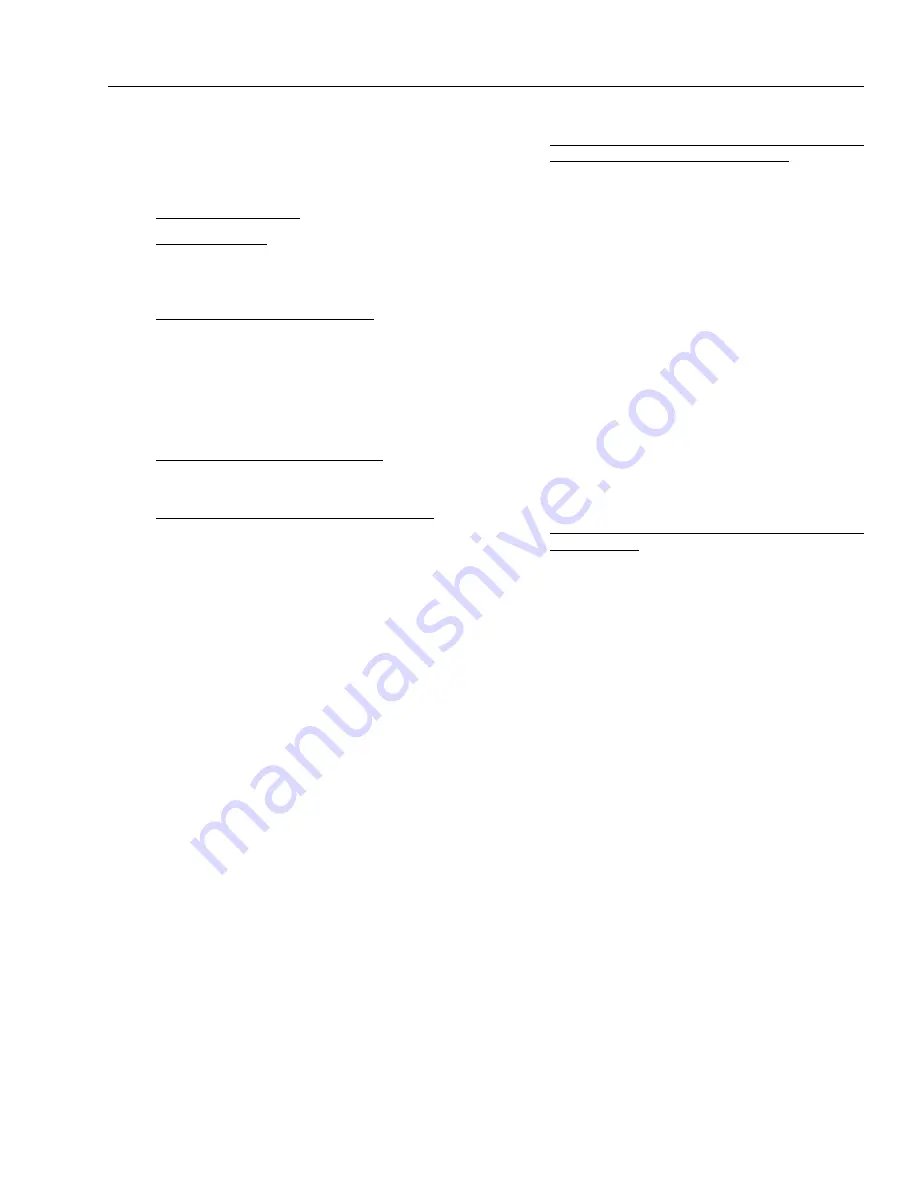
SECTION 6 - JLG CONTROL SYSTEM
3121619
6-105
Testing & Evaluation
Refer to Troubleshooting if the Load Sensing System fails to
meet these guidelines.
1.
Connect the JLG Analyzer.
2.
Level the Platform. The platform should be approxi-
mately level for analysis, or the guidelines below will not
be applicable. Level the platform from Ground Control
(if necessary) to within ±5 degrees.
3.
Observe the Empty Platform Weight. Proceed to the
DIAGNOSTICS, PLTLOAD sub-menu and observe the
measured platform load. All tools, debris, and customer-
installed devices shall be removed during evaluation.
Ideally, the PLTLOAD should be zero but can vary ±15lbs
(± 7kg). Further, the reading should be stable and
should not vary by more than ±2lbs (±1kg) (unless there
is heavy influence from wind or vibration).
4.
Use the Technician’s Weight to Evaluate. The technician
should enter the platform and record the PLTLOAD read-
ing while standing in the center of the platform.
5.
Confirm Control System Warnings and Interlocks. Using
the keyswitch, select Platform Mode and power-up.
