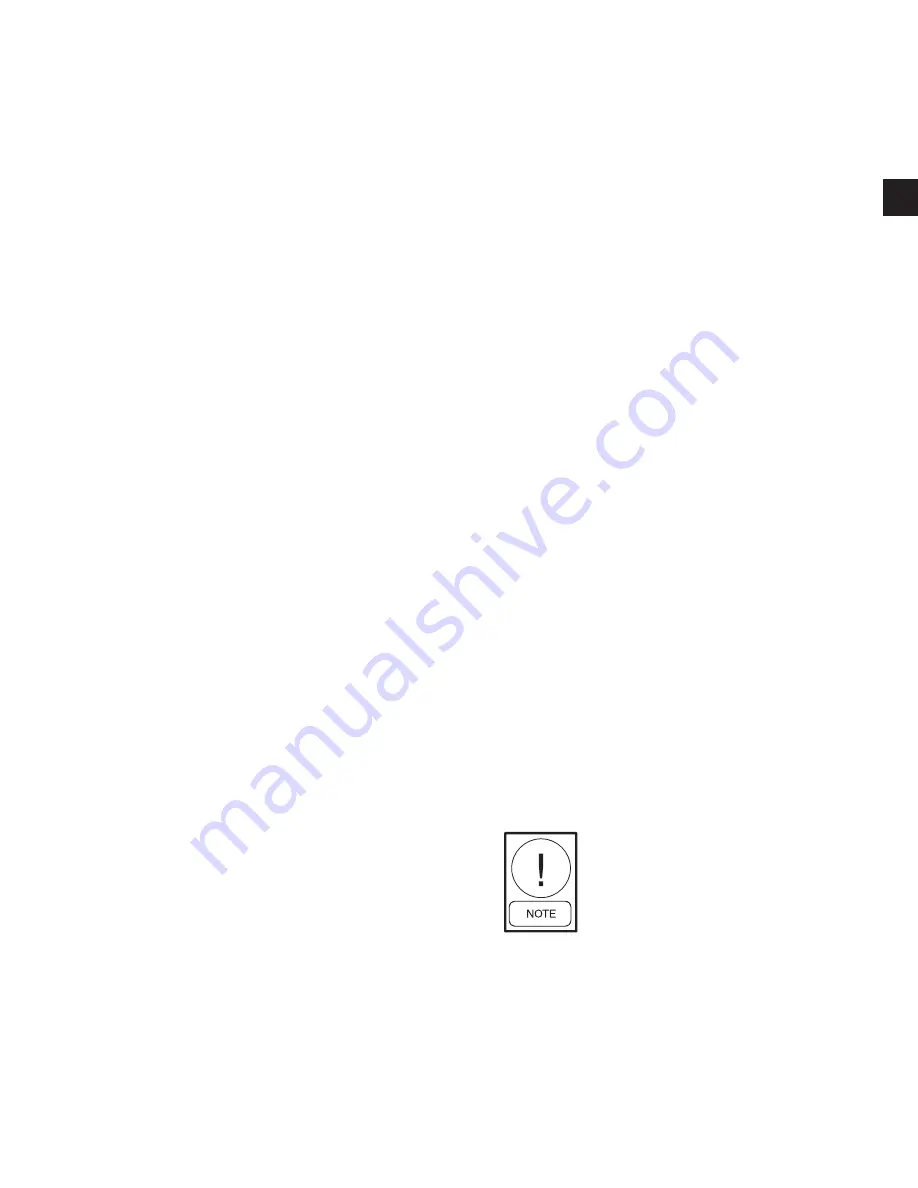
JOHNSON CONTROLS
11
FORM 150.62-NM6 (103)
FOUNDATION
The unit should be mounted on a flat and level foun
-
dation, floor, or rooftop capable of supporting the entire
operating weight of the equipment. See PHYSICAL
DATA for operating weight. If the unit is elevated beyond
the normal reach of service personnel, a suitable catwalk
must be capable of supporting service personnel, their
equipment, and the compressors.
GROUND LEvEL LOCATIONS
It is important that the units be installed on a substantial
base that will not settle. A one piece concrete slab with
footers extended below the frost line is highly recom-
mended. Additionally, the slab should not be tied to
the main building foundations as noise and vibration
may be transmitted. Mounting holes are provided in the
steel channel for bolting the unit to its foundation. (See
DIMENSIONS.)
For ground level installations, precautions should be
taken to protect the unit from tampering by or injury to
unauthorized persons. Screws and/or latches on access
panels will prevent casual tampering. However, further
safety precautions such as a fenced-in enclosure or
locking devices on the panels may be advisable.
ROOFTOP LOCATIONS
Choose a spot with adequate structural strength to safely
support the entire weight of the unit and service per-
sonnel. Care must be taken not to damage the roof.
Consult the building contractor or architect if the roof is
bonded. Roof installations should have wooden beams
(treated to reduce deterioration), cork, rubber, or vibra-
tion isolators under the base to minimize vibration.
