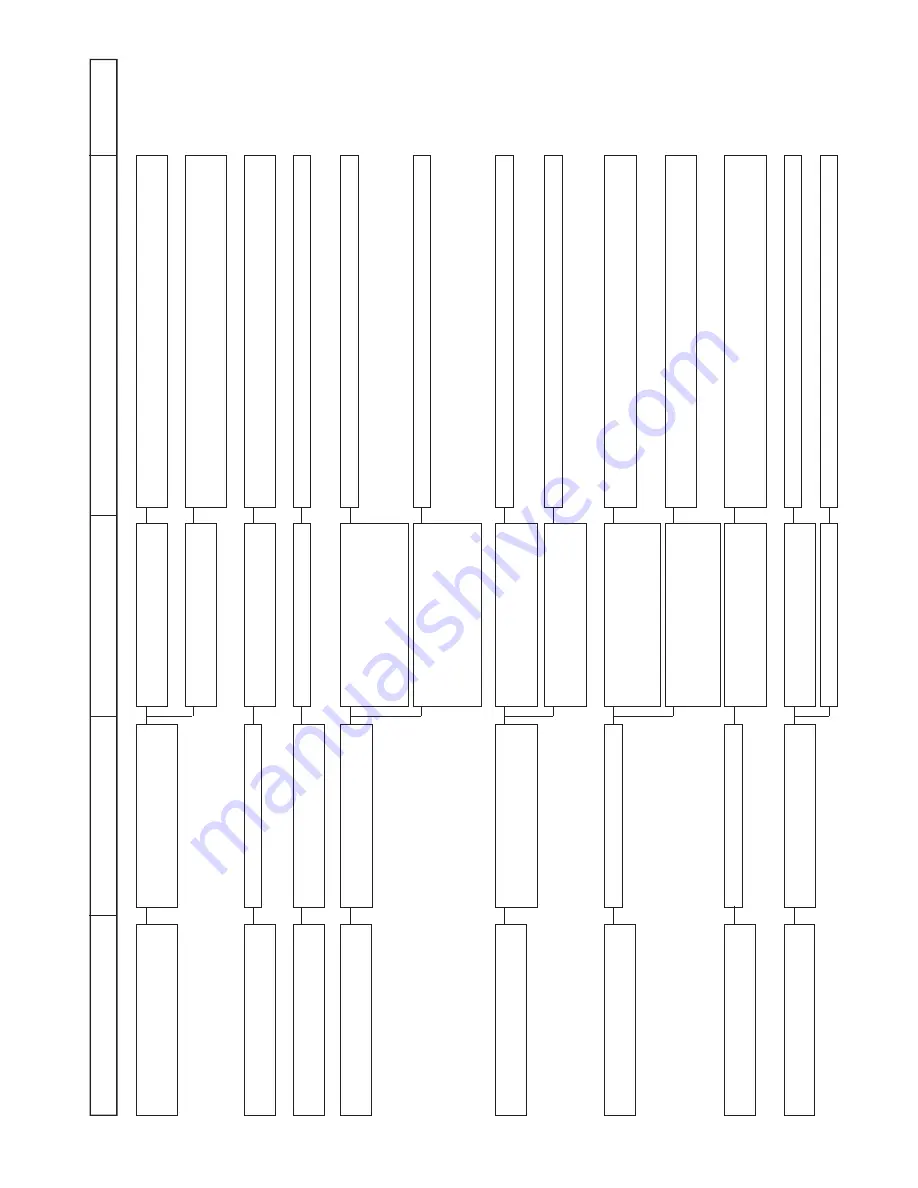
−
100
−
Trouble
Cause (1)
Cause (2)
Checking order and adjusting procedure
Page
15.
Error No. 15
Knife size, cloth cutting length
error
16.
Error No. 16
Knife drive timing error
17.
Error No. 17
Cycle sewing data ineffective error
18.
Error No. 18
Position of the start of sewing error
19.
Error No. 19
Bar-tacking compensation error
20. Error No. 30
Eyelet width error
21. Error No. 21
Eyelet length error
22. Error No. 40
S. State error
1.
Input data is wrong.
(At the time of operation of plural
times)
1.
Knife drive timing is not obtained.
1.
Pattern selected for cycle sewing
is ineffective.
1
.
Position of the start of sewing is
wrong.
1
.
Bar-tacking width + bar-tacking
compensation value is larger than
5 mm.
1. Input data is wrong.
1. Input data is wrong.
1
.
Signal from SDC circuit board is
wrong.
1
.
Knife size is larger than cloth
cutting length.
2.
When knife bar comes in contact
with work clamp.
1
.
2nd bar-tacking 2nd
clearance is shorter than 2 mm.
1.
Input data is wrong.
1
.
Position of the start of sewing
calculated from the number of
stitches at the start of sewing and
pitch is longer than the bar-tacking
length.
2
.
Left/right bar-tacking width
compensation values X 2 +
position of the start of sewing is
larger than bar-tacking length - 0.1
mm at the time of flow bar-tacking.
1
.
Overedging width + right knife
right compensation
exceeds 1/2 of the size of presser.
2
.
Overedging width + left knife
left compensation
exceeds 1/2 of the size of presser.
1. When overedging width + radius
of eyelet hole + knife groove width,
left exceed 1/2 of the width of
presser size.
2. When overedging width + radius
of eyelet hole + knife groove width,
right exceed 1/2 of the width of
presser size.
1. When the bottom (tail section) of
eyelet hole overlaps 2nd bar-
tacking section.
1
.
Connection is defective or cable
is defective.
2.
SDC circuit board is defective.
Change the data so that the cloth cutting length is larger than the knife
size. Or, make the knife size less than the cloth cutting length.
Knife bar may come in contact with work clamp when using a long
presser with a small knife size. In this case, replace the knife size with
a larger one.
Change the data so that 2nd bar-tacking 2nd clearance
becomes more than 2 mm.
Change the data.
Change the data.
Change the data.
Change the data.
Change the data.
Change overedging width, radius of eyelet hole and knife groove width
so as to adapt to 1/2 of the width of presser size.
Change overedging width, radius of eyelet hole and knife groove width,
right so as to adapt to 1/2 of the width of presser size.
Change length of the bottom of eyelet hole and the cloth cutting length
so that the botom of eyelet hole does not overlap 2nd bar-tacking
section.
Check the connection of CN12 and CN40.
Replace the SDC circuit board.
Summary of Contents for LBH-1700
Page 1: ...R ENGINEER S MANUAL 29339504 No 04 Electronic Buttonholing Machine LBH 1700 Series ...
Page 55: ... 51 MEMO ...
Page 124: ... 120 ...