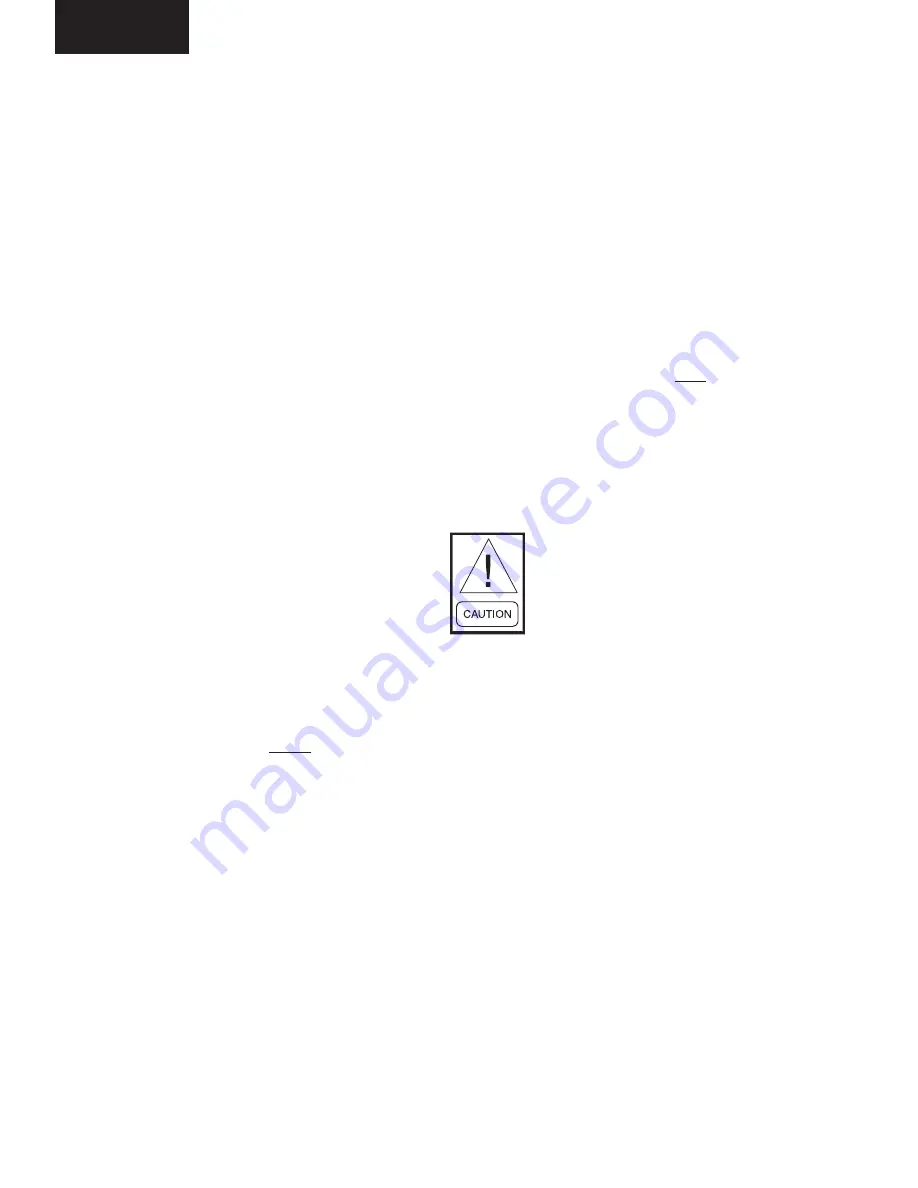
JOHNSON CONTROLS
68
FORM 150.62-NM6 (103)
The subcooling temperature of each system can be
calculated by recording the temperature of the liquid
line at the outlet of the condenser and subtracting it from
the liquid line saturation temperature at the liquid stop
valve (liquid line saturation temp. is converted from a
temperature/pressure chart).
Example:
Liquid line pressure =
102°F
202 PSIG converted to - 87°F
minus liquid line temp.
Subcooling =
15°F
The subcooling should be adjusted to 15°F at design
conditions.
1. Record the liquid line pressure and its corre-
sponding temperature, liquid line temperature
and subcooling below:
SYS 1 SYS 2
Liq Line Press = _______ _______ PSIG
Saturated Temp = _______ _______ °F
Liq Line Temp = _______ _______ °F
Subcooling = _______ _______ °F
After the subcooling is verified, the suction superheat
should be checked. The superheat should be checked
only after steady state operation of the chiller has been
established, the leaving water temperature has been pulled
down to the required leaving water temperature, and the
unit is running in a fully loaded condition. Correct superheat
setting for a system is 10°F - 15°F (5.56°C - 8.33°C) 18"
(46 cm) from the cooler.
Superheat should typically be set for no less than
10°F with only a single compressor running on a
circuit.
The superheat is calculated as the difference
between the actual temperature of the returned refrig-
erant gas in the suction line entering the compressor and
the temperature corresponding to the suction pressure
as shown in a standard pressure/temperature chart.
