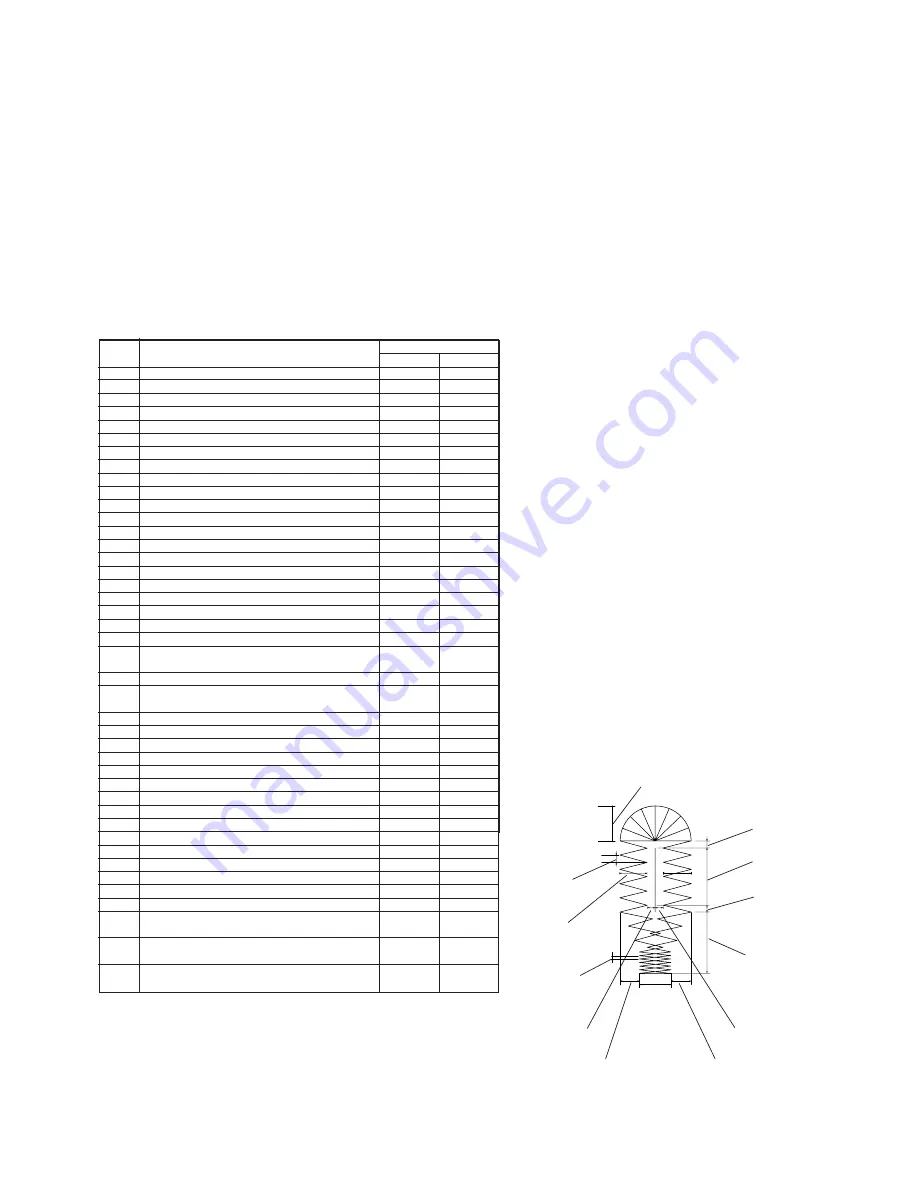
−
58
−
Data No. 11 :
Radial round type shape length
☆
Data No. 4 :
Stitch width
Data No. 8 :
Pitch at parallel
section
Data No. 9 :
Pitch at bar-
tacking section
☆
Data No. 15 :
Bar-tacking width,
left compensation
*
Data No. 3 :
Knife groove
width, left
☆
Data No. 14 :
B a r - t a c k i n g w i d t h ,
right compensation
Data No. 6 :
1st clearance
Data No. 1 :
Cloth cutting
length
Data No. 7 :
2nd clearance
*
Data No. 2 :
K n i f e g r o o v e
width, right
☆
Data No. 5 :
2nd bar-tacking
length
(3) Making the radial taper bar shape
It is convenient to perform the fine adjustment of the data after inputting data and making stitches referring to the
example of setting below. Main data determining the shape of the radial taper bar section are those with
☆
mark.
