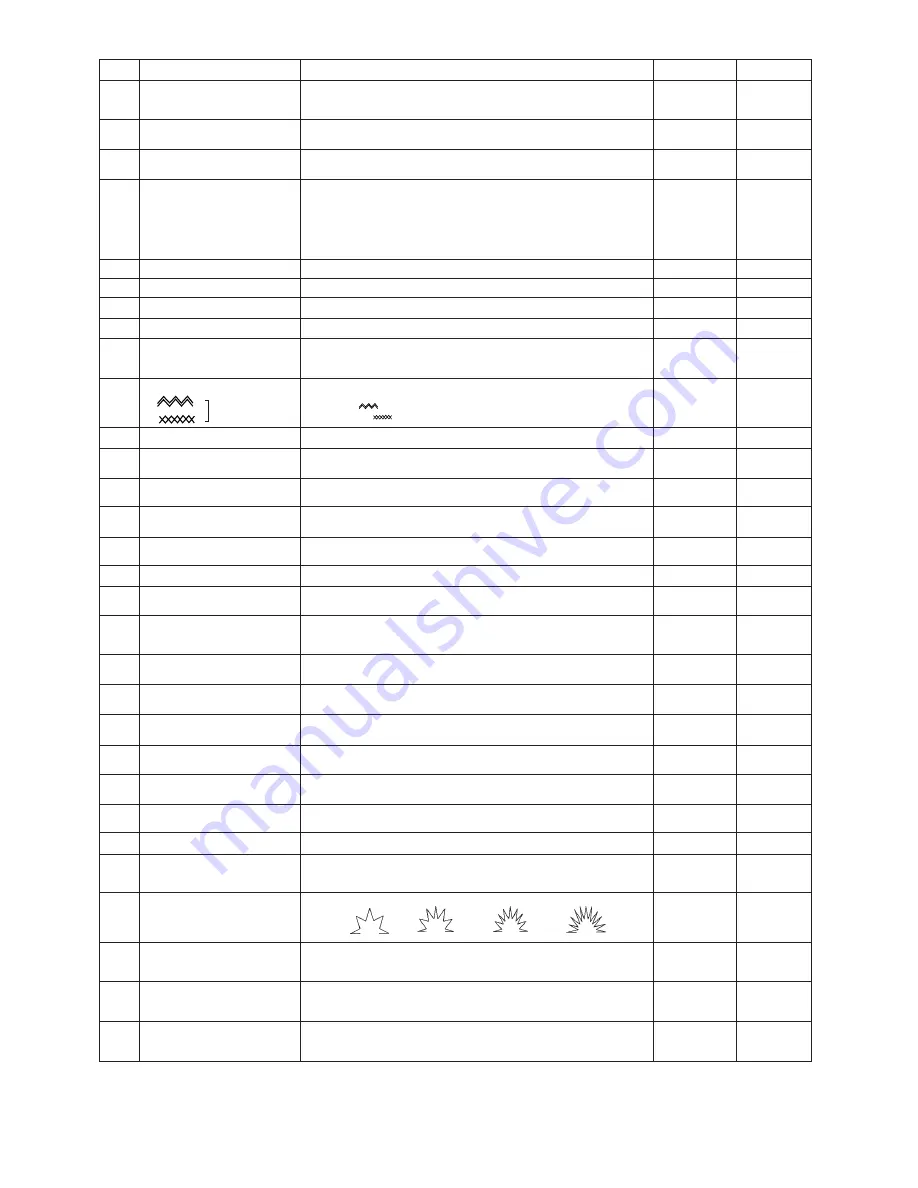
−
55
−
No.
13
14
15
16
17
18
19
20
21
22
23
24
25
26
27
28
29
30
31
32
33
34
35
36
37
38
39
60
61
62
Description
This item performs straight sewing for reinforcement in overedging width.
0 : Without function
1 to 9 : Number of times setting
This item compensates the position of right stitch base line of bar-tacking section.
This item compensates the position of the left side zigzag width of bar-tacking section.
This item selects the motion of cloth cutting knife.
0 : Without motion
1 : Motion at 2nd cycle only when double stitching is performed. (Normal motion)
2 : Motion at 1st cycle only when double stitching is performed.
3 : Motion both at 1st and 2nd cycles when double stitching is performed.
(Setting of 2 or 3 is effective in case of the shape of square type, radial square type or
round type.)
This item sets the left parallel section tension.
This item sets the right parallel section tension.
This item sets the tension at 1st bar-tacking section.
This item sets the tension at 2nd bar-tacking section.
This item selects single/double stitching.
1 : Single stitching
2 : Double stitching
This item selects double stitching when performing double stitching.
This item selects whether 1st cycle and 2nd cycle are overlapped.
0 : Overlap (
)
1 : Not overlap (
)
This item sets the tie stitch width at sewing end.
