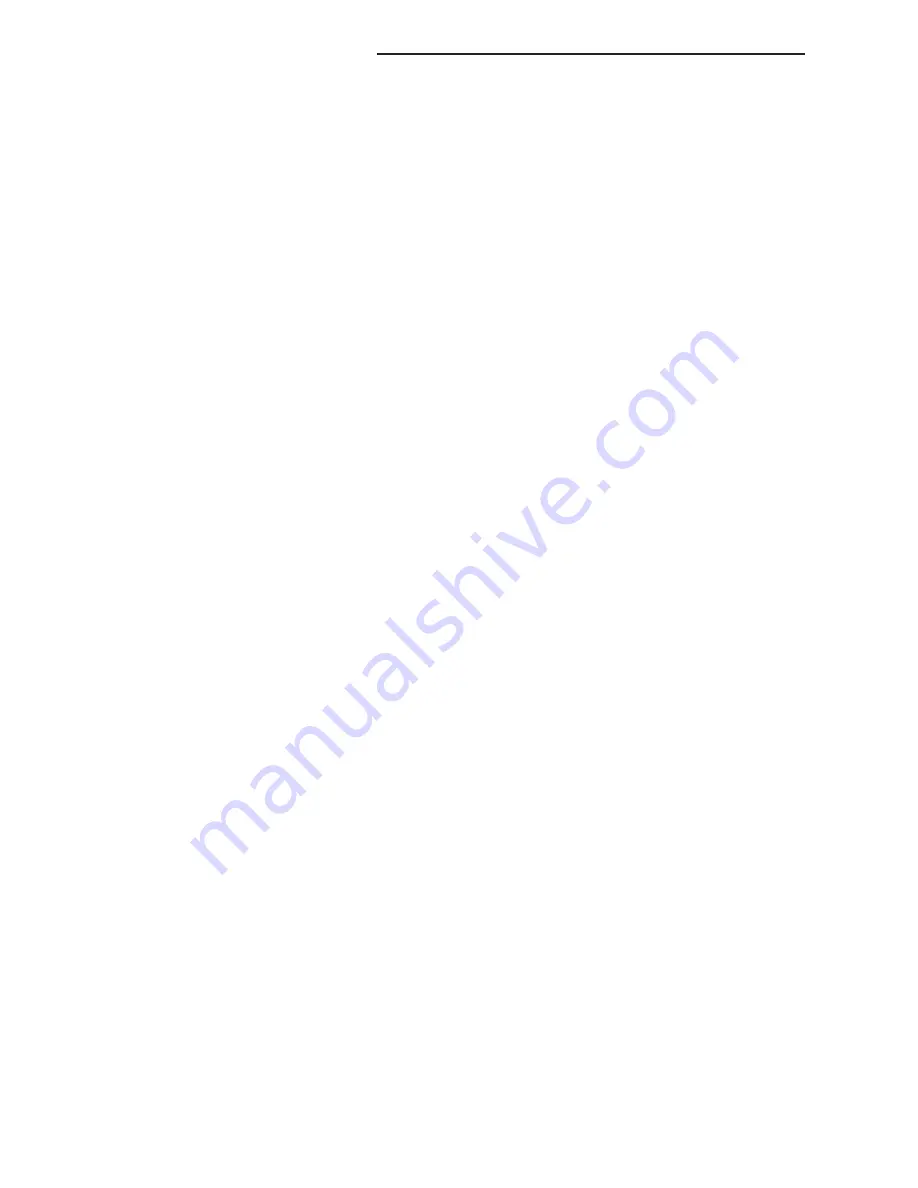
CAUTION:
•
Liquid refrigerant is corrosive to metal sur-
faces. Follow the operating instructions supplied
with the service equipment being used.
•
Never
add
R-12
to
a
refrigerant
system
designed to use R-134a. Damage to the system will
result.
•
R-12 refrigerant oil must not be mixed with
R-134a refrigerant oil. They are not compatible.
•
Do not use R-12 equipment or parts on the
R-134a system. Damage to the system will result.
•
Do not overcharge the refrigerant system. This
will cause excessive compressor head pressure
and can cause noise and system failure.
•
Recover the refrigerant before opening any fit-
ting or connection. Open the fittings with caution,
even after the system has been discharged. Never
open or loosen a connection before recovering the
refrigerant.
•
Do not remove the secondary retention clip
from any spring-lock coupler connection while the
refrigerant system is under pressure. Recover the
refrigerant before removing the secondary retention
clip. Open the fittings with caution, even after the
system has been discharged. Never open or loosen
a connection before recovering the refrigerant.