Start the vehicle’s engine and ensure that all controls are
functional and the Load Sensing System’s Overload
Visual and Audible Warnings are not active. Simulate an
Overload by unplugging the Shear Beam Load Cell. The
Overload Visual Warning should flash, and the Audible
Warning (at Platform and Ground) should sound for 5
seconds On, and 2 seconds Off. With the engine run-
ning, all control should be prevented. Cycle the Platform
EMS to stop the engine and then power-up again. The
Overload Visual and Audible Warning should continue.
Confirm that controls are responsive when using the
Auxiliary Power Unit for emergency movement. Recon-
nect the Load Cell. The Overload Visual and Audible
Warnings should cease and normal control function
should return. Switch the vehicle’s keyswitch to Ground
Mode and repeat the above procedure. The Overload
Visual Warning at the Ground Controls should flash, and
the Audible Warning (at Platform and Ground) should
sound for 5 seconds On, 2 seconds Off. However, the
controls should remain functional when using the
engine and the Auxiliary Power Unit (if the Control Sys-
tem’s MACHINE SETUP, LOAD is set to “2=CUTOUT PLT”. If
set to “3=CUTOUT ALL”, then Ground Controls will be
prevented when using the engine as in the platform).
6.
Confirm Control System Capacity Indication (optional
for vehicles with Dual Capacity Ratings). For vehicles
equipped with a Capacity Select switch on the Platform
Console Box, it is necessary to examine an additional
interface between the Load Sensing System and the
Control System. Using the keyswitch, select Platform
Mode and power-up. If necessary, put the boom in the
transport position (completely stowed) and center the
Jib Plus (if equipped). Place the Capacity Select switch in
the unrestricted position and ensure that the proper
indicator illuminates on the Platform Console Box. Plug
the JLG Analyzer into the Analyzer connection and pro-
ceed to the DIAGNOSTICS, SYSTEM submenu. Ensure
that the CAPACITY displays indicate OFF. Place the
Capacity Select switch in the unrestricted position (if so
equipped) and ensure that the proper indicator illumi-
nates on the Platform Console Box (but does not flash).
For vehicles with unrestricted capacity, ensure that the
unrestricted CAPACITY display indicates ON but the
restricted CAPACITY indicates OFF. For vehicles with
restricted capacity, ensure that the unrestricted CAPAC-
ITY display indicates OFF but the restricted CAPACITY
indicates ON.
7.
Confirm Load Sensing System Performance with Cali-
brated Weights. Operate the vehicle from Ground Con-
trol and place the boom in the transport position (fully
stowed) for safety. Plug the JLG Analyzer into the control
system connection and proceed to the DIAGNOSTICS,
PLTLOAD display. Place 500lbs (230kg) in the platform
and ensure that PLTLOAD is with ±5% of the actual
weight. For Dual Capacity vehicles, do the same for the
alternate capacity (unrestricted or restricted).
Summary of Contents for 1850SJ
Page 1: ...Service and Maintenance Manual Model 1850SJ 3121619 June 29 2018 Rev J AS NZS...
Page 2: ......
Page 21: ...3121619 xvii LIST OF FIGURES FIGURE NO TITLE PAGE NO Thispageleftblankintentionally...
Page 24: ...xx 3121619 LIST OF TABLES TABLE NO TITLE PAGE NO Thispageleftblankintentionally...
Page 50: ...SECTION 2 GENERAL 2 12 3121619 NOTES...
Page 55: ...SECTION 3 CHASSIS TURNTABLE 3121619 3 5 This page left blank intentionally...
Page 56: ...SECTION 3 CHASSIS TURNTABLE 3 6 3121619 Figure 3 4 Axle Hose Routing Sheet 1 of 2...
Page 57: ...SECTION 3 CHASSIS TURNTABLE 3121619 3 7 Figure 3 5 Axle Hose Routing Sheet 2 of 2...
Page 58: ...SECTION 3 CHASSIS TURNTABLE 3 8 3121619 Figure 3 6 Steering Axle Hydraulic Circuit...
Page 61: ...SECTION 3 CHASSIS TURNTABLE 3121619 3 11 Figure 3 9 Turntable Hydraulic System...
Page 92: ...SECTION 3 CHASSIS TURNTABLE 3 42 3121619 Figure 3 39 Swing Bearing Wear Tolerance...
Page 94: ...SECTION 3 CHASSIS TURNTABLE 3 44 3121619 Figure 3 41 Swing Bearing Removal Sheet 2 of 4...
Page 110: ...SECTION 3 CHASSIS TURNTABLE 3 60 3121619 Figure 3 54 Engine Electrical Circuit...
