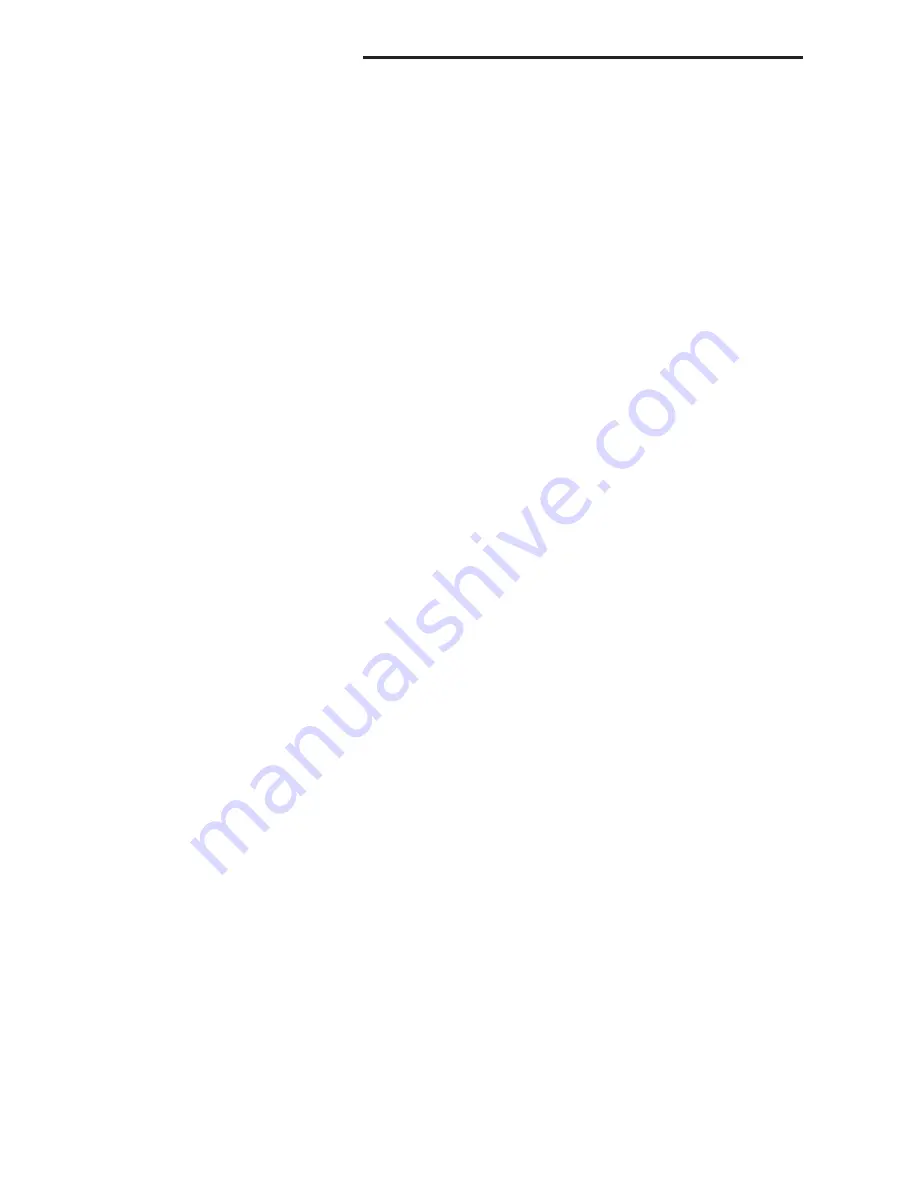
WASHER PUMP
The washer pumps and motors are mounted near
the bottom of the washer reservoir. A barbed nipple
on the pump housing passes through a rubber grom-
met seal installed in a hole near the bottom of the
reservoir. The washer pump is retained by an inter-
ference fit between the barbed pump nipple and the
grommet seal, which is a light press fit.
A permanently lubricated and sealed motor is cou-
pled to a rotor-type pump. Washer fluid is gravity-fed
from the reservoir to the pump. When the motor is
energized, the pump pressurizes the washer fluid
and forces it through the plumbing to the nozzles.
On vehicles with the optional rear wiper/washer
system, the front washer pump and motor is always
mounted in the lower hole of the reservoir. The
washer pump and motor unit cannot be repaired. If
faulty, the entire washer pump and motor unit must
be replaced.
WASHER FLUID LEVEL SENSOR
The washer fluid level sensor is mounted near the
front of the washer reservoir, above the two washer
pumps. A barbed nipple on the sensor is press-fit into
a rubber grommet seal installed in a hole in the front
of the reservoir.
When the fluid level in the reservoir falls below
the pivoting float on the sensor, the float changes
position and closes the internal switch contacts of the
sensor. Refer to Group 8E - Instrument Panel Sys-
tems for diagnosis of the low washer fluid warning
lamp and circuit, including the sensor.