This item sets the number of stitches of tie stitching at sewing end.
This item sets length of 1st bar-tacking section
Square type : Setting of 1st bar-tacking.
This item sets the number of stitches at the start of sewing.
This item sets the sewing pitch at the start of sewing.
(Two stitches of the number of stitches of the data No.26)
This item sets stitch width of the right parallel section.
This item sets the max. speed limitation. (Depending on the speed setting value of
memory switch No. 98)
This item sets the storing location where data is copied.
1 to 89 : capable of storing
90 to 99 : Not capable
This item adjusts timing of needle thread tension at the start of 1st bar-tacking.
This item adjusts timing of needle thread tension at the start of stitch width, right.
This item adjusts timing of needle thread tension at the start of 2nd bar-tacking.
This item sets the width of shape 7 : Bar-tacking.
This item sets width when the function of basting for sewing together is provided.
Normally basting for sewing together is performed before sewing.
Basting of zigzag is performed at the time of bar-tacking section of the square type.
This item sets radius of eyelet hole section.
This item selects length of bottom (tail section) of eyelet hole.
0 to 3 : Short to long
If the length is short, angle from parallel section to eyelet hole becomes sharp.
This item sets number of stitches of eyelet shape section.
This item narrows width of 1sr cycle in terms of data No. 4 : overedging width setting.
This setting is effective in case of the shape of square type, radial square type or
round type.
This item sets the left parallel section tension at 1st cycle when double stitching is
performed. This setting is effective in case of the shape of square type, radial square
type or round type.
This item sets the right parallel section tension at 1st cycle when double stitching is
performed. This setting is effective in case of the shape of square type, radial square
type or round type.or round type.
Setting range
0 to 9
-2.0 to 1.0
-2.0 to 1.0
0/1/2/3
0 to 255
0 to 255
0 to 255
0 to 255
1/2
0/1
0 to 1.5
0/2/4/6
0.2 to 5.0
0/2/4/6/8
0 to 0.7
0.1 to 2.5
400 to max
1 to 89
-5 to 5
-5 to 5
-5 to 5
1 to 6.
0/1
0 to 1
0.00 to 2.90
0 to 3
1 to 4
0.00 to 1.50
0 to 255
0 to 255
Unit
1
0.05 mm
0.05 mm
–
1
1
1
1
–
–
0.1 mm
–
0.1 mm
–
0.05 mm
0.05 mm
100 rpm
1
1 N
1 N
1 N
0.1 mm
–
0.1 mm
0.10 mm
1
1N
0.05 mm
1
1
Setting item
Reinforcement sewing
(off/number of times)
Compensation of bar-tacking width,
right
Compensation of bar-tacking width,
left
Knife motion Without/with/
1st cycle/1st and 2nd cycles
Left parallel section tension
Right parallel section tension
Tension at 1st bar-tacking section
Tension at 2nd bar-tacking section
1/2 stitching
When double stitching is performed.
Tie stitching width
Number of stitches of tie stitching at
sewing end
1st bar-tacking length
Number of stitches at the start of
sewing
Pitch at the start of sewing
Stitch width right
Maximum speed limitation
Storing location
1st bar-tacking at the start
ACT timing adjustment
Stitch width, right at the start
ACT timing adjustment
2nd bar-tacking at the start
ACT timing adjustment
Bar-tacking width (width of basting
for sewing together)
Function of basting for sewing
together Not provided/provided
Function of basting of bar-tacking Not
provided/pitch
Radius of eyelet hole
Length of bottom of eyelet hole
Number of stitches of eyelet shape
Compensation of overedging width
of 1st cycle when double stitching is
performed.
Left parallel section tension at 1st
cycle when double stitching is
performed.
Right parallel section tension at 1st
cycle when double stitching is
performed.
selection
(The values in the list are the data of ROMRev : 005A. There is a case where they are different from the actual data.)
* 1 ROMRev : Available from 004C
* 2 ROMRev : Available from 004F and 005
* 3 ROMRev : Individual setting of left/right stitch width is possible with 004C, D and E only. Overedging width up to 3 mm is available from 004F and 005
* 4 ROMRev : Available from 005A
* 5 ROMRev : Radial straight bar-tacking is added with 004C only.
ROMRev : Semilunar type and bar-tacking are added with 004F and 005 only.
ROMRev : 4 kinds of eyelet shapes are added with 005A only.
1 2 3 4
*
3
*
1
*
1
*
1
*
2
*
2
*
2
*
4
*
4
*
4
*
4
*
4
*
4
*
4
Summary of Contents for LBH-1700
Page 1: ...R ENGINEER S MANUAL 29339504 No 04 Electronic Buttonholing Machine LBH 1700 Series ...
Page 55: ... 51 MEMO ...
Page 124: ... 120 ...