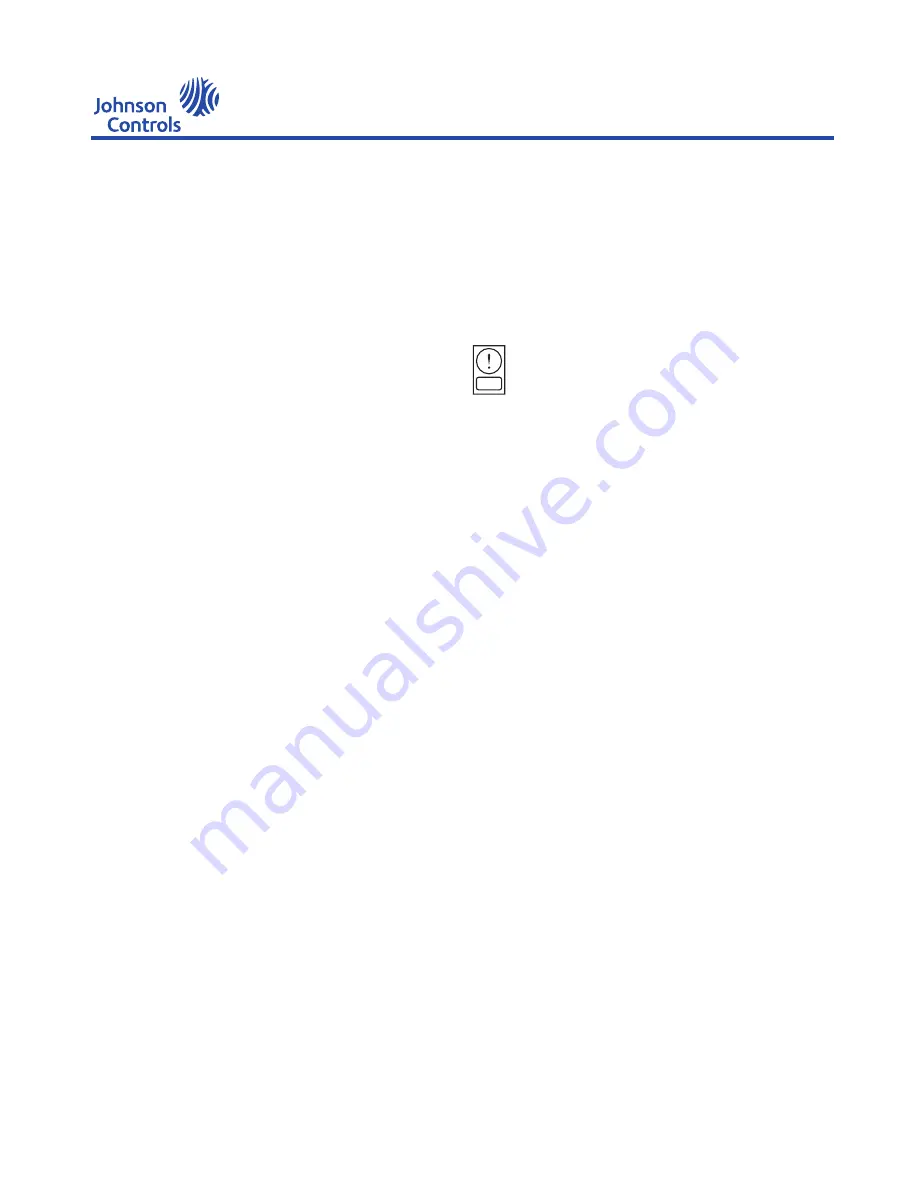
5. When absolute tightness of the system has been
established, blow the mixture of refrigerant and nitrogen
through the charging valves
8.7 Evacuation And Dehydration Of Unit
Vacuum Dehydration
Should the chiller be opened to the atmosphere for
lengthy repair or service, follow the Vacuum Dehydration
Guidelines to ensure that all air, moisture and non-
condensable gases are removed prior to placing the chiller
into service.
Vacuum Testing
The vacuum test should be conducted as follows:
1. Connect a high capacity vacuum pump, with indicator,
to the system charging valve.
2. Open wide all system valves, including the purge and
gauge valves. Be sure all valves to atmosphere are closed.
3. Operate the vacuum pump until a wet bulb temperature
of 0
℃
or a pressure of 5mm Hg is reached.
4. To improve evacuation circulate hot water(not to exc-
eed 52
℃
) through the evaporator and condenser tubes to
thoroughly dehydrate the shells. If a source of hot water is
not readily available, a portable water heater should be
employed. DO NOT USE STEAM.A suggested method is
to connect a hose between the source of hot water under
pressure and evaporator heat drain connec-tion, out the
evaporator vent connection, into the conde-nser heat drain
and out the condenser vent. To avoid the possibility of
causing leaks, the temperature should be br-ought up
slowly so that the tubes an shell are heated evenly.
5. Close the system charging valve and stop valve bet-
ween the vacuum indicator and the vacuum pump. then
disconnected the vacuum pump leaving the vacuum ind-
icator in place.
6. Hold the vacuum obtained in step3 in the system for 8
hours; the slighter rise in pressure indicates a leak or the
pressure of moisture, or both. If, after 8hours the wet bulb
temperature in the vacuum indicator has not risen above 5
℃
or a pressure of 6.3mm Hg, the system may be cons-idered
tight.
Be sure the vacuum indicator is valved off while
holding the system vacuum and be sure to open the
valve between the vacuum indicator and the system
when checking the vacuum for the 8 hours period.
7. If the vacuum does not hold for 8 hours with the limits
specified in step 6 above, the leak must be found and
repaired.
8.8 working conditions
Reading the working pressure and temperature from the
display panel by pressing the
“
display
”
key. Comfirm
that whether these value is within the working limits.
8.9 Scheduled Maintenance
The maintenance operations detailed in the following table
should be carried out on aregular basis by a suitably
qualified Service Engineer, It should be noted that the
interval necessary between each 'minor' and 'major' service
can vary depending on, for instance, application, site
conditions and expected operating schedule. Normally a
minor 'service' should be carried out every three to six
months and a 'major' service once a year.It is recommended
that your local York Service Centre is contacted for
recommendations for individual sites.
NOTE
YEWS-E Water Cooling Screw Chiller/Heat Pump
61
Summary of Contents for YEWS Series
Page 79: ...YEWS electrical drawing compressor for 50Hz power 74...
Page 80: ...YEWS electrical drawing main board YEWS100H 130H 170H 200H 210H for 50Hz power 75...
Page 81: ...YEWSelectrical drawing main board YEWS215P for 50Hz power 76...
Page 82: ...77 YEWS electrical drawing Main Board YEWS100P 130P 170P 200P for 50Hz power...
Page 83: ...YEWS electrical drawing compressor for 60Hz power 78...
Page 84: ...YEWS electrical drawing main board YEWS100H 130H 170H 200H for 60Hz power 79...
Page 85: ...YEWS electrical drawing main board YEWS215P for 60Hz power 80...
Page 86: ...YEWS field connection for 60Hz power 81...
Page 87: ...Transformer for230V 3P 60Hz Application 82...
Page 88: ...Form No AP1105 IOM01 1216 EN Supersedes AP1105 IOM01 0316 EN...