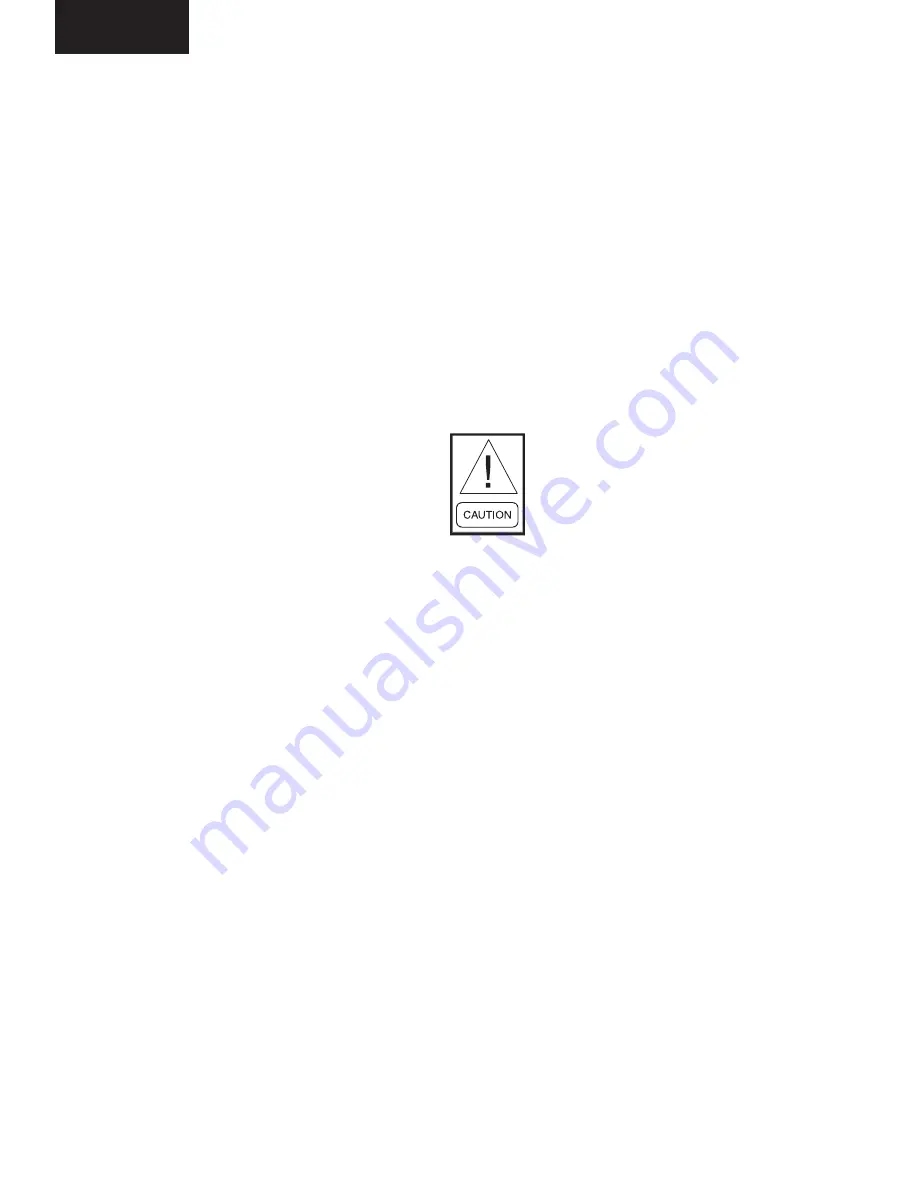
JOHNSON CONTROLS
12
FORM 150.62-NM6 (103)
Hand stop valves should be installed in all lines to fa-
cilitate servicing.
Piping to the inlet and outlet connections of the chiller
should include high-pressure rubber hose or piping
loops to ensure against transmission of water pump
vibration. The necessary components must be obtained
in the field.
Drain connections should be provided at all low points
to permit complete drainage of the cooler and system
water piping.
A small valve or valves should be installed at the highest
point or points in the chilled water piping to allow any
trapped air to be purged. Vent and drain connections
should be extended beyond the insulation to make them
accessible.
The piping to and from the cooler must be designed
to suit the individual installation. It is important that the
following considerations be observed:
1. The chilled liquid piping system should be laid out
so that the circulating pump discharges directly
into the cooler. The suction for this pump should
be taken from the piping system return line and not
the cooler. This piping scheme is recommended,
but is not mandatory.
2. The inlet and outlet cooler connection sizes are
3" (YCAL0014 - 0024), 4" (YCAL0030 - 0034), 6"
(YCAL0040 - 0080), or 8" (YCAL0090 - 0124) .
3. A strainer, preferably 40 mesh,
must
be installed
in the cooler inlet line just ahead of the cooler. This
is important to protect the cooler from entrance of
large particles which could cause damage to the
evaporator.
4. All chilled liquid piping should be thoroughly flushed
to free it from foreign material before the system
is placed into operation. Use care not to flush any
foreign material into or through the cooler.
