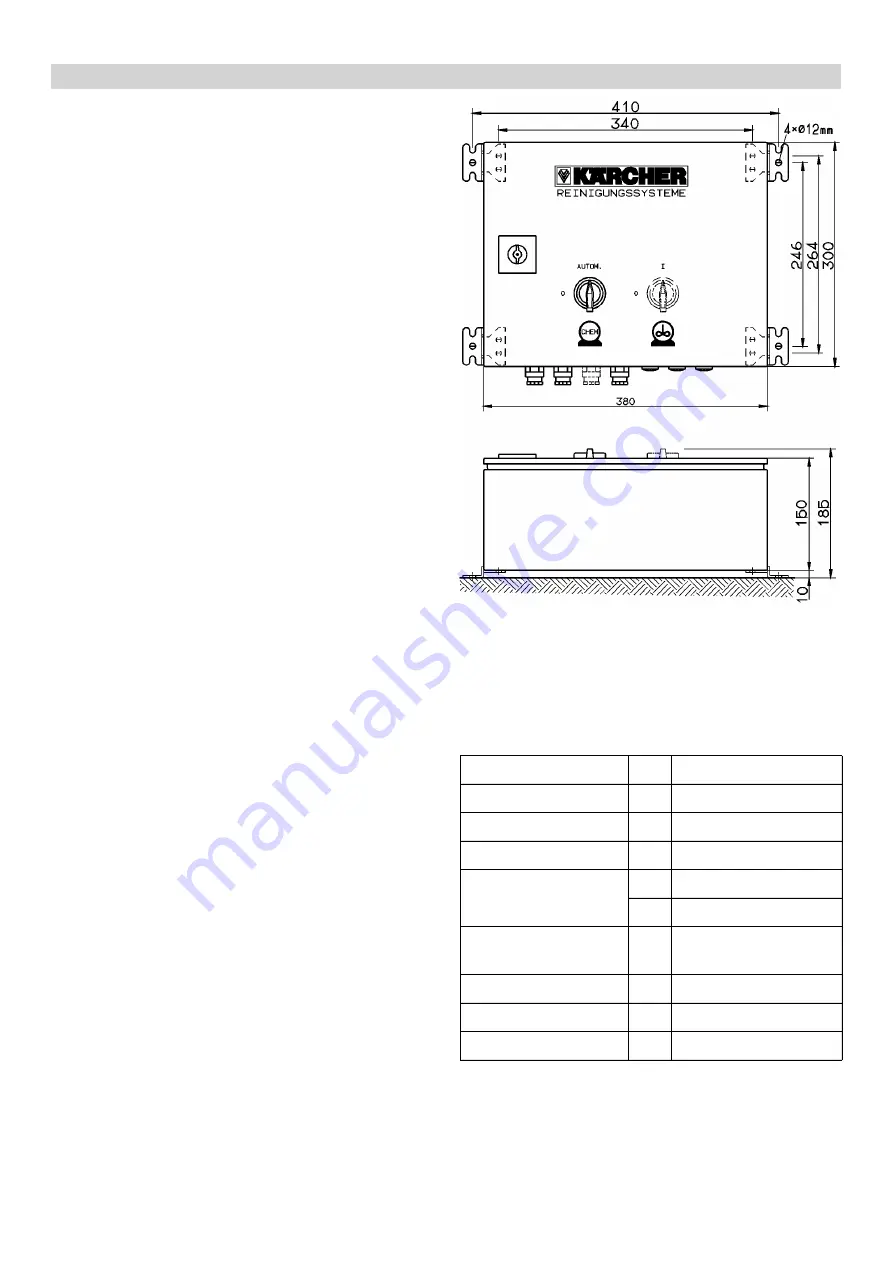
Deutsch
5.962-786.0 Rev. 05 (06/13)
65
Detergent supply unit for central supply of cleaning
systems with any number of access points.
The dosing centre is mostly set up operational and
consists of a PE container for the stockage of the de-
tergent, the pump unit, the mixing unit and the switch
cabinet for wall installation. The connecting hose with
hose stem as well as the fastening material is includ-
ed in the scope of delivery.
For each extraction point the suitable injector and the
ball valve are additionally required. Before each in-
jector and after each PE detergent tank these ball
valves must be installed.
The dosing centre will be taken into operation togeth-
er with the high pressure supply. It is designed to sup-
ply several access points simultaneously. In the
partial load area, the volume that has not been ex-
tracted will be routed back to the storage container
via a dosing valve.
The pump unit is designed as a glandless diaphragm
dosing pump with a separating chamber and manual
adjustment. It is driven by an electric motor and a
crank drive running in an oil bath.
Diaphragm casing made of PE RCH 500, diaphragm
PTFE coated, valve made of PVC with ceramic balls,
hypalon seal and connecting parts made of PVC en-
sure a high resistance over a wide pH range.
The connection between the supply unit and the ex-
traction point is ensured by means of an injector. This
ensures the addition of the concentrated detergent
directly at the extraction point. If two different deter-
gent are to be used for cleaning, the addition of the
detergents is to be performed via a complete dosing
unit, double (order no. 2.641-702.0). If only one de-
tergent is required, the standard injector for 1 deter-
gent can be used (order no. 3.637-001.0).
Note:
An injector must be installed at every extraction point
at which work is performed with a detergent. See
Chapter 7.6.4 for detailed information concerning the
injectors used.
Switch cabinet dosing centre
The control is designed as a contactor control; the
motor is monitored by a motor protection relay with a
pre-fuse. The switch cabinet is set up as per the VDE
guidelines and wired onto series terminals.
Technical data:
7.5
Accessories for central detergent supply
7.5.1
Supply unit of dosing centre
Pump capacity
l/h
208
Pressure
bar
max. 10 bar
Container capacity
l
2
00
Mixing unit
Hand mixer
Electrical connection V
3x400
Hz
50
Dimensions
mm Diameter
860x1750
Weight
kg
80
Power
kW
0,37
Order No.
3.910-005.0