•
The refrigerant system must always be evacu-
ated before charging.
•
Do not open the refrigerant system or uncap a
replacement component until you are ready to ser-
vice the system. This will prevent contamination in
the system.
•
Before disconnecting a component, clean the
outside of the fittings thoroughly to prevent con-
tamination from entering the refrigerant system.
•
Immediately after disconnecting a component
from the refrigerant system, seal the open fittings
with a cap or plug.
•
Before connecting an open refrigerant fitting,
always install a new seal or gasket. Coat the fitting
and seal with clean refrigerant oil before connect-
ing.
•
Do not remove the sealing caps from a replace-
ment component until it is to be installed.
•
When installing a refrigerant line, avoid sharp
bends that may restrict refrigerant flow. Position the
refrigerant lines away from exhaust system compo-
nents or any sharp edges, which may damage the
line.
•
Tighten refrigerant fittings only to the specified
torque. The aluminum fittings used in the refriger-
ant system will not tolerate overtightening.
•
When disconnecting a refrigerant fitting, use a
wrench on both halves of the fitting. This will pre-
vent twisting of the refrigerant lines or tubes.
•
Refrigerant oil will absorb moisture from the
atmosphere if left uncapped. Do not open a con-
tainer of refrigerant oil until you are ready to use it.
Replace the cap on the oil container immediately
after using. Store refrigerant oil only in a clean, air-
tight, and moisture-free container.
•
Keep service tools and the work area clean.
Contamination of the refrigerant system through
careless work habits must be avoided.
COOLING SYSTEM REQUIREMENTS
To maintain the performance level of the heating-
air conditioning system, the engine cooling system
must be properly maintained. The use of a bug
screen is not recommended. Any obstructions in front
of the radiator or condenser will reduce the perfor-
mance of the air conditioning and engine cooling sys-
tems.
The engine cooling system includes the heater core
and the heater hoses. Refer to Group 7 - Cooling Sys-
tem for more information before the opening of, or
attempting any service to the engine cooling system.
REFRIGERANT HOSES/LINES/TUBES
PRECAUTIONS
Kinks or sharp bends in the refrigerant plumbing
will reduce the capacity of the entire system. High
pressures are produced in the system when it is oper-
ating. Extreme care must be exercised to make sure
that all refrigerant system connections are pressure
tight.
A good rule for the flexible hose refrigerant lines is
to keep the radius of all bends at least ten times the
diameter of the hose. Sharp bends will reduce the
flow of refrigerant. The flexible hose lines should be
routed so they are at least 80 millimeters (3 inches)
from the exhaust manifold. It is a good practice to
inspect all flexible refrigerant system hose lines at
least once a year to make sure they are in good con-
dition and properly routed.
There are two types of refrigerant fittings:
•
All fittings with O-rings need to be coated with
refrigerant oil before installation. Use only O-rings
that are the correct size and approved for use with
R-134a refrigerant. Failure to do so may result in a
leak.
•
Unified plumbing connections with gaskets can-
not be serviced with O-rings. The gaskets are not
reusable and new gaskets do not require lubrication
before installing.
Using the proper tools when making a refrigerant
plumbing connection is very important. Improper
tools or improper use of the tools can damage the
refrigerant fittings. Always use two wrenches when
loosening or tightening tube fittings. Use one wrench
24 - 2
HEATING AND AIR CONDITIONING
XJ
DESCRIPTION AND OPERATION (Continued)
Summary of Contents for 200 Cherokee
Page 5: ...FASTENER IDENTIFICATION 4 INTRODUCTION XJ DESCRIPTION AND OPERATION Continued ...
Page 6: ...FASTENER STRENGTH XJ INTRODUCTION 5 DESCRIPTION AND OPERATION Continued ...
Page 8: ...METRIC CONVERSION CHART XJ INTRODUCTION 7 DESCRIPTION AND OPERATION Continued ...
Page 9: ...TORQUE SPECIFICATIONS 8 INTRODUCTION XJ DESCRIPTION AND OPERATION Continued ...
Page 47: ......
Page 107: ...Fig 105 Gear Tooth Contact Patterns 3 60 TUBE 181 AND 186 FBI AXLE XJ ADJUSTMENTS Continued ...
Page 111: ...Installer D 144 Installer W 262 3 64 TUBE 181 AND 186 FBI AXLE XJ SPECIAL TOOLS Continued ...
Page 145: ...Fig 79 Gear Tooth Contact Patterns 3 98 194 RBI AXLE XJ ADJUSTMENTS Continued ...