5. As an aid to servicing, thermometers and pressure
gauges should be installed in the inlet and outlet
water lines.
6. The chilled water lines that are exposed to outdoor
ambients should be wrapped with supplemental
heater cable and insulated to protect against
freeze-up during low ambient periods, and to pre-
vent formation of condensation on lines in warm
humid locations.
7. A chilled water flow switch, (either by YORK or oth
-
ers) MUST be installed in the leaving water piping of
the cooler. There should be a straight horizontal run
of at least 5 diameters on each side of the switch.
Adjust the flow switch paddle to the size of the pipe
in which it is to be installed. (See manufacturer’s
instructions furnished with the switch.) The switch
is to be wired to terminals 13 - 14 of CTb1 located
in the control panel, as shown on the unit wiring
diagram.
wIRING
Liquid Chillers are shipped with all factory-mounted
controls wired for operation.
Field wiring
–
Power wiring must be provided through
a fused disconnect switch to the unit terminals (or op-
tional molded disconnect switch) in accordance with
N.E.C. or local code requirements. Minimum circuit
ampacity and maximum dual element fuse size are
given in the Tables 2 – 6.
A 120-1-60, 15 amp source must be supplied for the
control panel through a fused disconnect when a control
panel transformer (optional) is not provided. Refer to
Table 1 and Figures 2 - 6.
See Figures 2 - 6 and unit wiring diagrams for field and
power wiring connections, chilled water pump starter
contacts, alarm contacts, compressor run status con-
tacts, PWM input, and load limit input. Refer to section on
UNIT OPERATION for a detailed description of operation
concerning aforementioned contacts and inputs.
Installation
The Flow Switch MUST NOT be used
to start and stop the chiller (i.e. start
ing and stopping the chilled water
pump). It is intended only as a safety
switch.
Summary of Contents for York YCAL0014E Series
Page 111: ...JOHNSON CONTROLS 111 FORM 150 62 nm6 103 2 This page intentionally left blank...
Page 133: ...JOHNSON CONTROLS 133 FORM 150 62 nm6 103 4 LD08851...
Page 135: ...JOHNSON CONTROLS 135 FORM 150 62 nm6 103 4 This page intentionally left blank...
Page 137: ...JOHNSON CONTROLS 137 FORM 150 62 nm6 103 LD08855 4...
Page 139: ...JOHNSON CONTROLS 139 FORM 150 62 nm6 103 4 This page intentionally left blank...
Page 141: ...JOHNSON CONTROLS 141 FORM 150 62 nm6 103 LD08858 4...
Page 143: ...JOHNSON CONTROLS 143 FORM 150 62 nm6 103 4 This page intentionally left blank...
Page 145: ...JOHNSON CONTROLS 145 FORM 150 62 nm6 103 LD08862 4...
Page 147: ...JOHNSON CONTROLS 147 FORM 150 62 nm6 103 4 This page intentionally left blank...
Page 149: ...JOHNSON CONTROLS 149 FORM 150 62 nm6 103 LD08865...
Page 151: ...JOHNSON CONTROLS 151 FORM 150 62 nm6 103 LD08867...
Page 153: ...JOHNSON CONTROLS 153 FORM 150 62 nm6 103 LD08869...
Page 155: ...JOHNSON CONTROLS 155 FORM 150 62 nm6 103 4 This page intentionally left blank...
Page 157: ...JOHNSON CONTROLS 157 FORM 150 62 nm6 103 LD08872...
Page 159: ...JOHNSON CONTROLS 159 FORM 150 62 nm6 103 4 LD08877...
Page 161: ...JOHNSON CONTROLS 161 FORM 150 62 nm6 103 LD08874...
Page 163: ...JOHNSON CONTROLS 163 FORM 150 62 nm6 103 This page intentionally left blank...
Page 165: ...JOHNSON CONTROLS 165 FORM 150 62 nm6 103 4 LD08830...
Page 167: ...JOHNSON CONTROLS 167 FORM 150 62 nm6 103 4 LD08833...
Page 169: ...JOHNSON CONTROLS 169 FORM 150 62 nm6 103 4 LD08835...
Page 171: ...JOHNSON CONTROLS 171 FORM 150 62 nm6 103 4 This page intentionally left blank...
Page 173: ...JOHNSON CONTROLS 173 FORM 150 62 nm6 103 4 LD08837...
Page 175: ...JOHNSON CONTROLS 175 FORM 150 62 nm6 103 4 LD08840...
Page 177: ...JOHNSON CONTROLS 177 FORM 150 62 nm6 103 4 LD08842...
Page 179: ...JOHNSON CONTROLS 179 FORM 150 62 nm6 103 4 This page intentionally left blank...
Page 181: ...JOHNSON CONTROLS 181 FORM 150 62 nm6 103 4 LD08844...
Page 183: ...JOHNSON CONTROLS 183 FORM 150 62 nm6 103 4 LD08847...
Page 185: ...JOHNSON CONTROLS 185 FORM 150 62 nm6 103 4 LD08849...
Page 187: ...JOHNSON CONTROLS 187 FORM 150 62 nm6 103 4 This page intentionally left blank...