Page 169: ...SECTION 4 BOOM PLATFORM 3121619 4 7 Figure 4 1 Boom Hydraulic System...
Page 173: ...SECTION 4 BOOM PLATFORM 3121619 4 11 Figure 4 2 Boom Assembly Sheet 1 of 9...
Page 174: ...SECTION 4 BOOM PLATFORM 4 12 3121619 Figure 4 3 Boom Assembly Sheet 2 of 9...
Page 175: ...SECTION 4 BOOM PLATFORM 3121619 4 13 Figure 4 4 Boom Assembly Sheet 3 of 9...
Page 176: ...SECTION 4 BOOM PLATFORM 4 14 3121619 Figure 4 5 Boom Assembly Sheet 4 of 9...
Page 177: ...SECTION 4 BOOM PLATFORM 3121619 4 15 Figure 4 6 Boom Assembly Sheet 5 of 9...
Page 178: ...SECTION 4 BOOM PLATFORM 4 16 3121619 Figure 4 7 Boom Assembly Sheet 6 of 9...
Page 179: ...SECTION 4 BOOM PLATFORM 3121619 4 17 Figure 4 8 Boom Assembly Sheet 7 of 9...
Page 180: ...SECTION 4 BOOM PLATFORM 4 18 3121619 Figure 4 9 Boom Assembly Sheet 8 of 9...
Page 181: ...SECTION 4 BOOM PLATFORM 3121619 4 19 Figure 4 10 Boom Assembly Sheet 9 of 9...
Page 187: ...SECTION 4 BOOM PLATFORM 3121619 4 25 Figure 4 16 Boom Assembly Torque Values Sheet 1 of 4...
Page 188: ...SECTION 4 BOOM PLATFORM 4 26 3121619 Figure 4 17 Boom Assembly Torque Values Sheet 2 of 4...
Page 189: ...SECTION 4 BOOM PLATFORM 3121619 4 27 Figure 4 18 Boom Assembly Torque Values Sheet 3 of 4...
Page 190: ...SECTION 4 BOOM PLATFORM 4 28 3121619 Figure 4 19 Boom Assembly Torque Values Sheet 4 of 4...
Page 201: ...SECTION 4 BOOM PLATFORM 3121619 4 39 Figure 4 20 Hose Adjustment...
Page 202: ...SECTION 4 BOOM PLATFORM 4 40 3121619 Figure 4 21 Section 3 Boom Cables...
Page 203: ...SECTION 4 BOOM PLATFORM 3121619 4 41 Figure 4 22 Section 4 Boom Cables...
Page 204: ...SECTION 4 BOOM PLATFORM 4 42 3121619 Figure 4 23 Section 5 Boom Cables...
Page 205: ...SECTION 4 BOOM PLATFORM 3121619 4 43 Figure 4 24 Jib Hydraulics Sheet 1 of 7...
Page 234: ...SECTION 4 BOOM PLATFORM 4 72 3121619 Figure 4 44 Powertrack Shimming Instructions...
Page 239: ...SECTION 4 BOOM PLATFORM 3121619 4 77 Figure 4 49 Powertrack Hose Installation Sheet 1 of 4...
Page 240: ...SECTION 4 BOOM PLATFORM 4 78 3121619 Figure 4 50 Powertrack Hose Installation Sheet 2 of 4...
Page 241: ...SECTION 4 BOOM PLATFORM 3121619 4 79 Figure 4 51 Powertrack Hose Installation Sheet 3 of 4...
Page 242: ...SECTION 4 BOOM PLATFORM 4 80 3121619 Figure 4 52 Powertrack Hose Installation Sheet 4 of 4...
Page 252: ...SECTION 4 BOOM PLATFORM 4 90 3121619 NOTES...
Page 432: ...SECTION 5 BASIC HYDRAULIC INFORMATION HYDRAULIC SCHEMATICS 5 180 3121619 NOTES...
Page 527: ...SECTION 6 JLG CONTROL SYSTEM 3121619 6 95 Figure 6 36 LSS Installation Sheet 1 of 4...
Page 528: ...SECTION 6 JLG CONTROL SYSTEM 6 96 3121619 Figure 6 37 LSS Installation Sheet 2 of 4...
Page 529: ...SECTION 6 JLG CONTROL SYSTEM 3121619 6 97 Figure 6 38 LSS Installation Sheet 3 of 4...
Page 530: ...SECTION 6 JLG CONTROL SYSTEM 6 98 3121619 Figure 6 39 LSS Installation Sheet 4 of 4...
Page 710: ...SECTION 7 BASIC ELECTRICAL INFORMATION ELECTRICAL SCHEMATICS 7 118 3121619 NOTES...
Page 711: ......