Page 177: ...Fig 59 Gear Tooth Contact Patterns 3 130 8 1 4 REAR AXLE XJ ADJUSTMENTS Continued ...
Page 230: ...Fig 8 Clutch Components And Inspection XJ CLUTCH 6 5 DIAGNOSIS AND TESTING Continued ...
Page 241: ......
Page 357: ......
Page 367: ......
Page 449: ......
Page 451: ......
Page 475: ......
Page 484: ...SPECIAL TOOLS HEADLAMP ALIGNMENT Headlamp Aiming Kit C 4466 A XJ LAMPS 8L 9 ...
Page 507: ......
Page 537: ......
Page 551: ......
Page 571: ......
Page 577: ......
Page 583: ......
Page 613: ......
Page 615: ......
Page 631: ......
Page 669: ......
Page 707: ......
Page 735: ......
Page 783: ......
Page 789: ......
Page 805: ......
Page 823: ......
Page 827: ......
Page 851: ......
Page 863: ......
Page 867: ......
Page 893: ......
Page 921: ......
Page 925: ......
Page 931: ......
Page 937: ......
Page 1047: ......
Page 1072: ...Fig 16 2 5L Engine XJ 8W 90 CONNECTOR LOCATIONS 8W 90 25 DESCRIPTION AND OPERATION Continued ...
Page 1073: ...Fig 17 4 0L Engine 8W 90 26 8W 90 CONNECTOR LOCATIONS XJ DESCRIPTION AND OPERATION Continued ...
Page 1074: ...Fig 18 4 0L Engine XJ 8W 90 CONNECTOR LOCATIONS 8W 90 27 DESCRIPTION AND OPERATION Continued ...
Page 1087: ...Fig 31 Liftgate 8W 90 40 8W 90 CONNECTOR LOCATIONS XJ DESCRIPTION AND OPERATION Continued ...
Page 1099: ......
Page 1129: ......
Page 1249: ......
Page 1331: ...Fig 6 Frame Dimensions 13 8 FRAME AND BUMPERS XJ SPECIFICATIONS Continued ...
Page 1333: ......
Page 1335: ......
Page 1869: ......
Page 1875: ......
Page 1887: ......
Page 1912: ...Fig 3 Hood Components XJ BODY 23 25 REMOVAL AND INSTALLATION Continued ...
Page 1955: ...WELD LOCATIONS UPPER COWL 23 68 BODY XJ SPECIFICATIONS Continued ...
Page 1956: ...UPPER COWL XJ BODY 23 69 SPECIFICATIONS Continued ...
Page 1957: ...COWL 23 70 BODY XJ SPECIFICATIONS Continued ...
Page 1958: ...A PILLAR XJ BODY 23 71 SPECIFICATIONS Continued ...
Page 1959: ...A PILLAR 23 72 BODY XJ SPECIFICATIONS Continued ...
Page 1960: ...A PILLAR XJ BODY 23 73 SPECIFICATIONS Continued ...
Page 1961: ...A PILLAR 23 74 BODY XJ SPECIFICATIONS Continued ...
Page 1962: ...B PILLAR XJ BODY 23 75 SPECIFICATIONS Continued ...
Page 1963: ...D PILLAR 23 76 BODY XJ SPECIFICATIONS Continued ...
Page 1964: ...FUEL FILLER OPENING XJ BODY 23 77 SPECIFICATIONS Continued ...
Page 1965: ...CARGO AREA FLOOR PAN 23 78 BODY XJ SPECIFICATIONS Continued ...
Page 1966: ...ROOF AND D PILLAR XJ BODY 23 79 SPECIFICATIONS Continued ...
Page 1967: ...LIFTGATE OPENING 23 80 BODY XJ SPECIFICATIONS Continued ...
Page 1968: ...ROOF XJ BODY 23 81 SPECIFICATIONS Continued ...
Page 1969: ...ROOF 23 82 BODY XJ SPECIFICATIONS Continued ...
Page 1970: ...FRAME RAIL XJ BODY 23 83 SPECIFICATIONS Continued ...
Page 1971: ...FRAME RAIL 23 84 BODY XJ SPECIFICATIONS Continued ...
Page 1972: ...FRAME RAIL XJ BODY 23 85 SPECIFICATIONS Continued ...
Page 1973: ...FRAME RAIL 23 86 BODY XJ SPECIFICATIONS Continued ...
Page 1974: ...REINFORCEMENT XJ BODY 23 87 SPECIFICATIONS Continued ...
