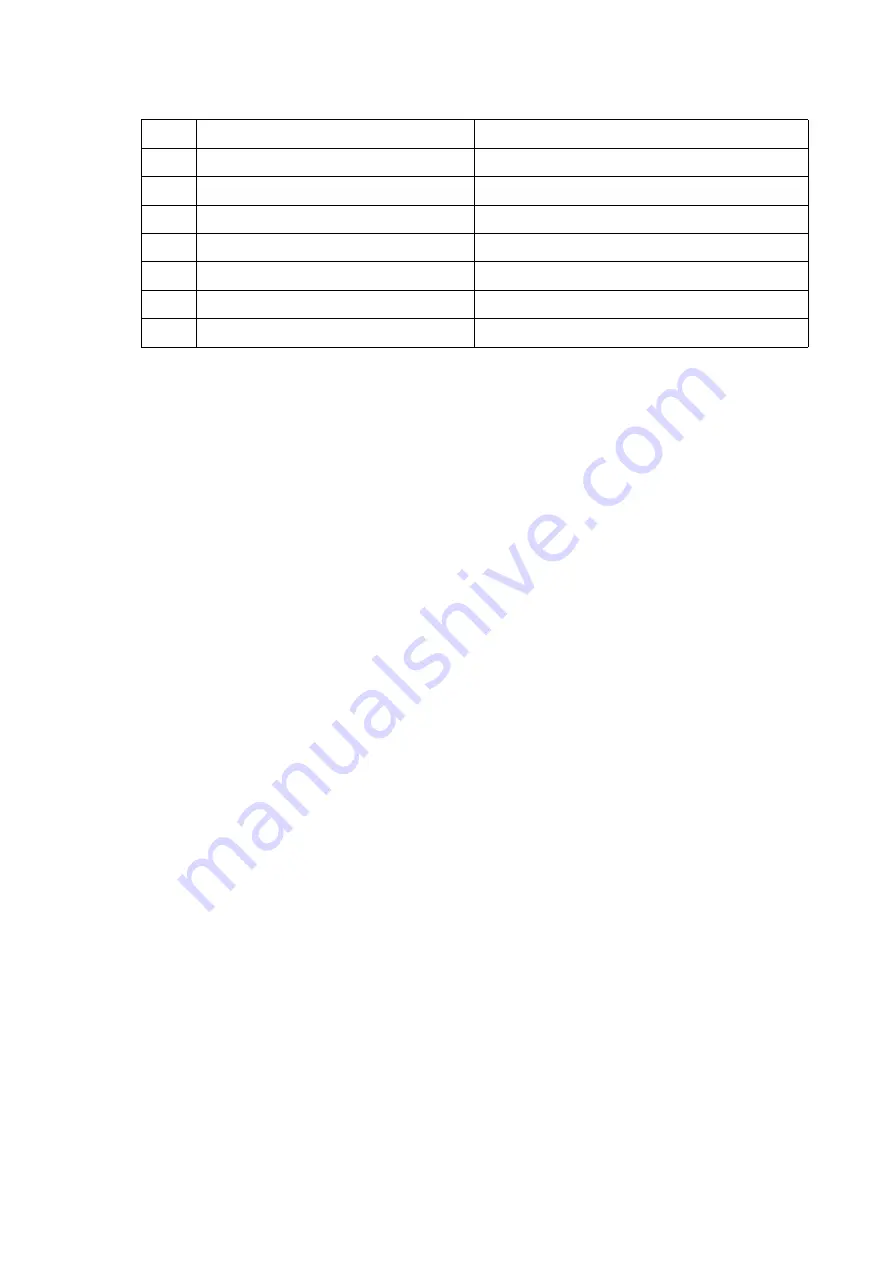
11
02
.1
6
EN
4.1.1 Battery nominal data
1.
Product
Traction battery
2.
Nominal voltage
2.0 V x number of cells
3.
Rated capacity C5
See data plate
4.
Discharge current
C5/5h
5.
Nominal electrolyte density
1
1. Reached within the first 10 cycles.
1.29 kg/l
6.
Nominal temperature
2
2. Higher temperatures shorten the useful life, lower temperatures reduce the
available capacity.
30 °C
7.
System rated electrolyte level
up to "Max" electrolyte level marking
Limit temperature
3
3. Not permissible as operating temperature.
55 °C
Summary of Contents for ETX 513
Page 1: ...ETX 513 ETX 515 03 11 Operating instructions 51190312 04 19 en GB ETX 513 ETX 515...
Page 2: ...2...
Page 4: ...4 04 19 en GB...
Page 12: ...0506 GB 2 0506 GB 2...
Page 34: ...4 2 2 Dimensions of ETX 513 T F ETX 513 T F with telescopic table z 32 04 19 en GB...
Page 36: ...z 34 04 19 en GB...
Page 54: ...52 04 19 en GB...
Page 96: ...94 04 19 en GB...
Page 152: ...4 7 Emergency Disconnect 9 150 04 19 en GB...
Page 360: ...358 04 19 en GB...
Page 384: ...02 16 EN 6...
Page 386: ...02 16 EN 8 14 Safety instructions and warning information...
Page 408: ......