NOISE SENSITIvE LOCATIONS
Efforts should be made to assure that the chiller is not
located next to occupied spaces or noise sensitive areas
where chiller noise level would be a problem. Chiller
noise is a result of compressor and fan operation. Con-
siderations should be made utilizing noise levels pub-
lished in the YORK Engineering Guide for the specific
chiller model. Sound blankets for the compressors and
low sound fans are available.
SPRING ISOLATORS (OPTIONAL)
When ordered, four (4) isolators will be furnished.
Identify the isolator, locate at the proper mounting point,
and adjust per instructions. See APPENDIx 1.
COMPRESSOR MOUNTING
The compressors are mounted on four (4) rubber iso-
lators. The mounting bolts should not be loosened or
adjusted at installation of the chiller.
REMOTE COOLER OPTION
For units using remote cooler option, refer to instructions
included with miscellaneous cooler parts kit.
The unit and remote cooler is shipped with a 6 lb. (2.7
kg) nitrogen holding charge. The nitrogen charge must
be removed, and system evacuated, and the refrigerant
charge must be weighed-in according to the operating
charge listed under PHYSICAL DATA. Additional charge
must also be added for the refrigerant lines.
CHILLED wATER PIPING
General –
When the unit has been located in its
final position, the unit water piping may be connected.
Normal installation precautions should be observed in
order to receive maximum operating efficiencies. Piping
should be kept free of all foreign matter. All chilled water
evaporator piping must comply in all respects with local
plumbing codes and ordinances.
Since elbows, tees and valves decrease pump capacity,
all piping should be kept as straight and as simple as
possible.
All piping must be supported independent
of the chiller.
Consideration should be given to
compressor access when laying out
water piping. Routing the water pip
ing too close to the unit could make
compressor servicing/replacement
difficult.
1
Summary of Contents for York YCAL0014E Series
Page 111: ...JOHNSON CONTROLS 111 FORM 150 62 nm6 103 2 This page intentionally left blank...
Page 133: ...JOHNSON CONTROLS 133 FORM 150 62 nm6 103 4 LD08851...
Page 135: ...JOHNSON CONTROLS 135 FORM 150 62 nm6 103 4 This page intentionally left blank...
Page 137: ...JOHNSON CONTROLS 137 FORM 150 62 nm6 103 LD08855 4...
Page 139: ...JOHNSON CONTROLS 139 FORM 150 62 nm6 103 4 This page intentionally left blank...
Page 141: ...JOHNSON CONTROLS 141 FORM 150 62 nm6 103 LD08858 4...
Page 143: ...JOHNSON CONTROLS 143 FORM 150 62 nm6 103 4 This page intentionally left blank...
Page 145: ...JOHNSON CONTROLS 145 FORM 150 62 nm6 103 LD08862 4...
Page 147: ...JOHNSON CONTROLS 147 FORM 150 62 nm6 103 4 This page intentionally left blank...
Page 149: ...JOHNSON CONTROLS 149 FORM 150 62 nm6 103 LD08865...
Page 151: ...JOHNSON CONTROLS 151 FORM 150 62 nm6 103 LD08867...
Page 153: ...JOHNSON CONTROLS 153 FORM 150 62 nm6 103 LD08869...
Page 155: ...JOHNSON CONTROLS 155 FORM 150 62 nm6 103 4 This page intentionally left blank...
Page 157: ...JOHNSON CONTROLS 157 FORM 150 62 nm6 103 LD08872...
Page 159: ...JOHNSON CONTROLS 159 FORM 150 62 nm6 103 4 LD08877...
Page 161: ...JOHNSON CONTROLS 161 FORM 150 62 nm6 103 LD08874...
Page 163: ...JOHNSON CONTROLS 163 FORM 150 62 nm6 103 This page intentionally left blank...
Page 165: ...JOHNSON CONTROLS 165 FORM 150 62 nm6 103 4 LD08830...
Page 167: ...JOHNSON CONTROLS 167 FORM 150 62 nm6 103 4 LD08833...
Page 169: ...JOHNSON CONTROLS 169 FORM 150 62 nm6 103 4 LD08835...
Page 171: ...JOHNSON CONTROLS 171 FORM 150 62 nm6 103 4 This page intentionally left blank...
Page 173: ...JOHNSON CONTROLS 173 FORM 150 62 nm6 103 4 LD08837...
Page 175: ...JOHNSON CONTROLS 175 FORM 150 62 nm6 103 4 LD08840...
Page 177: ...JOHNSON CONTROLS 177 FORM 150 62 nm6 103 4 LD08842...
Page 179: ...JOHNSON CONTROLS 179 FORM 150 62 nm6 103 4 This page intentionally left blank...
Page 181: ...JOHNSON CONTROLS 181 FORM 150 62 nm6 103 4 LD08844...
Page 183: ...JOHNSON CONTROLS 183 FORM 150 62 nm6 103 4 LD08847...
Page 185: ...JOHNSON CONTROLS 185 FORM 150 62 nm6 103 4 LD08849...
Page 187: ...JOHNSON CONTROLS 187 FORM 150 62 nm6 103 4 This page intentionally left blank...