Page 1975: ...FRONT INNER FENDER 23 88 BODY XJ SPECIFICATIONS Continued ...
Page 1976: ...FRONT INNER FENDER AND RADIATOR CLOSURE PANEL XJ BODY 23 89 SPECIFICATIONS Continued ...
Page 1977: ...REINFORCEMENT 23 90 BODY XJ SPECIFICATIONS Continued ...
Page 1978: ...FRONT FENDER XJ BODY 23 91 SPECIFICATIONS Continued ...
Page 1979: ...BODY SIDE 23 92 BODY XJ SPECIFICATIONS Continued ...
Page 1980: ...REAR WHEELHOUSE XJ BODY 23 93 SPECIFICATIONS Continued ...
Page 1981: ...REAR INNER WHEELHOUSE 23 94 BODY XJ SPECIFICATIONS Continued ...
Page 1982: ...BODY SIDE XJ BODY 23 95 SPECIFICATIONS Continued ...
Page 1983: ...BODY SIDE 23 96 BODY XJ SPECIFICATIONS Continued ...
Page 1984: ...BODY SIDE XJ BODY 23 97 SPECIFICATIONS Continued ...
Page 1985: ...BODY SIDE 23 98 BODY XJ SPECIFICATIONS Continued ...
Page 1986: ...BODY SIDE XJ BODY 23 99 SPECIFICATIONS Continued ...
Page 1987: ...BODY SIDE 23 100 BODY XJ SPECIFICATIONS Continued ...
Page 1988: ...UNDERBODY XJ BODY 23 101 SPECIFICATIONS Continued ...
Page 1989: ...UNDERBODY 23 102 BODY XJ SPECIFICATIONS Continued ...
Page 1990: ...UNDERBODY XJ BODY 23 103 SPECIFICATIONS Continued ...
Page 1991: ...UNDERBODY 23 104 BODY XJ SPECIFICATIONS Continued ...
Page 1992: ...UNDERBODY XJ BODY 23 105 SPECIFICATIONS Continued ...
Page 1993: ...UNDERBODY 23 106 BODY XJ SPECIFICATIONS Continued ...
Page 1994: ...UNDERBODY XJ BODY 23 107 SPECIFICATIONS Continued ...
Page 1995: ...UNDERBODY 23 108 BODY XJ SPECIFICATIONS Continued ...
Page 1996: ...UNDERBODY XJ BODY 23 109 SPECIFICATIONS Continued ...
Page 1997: ...UNDERBODY 23 110 BODY XJ SPECIFICATIONS Continued ...
Page 1998: ...UNDERBODY XJ BODY 23 111 SPECIFICATIONS Continued ...
Page 1999: ...BODY SEALING LOCATIONS APPLICATION METHODS 23 112 BODY XJ SPECIFICATIONS Continued ...
Page 2000: ...COWL AND DASH PANEL XJ BODY 23 113 SPECIFICATIONS Continued ...
Page 2001: ...DASH PANEL AND FLOOR PAN 23 114 BODY XJ SPECIFICATIONS Continued ...
Page 2002: ...FLOOR PAN XJ BODY 23 115 SPECIFICATIONS Continued ...
Page 2003: ...REAR INNER WHEELHOUSE 23 116 BODY XJ SPECIFICATIONS Continued ...
Page 2004: ...FRONT INNER WHEELHOUSE XJ BODY 23 117 SPECIFICATIONS Continued ...
Page 2005: ...BODY SIDE 23 118 BODY XJ SPECIFICATIONS Continued ...
Page 2006: ...BODY SIDE XJ BODY 23 119 SPECIFICATIONS Continued ...
Page 2007: ...BODY SIDE 23 120 BODY XJ SPECIFICATIONS Continued ...
Page 2008: ...ROOF PANEL XJ BODY 23 121 SPECIFICATIONS Continued ...
Page 2009: ...FUEL FILLER HOUSING 23 122 BODY XJ SPECIFICATIONS Continued ...
Page 2010: ...LIFTGATE OPENING XJ BODY 23 123 SPECIFICATIONS Continued ...
Page 2011: ...STRUCTURAL ADHESIVE LOCATIONS LEFT QUARTER PANEL 23 124 BODY XJ SPECIFICATIONS Continued ...
Page 2012: ...REAR WHEELHOUSE XJ BODY 23 125 SPECIFICATIONS Continued ...
Page 2013: ...ROOF BOWS 23 126 BODY XJ SPECIFICATIONS Continued ...
Page 2023: ......
Page 2071: ......