The washer fluid level sensor cannot be repaired. If
faulty or damaged, the sensor unit must be replaced.
WASHER NOZZLE AND PLUMBING
FRONT
Pressurized washer fluid is fed through a single
hose, attached to a barbed nipple on the front washer
pump. The hose is routed to a tee fitting located in
the cowl plenum area, beneath the cowl plenum cov-
er/grille panel. Hoses from the tee fitting are routed
to the two nozzles, which are riveted into openings in
the cowl plenum cover/grille panel below the wind-
shield.
The two fluidic washer nozzles are not adjustable.
The nozzles and hose fittings cannot be repaired and,
if faulty or damaged, they must be replaced.
REAR
Pressurized washer fluid is fed through a single
hose, attached to a barbed nipple on the rear washer
pump. The hose is routed from the front of the vehi-
cle to the liftgate with the body wire harness.
Located at the highest point of the supply hose
routing, beneath the liftgate opening upper header
garnish moulding, the hose connects to a check valve.
The check valve prevents washer fluid drain-back or
siphoning from occurring. From the check valve,
another single hose is routed through a grommet to
the liftgate, where it is connected to a nipple that
protrudes from the inside of the rear wiper motor
output shaft bezel.
The washer fluid passes through the bezel nipple
to the outside of the liftgate. There a single hose is
connected to a nipple on the outside of the rear wiper
motor output shaft bezel. The hose is routed through
a plastic trough-like guard snapped to the underside
of the rear wiper arm. The hose is then attached to
the single rear washer nozzle. The nozzle snaps into
place on the rear wiper arm.
The rear washer nozzle cannot be adjusted. The
nozzle, bezel, check valve, and hose fittings cannot be
repaired and, if faulty or damaged, they must be
replaced.
DIAGNOSIS AND TESTING
WIPER SYSTEM
FRONT
For circuit descriptions and diagrams, refer to
8W-53 - Wipers in Group 8W - Wiring Diagrams.
WARNING: ON VEHICLES EQUIPPED WITH AIR-
BAGS,
REFER
TO
GROUP
8M
-
PASSIVE
RESTRAINT SYSTEMS BEFORE ATTEMPTING ANY
STEERING
WHEEL,
STEERING
COLUMN,
OR
INSTRUMENT PANEL COMPONENT DIAGNOSIS OR
SERVICE. FAILURE TO TAKE THE PROPER PRE-
CAUTIONS COULD RESULT IN ACCIDENTAL AIR-
BAG DEPLOYMENT AND POSSIBLE PERSONAL
INJURY.
(1) Check the circuit breaker in the junction block.
If OK, go to Step 2. If not OK, replace the faulty cir-
cuit breaker.
(2) Disconnect and isolate the battery negative
cable. Unplug the windshield wiper switch wire har-
ness connector. Connect the battery negative cable.
Turn the ignition switch to the On position. Check
for battery voltage at the fused ignition switch out-
put (run/acc) circuit cavity of the wiper switch wire
harness connector. If OK, go to Step 3. If not OK,
repair the open circuit to the junction block as
required.
(3) If the problem being diagnosed involves only
the pulse wipe, wipe-after-wash, or intermittent wipe
modes, go to Step 4. If not, go to Step 5.
8K - 4
WIPER AND WASHER SYSTEMS
XJ
DESCRIPTION AND OPERATION (Continued)
Summary of Contents for 200 Cherokee
Page 5: ...FASTENER IDENTIFICATION 4 INTRODUCTION XJ DESCRIPTION AND OPERATION Continued ...
Page 6: ...FASTENER STRENGTH XJ INTRODUCTION 5 DESCRIPTION AND OPERATION Continued ...
Page 8: ...METRIC CONVERSION CHART XJ INTRODUCTION 7 DESCRIPTION AND OPERATION Continued ...
Page 9: ...TORQUE SPECIFICATIONS 8 INTRODUCTION XJ DESCRIPTION AND OPERATION Continued ...
Page 47: ......
Page 107: ...Fig 105 Gear Tooth Contact Patterns 3 60 TUBE 181 AND 186 FBI AXLE XJ ADJUSTMENTS Continued ...
Page 111: ...Installer D 144 Installer W 262 3 64 TUBE 181 AND 186 FBI AXLE XJ SPECIAL TOOLS Continued ...
Page 145: ...Fig 79 Gear Tooth Contact Patterns 3 98 194 RBI AXLE XJ ADJUSTMENTS Continued ...
Page 177: ...Fig 59 Gear Tooth Contact Patterns 3 130 8 1 4 REAR AXLE XJ ADJUSTMENTS Continued ...
Page 230: ...Fig 8 Clutch Components And Inspection XJ CLUTCH 6 5 DIAGNOSIS AND TESTING Continued ...
Page 241: ......
Page 357: ......
Page 367: ......
Page 449: ......
Page 451: ......
Page 475: ......
Page 484: ...SPECIAL TOOLS HEADLAMP ALIGNMENT Headlamp Aiming Kit C 4466 A XJ LAMPS 8L 9 ...
