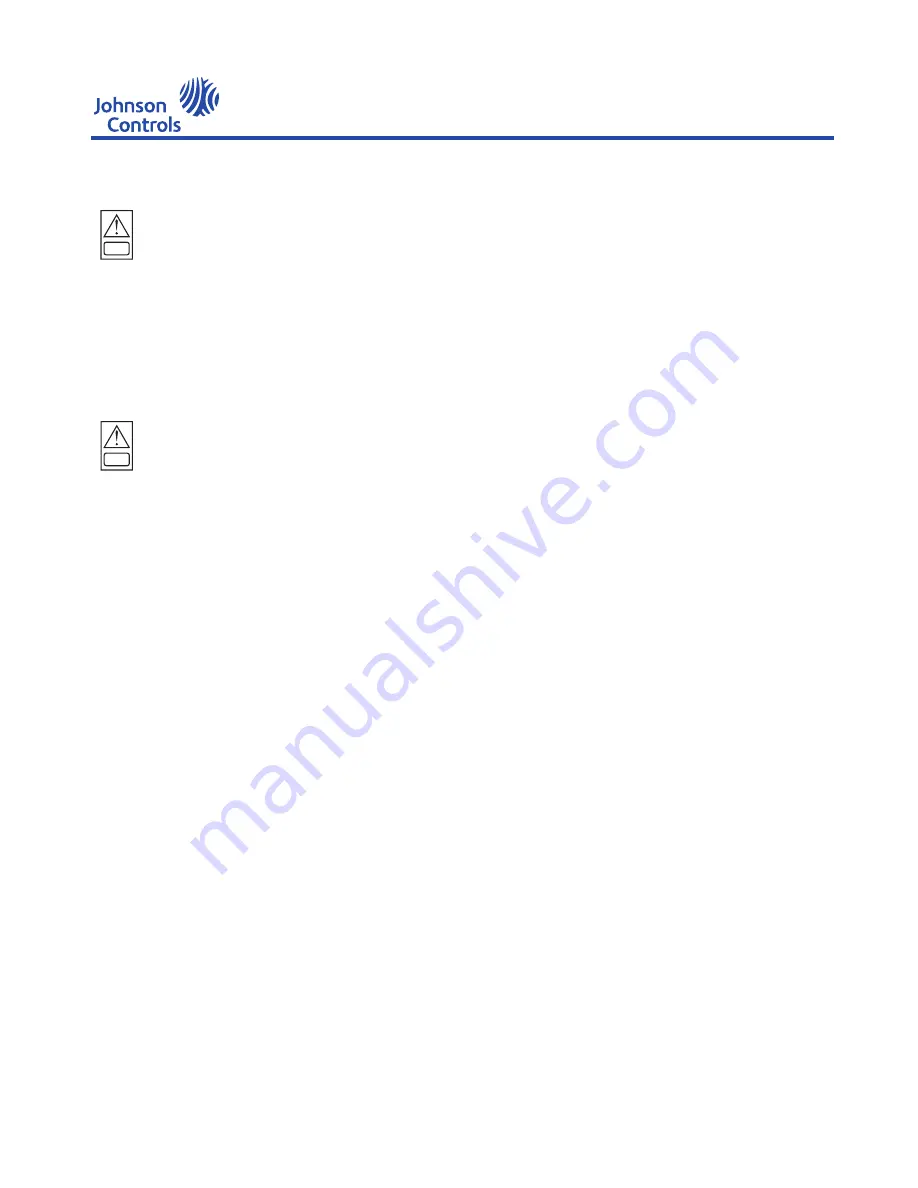
6 COMMISSIONING
6.1 PREPARATION
Commissioning of this unit should only be
carried out by YORK Authorized personnel.
Especially, this section must be read in conjunction with
the control system operation onstruction in section 5.
Power Off
The following basic checks should be made with the
customer power supply to the unit switched off.
Ensure all sources of supply to the unit are
padlocked in the OFF position.
Inspection
Inspect unit for installation damage. If found, take action
or repair as appropriate.
Refrigerant Charge
Packaged units are normally shipped as standard with a
full refrigerant operating charge. Check that refrigerant
pressure is present in the system and that no leaks are
apparent. If no pressure is present, a leak test must be
undertaken, located and repaired the leak(s). These
systems must be evacuated with a suitable vacuum
pump/recovery unit as appropriate to below 500
μ
mHg.
Valves
Open diacharge valve on compressor and liquid line angle
valve under condenser fully (counterclockwise) then close
one turn of the stem to ensure operating pressure is fed to
pressure transducers. Open all angle valves on the oil
return line and eductor line.
Isolation / Protection
Verify all sources of electrical supply to the unit are taken
from a single point of isolation.
Control Panel
Make sure the control panle is free of foreign materials
(wire, metal chips, etc.) and clean out foreign materials if
it is found.
Power Connections
Check that the customer power cables are connected
correctly to the circuit breaker. Ensure that connections
of power cables within the panels to the circuit breaker
are tight.
Earthing
Make sure all the protective conductor is properly and
tightly connected to the ground.
Oil heater
Verify that the oil heater is powe on. If the chiller
repowered after it have been power off for more than 15
days, the compressor are not allowed to run unless the oil
heater has been work for more than 5 hours.
Water System
Verify the chilled liquid system has been installed
correctly, and has been commissioned with the correct
direction of water flow through the cooler. The inlet
should be connected to the bottom nozzle of water box of
the cooler and the outlet to the top one. Purge air using
the plugged air vent mounted on the top of water box.
Flow rates and pressure drops must be within the limits
given in the Section 10. Out of these limits is undesirable
and could cause damage.
Low temperature brine chiller
Confirm the freezing point of the evaporator brine fluid.
Using a hydrometer or an optical refractometer to test the
concentration of the birne and figure out the freezing
point. When working on the ITS mode, the LOW LELT/
LEP UNLOAD/LEP SHUT DOWN should be reset.
Make sure the temperature corresponding to the LEP
SHUT DOWN and the LOW LELT setpoint are higher
than the freezing point of brine, and any of these two
temperature should be at least 3
℃
higher than the brine
freezing point.
WARNING
CAUTION
YEWS-E Water Cooling Screw Chiller/Heat Pump
49
Summary of Contents for YEWS Series
Page 79: ...YEWS electrical drawing compressor for 50Hz power 74...
Page 80: ...YEWS electrical drawing main board YEWS100H 130H 170H 200H 210H for 50Hz power 75...
Page 81: ...YEWSelectrical drawing main board YEWS215P for 50Hz power 76...
Page 82: ...77 YEWS electrical drawing Main Board YEWS100P 130P 170P 200P for 50Hz power...
Page 83: ...YEWS electrical drawing compressor for 60Hz power 78...
Page 84: ...YEWS electrical drawing main board YEWS100H 130H 170H 200H for 60Hz power 79...
Page 85: ...YEWS electrical drawing main board YEWS215P for 60Hz power 80...
Page 86: ...YEWS field connection for 60Hz power 81...
Page 87: ...Transformer for230V 3P 60Hz Application 82...
Page 88: ...Form No AP1105 IOM01 1216 EN Supersedes AP1105 IOM01 0316 EN...