Caution when making the shape
Some data with
☆
mark or * mark will cause “Er 18” and “Er 19”.
1. It is necessary to set the length of data No. 4 “2nd bar-tacking length” two times or more than data No. 14
“Compensation of bar-tacking width, right” or data No. 15 “Compensation of bar-tacking width, left”. (Er 19)
2. Width A of of the taper bar section cannot be made less than data No. 4, Stitch width, left.
A = No. 4, Stitch width x2 “+” No. 2, Knife groove width, right “+” No. 3, Knife groove width, left “–” No. 14,
Compensation of bar-tacking width, right “–” No. 15, Compensation of bar-tacking width, left
Accordingly, the error occurs in accordance with the set value of No. 14, Compensation of bar-tacking width,
right or No. 15, Compensation of bar-tacking width, left. (Er 19)
No
Item
Pattern
For shirt
For knit
1
Cloth cutting length
12.70
19.10
2
Knife groove width, right
0.10
0.10
3
Knife groove width, left
0.10
0.10
4
Stitch width left
1.70
2.40
5
2nd bar-tacking length
3.0
4.0
6
1st clearance
1.50
1.50
7
2nd clearance
1.30
1.30
8
Pitch at parallel section
0.35
0.5
9
Pitch at bar-tacking section
0.30
0.30
10
Shape
5
5
11
Radial round type shape length
1.60
2.70
12
Number of stitches of radial shape
2
2
13
Reinforcement sewing (off/number of times)
0
2
14
Bar-tacking width, right compensation
-0.80
-1.20
15
Bar-tacking width, left compensation
-0.80
-1.20
16
Knife motion without/with
1
1
17
Left parallel section tension
190
175
18
Right parallel section tension
190
175
19
1st bar-tacking section tension
190
175
20
2nd bar-tacking section tension
190
175
21
1/2 stitching
1
2
22
When double stitching is performed
0
0
< X selection
23
Tie stitching width
0.50
0.50
24
Number of stitches of tie stitching
4
4
at sewing end
25
1st bar-tacking length
1.00
1.00
26
Number of stitches at the start of sewing
2
2
27
Pitch at the start of sewing
0.00
0.00
28
Stitch width right
1.70
2.40
29
Maximum speed limitation
30
Storing location
31
1st bar-tacking at the start ACT timing adjustment
0
0
32
Stitch width, right at the start ACT timing adjustment
0
0
33
2nd bar-tacking at the start ACT timing adjustment
0
0
34
Bar-tacking width (width of basting for sewing together)
3.6
5.00
35
Function of basting for sewing together Not provided/provided
0
0
36
Function of basting of bar-tacking Not provided/pitch
0
0
37
Radius of eyelet hole
0.7
0.7
38
Length of bottom of eyelet hole
2
2
39
Number of stitches of eyelet shape
3
3
60
Compensation of overedging width of 1st cycle when
0
0
double stitching is performed.
61
Left parallel section tension at 1st cycle when
190
175
double stitching is performed.
62
Right parallel section tension at 1st cycle when
190
175
double stitching is performed.
Be sure to
select 5.
Be sure to set
“–” value.
*
*
☆
☆
☆
☆
☆
*
*
Reference : Example of setting
A
Summary of Contents for LBH-1700
Page 1: ...R ENGINEER S MANUAL 29339504 No 04 Electronic Buttonholing Machine LBH 1700 Series ...
Page 55: ... 51 MEMO ...
Page 124: ... 120 ...