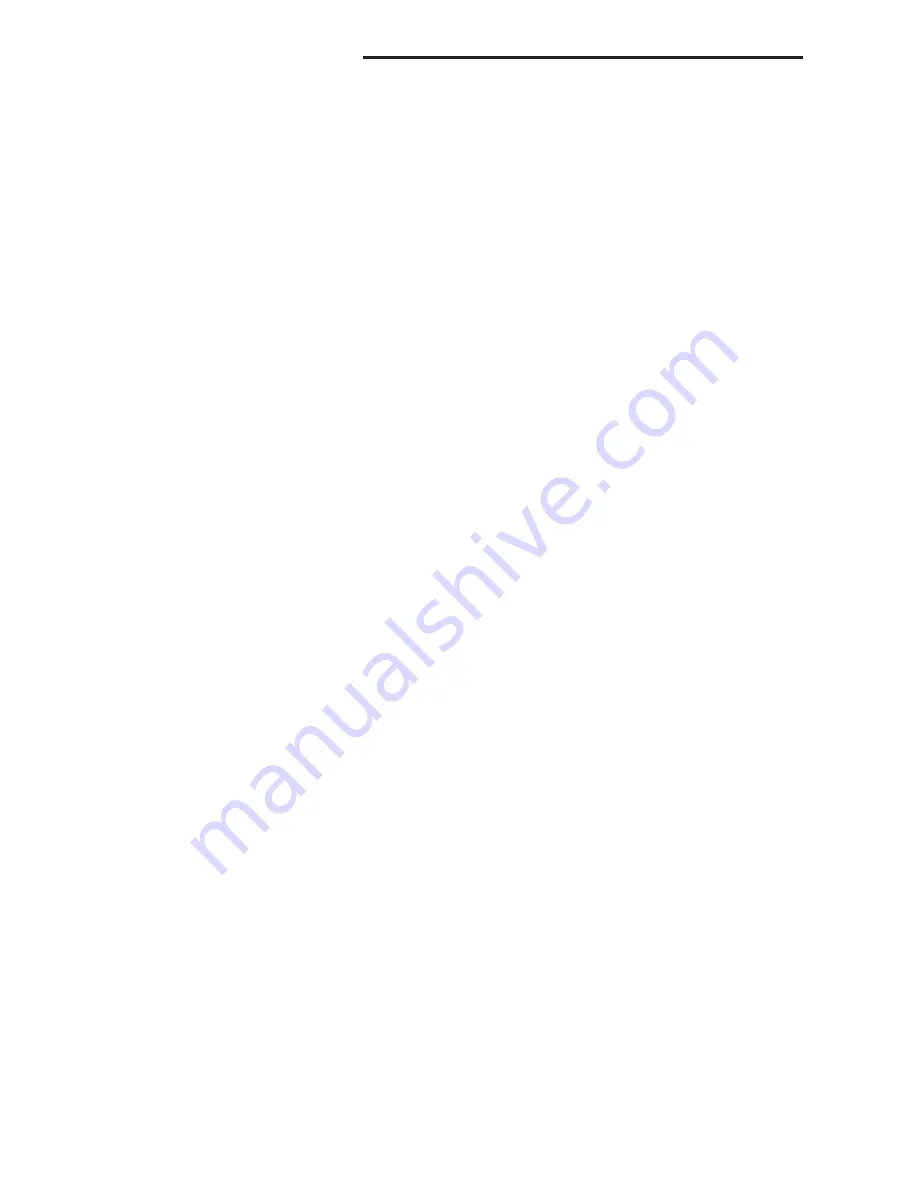
tions listed above; a pump which contains a switch,
two check valves and a spring/diaphragm, a canister
vent valve (CVV) seal which contains a spring loaded
vent seal valve.
Immediately after a cold start, between predeter-
mined temperature thresholds limits, the three port
solenoid is briefly energized. This initializes the
pump by drawing air into the pump cavity and also
closes the vent seal. During non test conditions the
vent seal is held open by the pump diaphragm
assembly which pushes it open at the full travel posi-
tion. The vent seal will remain closed while the
pump is cycling due to the reed switch triggering of
the three port solenoid that prevents the diaphragm
assembly from reaching full travel. After the brief
initialization period, the solenoid is de-energized
allowing atmospheric pressure to enter the pump
cavity, thus permitting the spring to drive the dia-
phragm which forces air out of the pump cavity and
into the vent system. When the solenoid is energized
and de energized, the cycle is repeated creating flow
in typical diaphragm pump fashion. The pump is con-
trolled in 2 modes:
Pump Mode: The pump is cycled at a fixed rate to
achieve a rapid pressure build in order to shorten the
overall test length.
