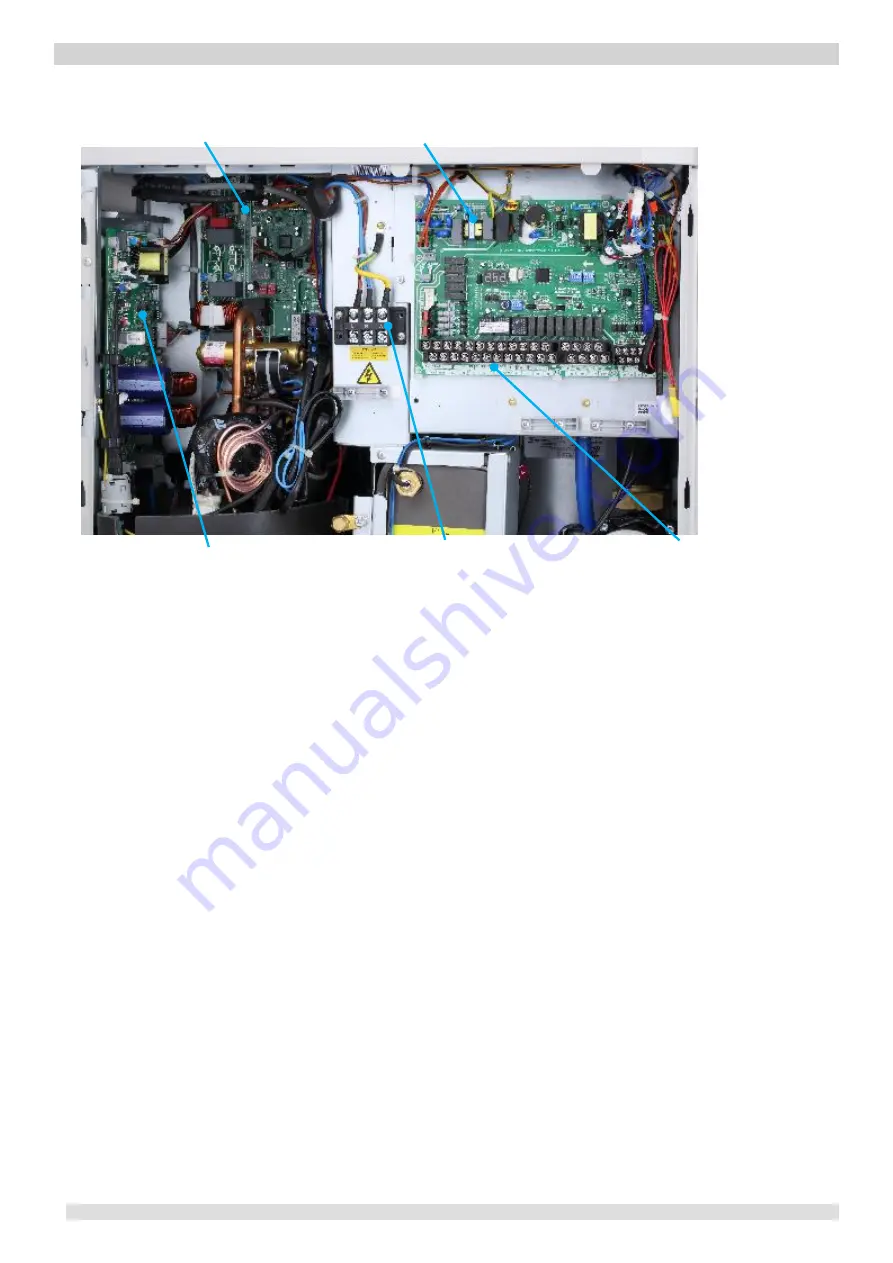
M thermal Mono
32
200208
Midea
M t
her
ma
l Mo
no
Se
rvice M
an
ual
1
Outdoor Unit Electric Control Box Layout
KHC-06RY1
Figure 4-1.1: Electric control box front view
Main PCB for refrigerant system
Main PCB for hydronic system
Main PCB for refrigerant system
Inverter module
terminal blocks
Midea CAC Confidential
M thermal Mono
202008
33
KHC-08RY1
/
KHC-10RY1
Figure 4-1.2: Electric control box front view
Main PCB for refrigerant system
Main PCB fort hydronic system
Inverter module
Outdoor unit power supply terminals
Communication terminal blocks
Midea CAC Confidential
Mono
Summary of Contents for 06RY1
Page 1: ...SERVICEMANUAL MONO TYPE HEAT PUMP R32...
Page 2: ...Mono...
Page 4: ...M thermal Mono 2 202008 Midea M thermal Mono Service Manual Midea CAC Confidential Mono...
Page 16: ...M thermal Mono 14 202008 Midea M thermal Mono Service Manual Midea CAC Confidential Mono...
Page 32: ...M thermal Mono 30 202008 Midea M thermal Mono Service Manual Midea CAC Confidential Mono...
Page 51: ...M thermal Mono 202008 51 Midea CAC Confidential Mono...
Page 113: ...Mono...
Page 114: ...kaisai com...