Example:
Suction Temp =
46°F
minus Suction Press
60 PSIG converted to Temp - 34°F
Superheat =
12°F
When adjusting the expansion valve (TxV only), the
adjusting screw should be turned not more than one
turn at a time, allowing sufficient time (approximately 15
minutes) between adjustments for the system and the
thermal expansion valve to respond and stabilize.
The EEV is nonadjustable. Superheat
setpoint is programmable from the
keypad.
Assure that superheat is set at a minimum of 10°F (5.56°C)
with a single compressor running on each circuit.
2. Record the suction temperature, suction pressure,
suction saturation temperature, and superheat of
each system below:
SYS 1
SYS 2
Suction temp = _______ _______ °F
Suction Pressure = _______ _______ PSIG
Saturation Temp = _______ _______ °F
Superheat = _______ _______ °F
LEAK CHECKING
1. Leak check compressors, fittings, and piping to
ensure no leaks.
If the unit is functioning satisfactorily during the initial
operating period, no safeties trip and the compressors
cycle to control water temperature to setpoint, the chiller
is ready to be placed into operation.
Installation
3. Allow the compressor to run a short time, being
ready to stop it immediately if any unusual noise
or adverse conditions develop.
4. Check the system operating parameters. Do this
by selecting various displays such as pressures
and temperatures and comparing these readings
to pressures and temperatures taken with man-
ifold gauges and temperature sensors.
5. With an ammeter, verify that each phase of the
condenser fans and compressors are within the
RLA as listed under Electrical Data.
CHECKING SUPERHEAT AND SUbCOOLING
The subcooling and superheat should always be
checked when charging the system with refrigerant.
When the refrigerant charge is correct, there will be no
vapor in the liquid sight glass with the system operating
under full load conditions, and there will be 15°F (8.34°C)
subcooled liquid leaving the condenser.
An overcharged system should be guarded against.
The temperature of the liquid refrigerant out of the con-
denser should be no more than 18°F (10°C) subcooled
at design conditions.
Summary of Contents for York YCAL0014E Series
Page 111: ...JOHNSON CONTROLS 111 FORM 150 62 nm6 103 2 This page intentionally left blank...
Page 133: ...JOHNSON CONTROLS 133 FORM 150 62 nm6 103 4 LD08851...
Page 135: ...JOHNSON CONTROLS 135 FORM 150 62 nm6 103 4 This page intentionally left blank...
Page 137: ...JOHNSON CONTROLS 137 FORM 150 62 nm6 103 LD08855 4...
Page 139: ...JOHNSON CONTROLS 139 FORM 150 62 nm6 103 4 This page intentionally left blank...
Page 141: ...JOHNSON CONTROLS 141 FORM 150 62 nm6 103 LD08858 4...
Page 143: ...JOHNSON CONTROLS 143 FORM 150 62 nm6 103 4 This page intentionally left blank...
Page 145: ...JOHNSON CONTROLS 145 FORM 150 62 nm6 103 LD08862 4...
Page 147: ...JOHNSON CONTROLS 147 FORM 150 62 nm6 103 4 This page intentionally left blank...
Page 149: ...JOHNSON CONTROLS 149 FORM 150 62 nm6 103 LD08865...
Page 151: ...JOHNSON CONTROLS 151 FORM 150 62 nm6 103 LD08867...
Page 153: ...JOHNSON CONTROLS 153 FORM 150 62 nm6 103 LD08869...
Page 155: ...JOHNSON CONTROLS 155 FORM 150 62 nm6 103 4 This page intentionally left blank...
Page 157: ...JOHNSON CONTROLS 157 FORM 150 62 nm6 103 LD08872...
Page 159: ...JOHNSON CONTROLS 159 FORM 150 62 nm6 103 4 LD08877...
Page 161: ...JOHNSON CONTROLS 161 FORM 150 62 nm6 103 LD08874...
Page 163: ...JOHNSON CONTROLS 163 FORM 150 62 nm6 103 This page intentionally left blank...
Page 165: ...JOHNSON CONTROLS 165 FORM 150 62 nm6 103 4 LD08830...
Page 167: ...JOHNSON CONTROLS 167 FORM 150 62 nm6 103 4 LD08833...
Page 169: ...JOHNSON CONTROLS 169 FORM 150 62 nm6 103 4 LD08835...
Page 171: ...JOHNSON CONTROLS 171 FORM 150 62 nm6 103 4 This page intentionally left blank...
Page 173: ...JOHNSON CONTROLS 173 FORM 150 62 nm6 103 4 LD08837...
Page 175: ...JOHNSON CONTROLS 175 FORM 150 62 nm6 103 4 LD08840...
Page 177: ...JOHNSON CONTROLS 177 FORM 150 62 nm6 103 4 LD08842...
Page 179: ...JOHNSON CONTROLS 179 FORM 150 62 nm6 103 4 This page intentionally left blank...
Page 181: ...JOHNSON CONTROLS 181 FORM 150 62 nm6 103 4 LD08844...
Page 183: ...JOHNSON CONTROLS 183 FORM 150 62 nm6 103 4 LD08847...
Page 185: ...JOHNSON CONTROLS 185 FORM 150 62 nm6 103 4 LD08849...
Page 187: ...JOHNSON CONTROLS 187 FORM 150 62 nm6 103 4 This page intentionally left blank...