Test Mode: The solenoid is energized with a fixed
duration pulse. Subsequent fixed pulses occur when
the diaphragm reaches the Switch closure point.
The spring in the pump is set so that the system
will achieve an equalized pressure of about 7.5” H20.
The cycle rate of pump strokes is quite rapid as the
system begins to pump up to this pressure. As the
pressure increases, the cycle rate starts to drop off. If
there is no leak in the system, the pump would even-
tually stop pumping at the equalized pressure. If
there is a leak, it will continue to pump at a rate rep-
resentative of the flow characteristic of the size of the
leak. From this information we can determine if the
leak is larger than the required detection limit (cur-
rently set at.040” orifice by CARB). If a leak is
revealed during the leak test portion of the test, the
test is terminated at the end of the test mode and no
further system checks will be performed.
After passing the leak detection phase of the test,
system pressure is maintained by turning on the
LDP’s solenoid until the purge system is activated.
Purge activation in effect creates a leak. The cycle
rate is again interrogated and when it increases due
to the flow through the purge system, the leak check
portion of the diagnostic is complete.
The canister vent valve will unseal the system
after completion of the test sequence as the pump
diaphragm assembly moves to the full travel position.
Evaporative system functionality will be verified by
using the stricter evap purge flow monitor. At an
appropriate warm idle the LDP will be energized to
seal the canister vent. The purge flow will be clocked
up from some small value in an attempt to see a
shift in the 02 control system. If fuel vapor, indicated
by a shift in the 02 control, is present the test is
passed. If not, it is assumed that the purge system is
not functioning in some respect. The LDP is again
turned off and the test is ended.
MISFIRE MONITOR
Excessive engine misfire results in increased cata-
lyst temperature and causes an increase in HC emis-
sions. Severe misfires could cause catalyst damage.
To prevent catalytic convertor damage, the PCM
monitors engine misfire.
The Powertrain Control Module (PCM) monitors
for misfire during most engine operating conditions
(positive torque) by looking at changes in the crank-
shaft speed. If a misfire occurs the speed of the
crankshaft will vary more than normal.
FUEL SYSTEM MONITOR
To comply with clean air regulations, vehicles are
equipped with catalytic converters. These converters
reduce the emission of hydrocarbons, oxides of nitro-
gen and carbon monoxide. The catalyst works best
when the Air Fuel (A/F) ratio is at or near the opti-
mum of 14.7 to 1.
The PCM is programmed to maintain the optimum
air/fuel ratio of 14.7 to 1. This is done by making
short term corrections in the fuel injector pulse width
based on the O2S sensor output. The programmed
memory acts as a self calibration tool that the engine
controller uses to compensate for variations in engine
specifications, sensor tolerances and engine fatigue
over the life span of the engine. By monitoring the
actual fuel-air ratio with the O2S sensor (short term)
and multiplying that with the program long-term
(adaptive) memory and comparing that to the limit,
it can be determined whether it will pass an emis-
sions test. If a malfunction occurs such that the PCM
cannot maintain the optimum A/F ratio, then the
MIL will be illuminated.
CATALYST MONITOR
To comply with clean air regulations, vehicles are
equipped with catalytic converters. These converters
reduce the emission of hydrocarbons, oxides of nitro-
gen and carbon monoxide.
Normal vehicle miles or engine misfire can cause a
catalyst to decay. A meltdown of the ceramic core can
cause a reduction of the exhaust passage. This can
increase vehicle emissions and deteriorate engine
performance, driveability and fuel economy.
The catalyst monitor uses dual oxygen sensors
(O2S’s) to monitor the efficiency of the converter. The
dual O2S’s sensor strategy is based on the fact that
25 - 20
EMISSION CONTROL SYSTEMS
XJ
DESCRIPTION AND OPERATION (Continued)
Summary of Contents for 200 Cherokee
Page 5: ...FASTENER IDENTIFICATION 4 INTRODUCTION XJ DESCRIPTION AND OPERATION Continued ...
Page 6: ...FASTENER STRENGTH XJ INTRODUCTION 5 DESCRIPTION AND OPERATION Continued ...
Page 8: ...METRIC CONVERSION CHART XJ INTRODUCTION 7 DESCRIPTION AND OPERATION Continued ...
Page 9: ...TORQUE SPECIFICATIONS 8 INTRODUCTION XJ DESCRIPTION AND OPERATION Continued ...
Page 47: ......
Page 107: ...Fig 105 Gear Tooth Contact Patterns 3 60 TUBE 181 AND 186 FBI AXLE XJ ADJUSTMENTS Continued ...
Page 111: ...Installer D 144 Installer W 262 3 64 TUBE 181 AND 186 FBI AXLE XJ SPECIAL TOOLS Continued ...
Page 145: ...Fig 79 Gear Tooth Contact Patterns 3 98 194 RBI AXLE XJ ADJUSTMENTS Continued ...
Page 177: ...Fig 59 Gear Tooth Contact Patterns 3 130 8 1 4 REAR AXLE XJ ADJUSTMENTS Continued ...
Page 230: ...Fig 8 Clutch Components And Inspection XJ CLUTCH 6 5 DIAGNOSIS AND TESTING Continued ...
Page 241: ......
Page 357: ......
Page 367: ......
Page 449: ......
Page 451: ......
Page 475: ......
Page 484: ...SPECIAL TOOLS HEADLAMP ALIGNMENT Headlamp Aiming Kit C 4466 A XJ LAMPS 8L 9 ...
Page 507: ......
Page 537: ......
Page 551: ......
Page 571: ......
Page 577: ......
Page 583: ......
Page 613: ......
Page 615: ......
Page 631: ......
Page 669: ......
Page 707: ......
Page 735: ......
Page 783: ......
Page 789: ......
Page 805: ......
Page 823: ......
Page 827: ......
Page 851: ......
Page 863: ......
Page 867: ......
Page 893: ......
Page 921: ......
Page 925: ......
Page 931: ......
Page 937: ......
Page 1047: ......
Page 1072: ...Fig 16 2 5L Engine XJ 8W 90 CONNECTOR LOCATIONS 8W 90 25 DESCRIPTION AND OPERATION Continued ...
Page 1073: ...Fig 17 4 0L Engine 8W 90 26 8W 90 CONNECTOR LOCATIONS XJ DESCRIPTION AND OPERATION Continued ...
Page 1074: ...Fig 18 4 0L Engine XJ 8W 90 CONNECTOR LOCATIONS 8W 90 27 DESCRIPTION AND OPERATION Continued ...
Page 1087: ...Fig 31 Liftgate 8W 90 40 8W 90 CONNECTOR LOCATIONS XJ DESCRIPTION AND OPERATION Continued ...
Page 1099: ......
Page 1129: ......
Page 1249: ......
Page 1331: ...Fig 6 Frame Dimensions 13 8 FRAME AND BUMPERS XJ SPECIFICATIONS Continued ...
Page 1333: ......
Page 1335: ......
Page 1869: ......
Page 1875: ......
Page 1887: ......
Page 1912: ...Fig 3 Hood Components XJ BODY 23 25 REMOVAL AND INSTALLATION Continued ...
Page 1955: ...WELD LOCATIONS UPPER COWL 23 68 BODY XJ SPECIFICATIONS Continued ...
Page 1956: ...UPPER COWL XJ BODY 23 69 SPECIFICATIONS Continued ...
Page 1957: ...COWL 23 70 BODY XJ SPECIFICATIONS Continued ...
Page 1958: ...A PILLAR XJ BODY 23 71 SPECIFICATIONS Continued ...
Page 1959: ...A PILLAR 23 72 BODY XJ SPECIFICATIONS Continued ...
Page 1960: ...A PILLAR XJ BODY 23 73 SPECIFICATIONS Continued ...
Page 1961: ...A PILLAR 23 74 BODY XJ SPECIFICATIONS Continued ...
Page 1962: ...B PILLAR XJ BODY 23 75 SPECIFICATIONS Continued ...
Page 1963: ...D PILLAR 23 76 BODY XJ SPECIFICATIONS Continued ...
Page 1964: ...FUEL FILLER OPENING XJ BODY 23 77 SPECIFICATIONS Continued ...
Page 1965: ...CARGO AREA FLOOR PAN 23 78 BODY XJ SPECIFICATIONS Continued ...
Page 1966: ...ROOF AND D PILLAR XJ BODY 23 79 SPECIFICATIONS Continued ...
Page 1967: ...LIFTGATE OPENING 23 80 BODY XJ SPECIFICATIONS Continued ...
Page 1968: ...ROOF XJ BODY 23 81 SPECIFICATIONS Continued ...
Page 1969: ...ROOF 23 82 BODY XJ SPECIFICATIONS Continued ...
Page 1970: ...FRAME RAIL XJ BODY 23 83 SPECIFICATIONS Continued ...
Page 1971: ...FRAME RAIL 23 84 BODY XJ SPECIFICATIONS Continued ...
Page 1972: ...FRAME RAIL XJ BODY 23 85 SPECIFICATIONS Continued ...
Page 1973: ...FRAME RAIL 23 86 BODY XJ SPECIFICATIONS Continued ...
Page 1974: ...REINFORCEMENT XJ BODY 23 87 SPECIFICATIONS Continued ...
Page 1975: ...FRONT INNER FENDER 23 88 BODY XJ SPECIFICATIONS Continued ...
Page 1976: ...FRONT INNER FENDER AND RADIATOR CLOSURE PANEL XJ BODY 23 89 SPECIFICATIONS Continued ...
Page 1977: ...REINFORCEMENT 23 90 BODY XJ SPECIFICATIONS Continued ...
Page 1978: ...FRONT FENDER XJ BODY 23 91 SPECIFICATIONS Continued ...
Page 1979: ...BODY SIDE 23 92 BODY XJ SPECIFICATIONS Continued ...
Page 1980: ...REAR WHEELHOUSE XJ BODY 23 93 SPECIFICATIONS Continued ...
Page 1981: ...REAR INNER WHEELHOUSE 23 94 BODY XJ SPECIFICATIONS Continued ...
Page 1982: ...BODY SIDE XJ BODY 23 95 SPECIFICATIONS Continued ...
Page 1983: ...BODY SIDE 23 96 BODY XJ SPECIFICATIONS Continued ...
Page 1984: ...BODY SIDE XJ BODY 23 97 SPECIFICATIONS Continued ...
Page 1985: ...BODY SIDE 23 98 BODY XJ SPECIFICATIONS Continued ...
Page 1986: ...BODY SIDE XJ BODY 23 99 SPECIFICATIONS Continued ...
Page 1987: ...BODY SIDE 23 100 BODY XJ SPECIFICATIONS Continued ...
Page 1988: ...UNDERBODY XJ BODY 23 101 SPECIFICATIONS Continued ...
Page 1989: ...UNDERBODY 23 102 BODY XJ SPECIFICATIONS Continued ...
Page 1990: ...UNDERBODY XJ BODY 23 103 SPECIFICATIONS Continued ...
Page 1991: ...UNDERBODY 23 104 BODY XJ SPECIFICATIONS Continued ...
Page 1992: ...UNDERBODY XJ BODY 23 105 SPECIFICATIONS Continued ...
Page 1993: ...UNDERBODY 23 106 BODY XJ SPECIFICATIONS Continued ...
Page 1994: ...UNDERBODY XJ BODY 23 107 SPECIFICATIONS Continued ...
Page 1995: ...UNDERBODY 23 108 BODY XJ SPECIFICATIONS Continued ...
Page 1996: ...UNDERBODY XJ BODY 23 109 SPECIFICATIONS Continued ...
Page 1997: ...UNDERBODY 23 110 BODY XJ SPECIFICATIONS Continued ...
Page 1998: ...UNDERBODY XJ BODY 23 111 SPECIFICATIONS Continued ...
Page 1999: ...BODY SEALING LOCATIONS APPLICATION METHODS 23 112 BODY XJ SPECIFICATIONS Continued ...
Page 2000: ...COWL AND DASH PANEL XJ BODY 23 113 SPECIFICATIONS Continued ...
Page 2001: ...DASH PANEL AND FLOOR PAN 23 114 BODY XJ SPECIFICATIONS Continued ...
Page 2002: ...FLOOR PAN XJ BODY 23 115 SPECIFICATIONS Continued ...
Page 2003: ...REAR INNER WHEELHOUSE 23 116 BODY XJ SPECIFICATIONS Continued ...
Page 2004: ...FRONT INNER WHEELHOUSE XJ BODY 23 117 SPECIFICATIONS Continued ...
Page 2005: ...BODY SIDE 23 118 BODY XJ SPECIFICATIONS Continued ...
Page 2006: ...BODY SIDE XJ BODY 23 119 SPECIFICATIONS Continued ...
Page 2007: ...BODY SIDE 23 120 BODY XJ SPECIFICATIONS Continued ...
Page 2008: ...ROOF PANEL XJ BODY 23 121 SPECIFICATIONS Continued ...
Page 2009: ...FUEL FILLER HOUSING 23 122 BODY XJ SPECIFICATIONS Continued ...
Page 2010: ...LIFTGATE OPENING XJ BODY 23 123 SPECIFICATIONS Continued ...
Page 2011: ...STRUCTURAL ADHESIVE LOCATIONS LEFT QUARTER PANEL 23 124 BODY XJ SPECIFICATIONS Continued ...
Page 2012: ...REAR WHEELHOUSE XJ BODY 23 125 SPECIFICATIONS Continued ...
Page 2013: ...ROOF BOWS 23 126 BODY XJ SPECIFICATIONS Continued ...
Page 2023: ......
Page 2071: ......