Page 507: ......
Page 537: ......
Page 551: ......
Page 571: ......
Page 577: ......
Page 583: ......
Page 613: ......
Page 615: ......
Page 631: ......
Page 669: ......
Page 707: ......
Page 735: ......
Page 783: ......
Page 789: ......
Page 805: ......
Page 823: ......
Page 827: ......
Page 851: ......
Page 863: ......
Page 867: ......
Page 893: ......
Page 921: ......
Page 925: ......
Page 931: ......
Page 937: ......
Page 1047: ......
Page 1072: ...Fig 16 2 5L Engine XJ 8W 90 CONNECTOR LOCATIONS 8W 90 25 DESCRIPTION AND OPERATION Continued ...
Page 1073: ...Fig 17 4 0L Engine 8W 90 26 8W 90 CONNECTOR LOCATIONS XJ DESCRIPTION AND OPERATION Continued ...
Page 1074: ...Fig 18 4 0L Engine XJ 8W 90 CONNECTOR LOCATIONS 8W 90 27 DESCRIPTION AND OPERATION Continued ...
Page 1087: ...Fig 31 Liftgate 8W 90 40 8W 90 CONNECTOR LOCATIONS XJ DESCRIPTION AND OPERATION Continued ...
Page 1099: ......
Page 1129: ......
Page 1249: ......
Page 1331: ...Fig 6 Frame Dimensions 13 8 FRAME AND BUMPERS XJ SPECIFICATIONS Continued ...
Page 1333: ......
Page 1335: ......
Page 1869: ......
Page 1875: ......
Page 1887: ......
Page 1912: ...Fig 3 Hood Components XJ BODY 23 25 REMOVAL AND INSTALLATION Continued ...
Page 1955: ...WELD LOCATIONS UPPER COWL 23 68 BODY XJ SPECIFICATIONS Continued ...
Page 1956: ...UPPER COWL XJ BODY 23 69 SPECIFICATIONS Continued ...
Page 1957: ...COWL 23 70 BODY XJ SPECIFICATIONS Continued ...
Page 1958: ...A PILLAR XJ BODY 23 71 SPECIFICATIONS Continued ...
Page 1959: ...A PILLAR 23 72 BODY XJ SPECIFICATIONS Continued ...
Page 1960: ...A PILLAR XJ BODY 23 73 SPECIFICATIONS Continued ...
Page 1961: ...A PILLAR 23 74 BODY XJ SPECIFICATIONS Continued ...
Page 1962: ...B PILLAR XJ BODY 23 75 SPECIFICATIONS Continued ...
Page 1963: ...D PILLAR 23 76 BODY XJ SPECIFICATIONS Continued ...
Page 1964: ...FUEL FILLER OPENING XJ BODY 23 77 SPECIFICATIONS Continued ...
Page 1965: ...CARGO AREA FLOOR PAN 23 78 BODY XJ SPECIFICATIONS Continued ...
Page 1966: ...ROOF AND D PILLAR XJ BODY 23 79 SPECIFICATIONS Continued ...
Page 1967: ...LIFTGATE OPENING 23 80 BODY XJ SPECIFICATIONS Continued ...
Page 1968: ...ROOF XJ BODY 23 81 SPECIFICATIONS Continued ...
Page 1969: ...ROOF 23 82 BODY XJ SPECIFICATIONS Continued ...
Page 1970: ...FRAME RAIL XJ BODY 23 83 SPECIFICATIONS Continued ...
Page 1971: ...FRAME RAIL 23 84 BODY XJ SPECIFICATIONS Continued ...
Page 1972: ...FRAME RAIL XJ BODY 23 85 SPECIFICATIONS Continued ...
Page 1973: ...FRAME RAIL 23 86 BODY XJ SPECIFICATIONS Continued ...
Page 1974: ...REINFORCEMENT XJ BODY 23 87 SPECIFICATIONS Continued ...
Page 1975: ...FRONT INNER FENDER 23 88 BODY XJ SPECIFICATIONS Continued ...
Page 1976: ...FRONT INNER FENDER AND RADIATOR CLOSURE PANEL XJ BODY 23 89 SPECIFICATIONS Continued ...
Page 1977: ...REINFORCEMENT 23 90 BODY XJ SPECIFICATIONS Continued ...
Page 1978: ...FRONT FENDER XJ BODY 23 91 SPECIFICATIONS Continued ...
Page 1979: ...BODY SIDE 23 92 BODY XJ SPECIFICATIONS Continued ...
Page 1980: ...REAR WHEELHOUSE XJ BODY 23 93 SPECIFICATIONS Continued ...
Page 1981: ...REAR INNER WHEELHOUSE 23 94 BODY XJ SPECIFICATIONS Continued ...
Page 1982: ...BODY SIDE XJ BODY 23 95 SPECIFICATIONS Continued ...
Page 1983: ...BODY SIDE 23 96 BODY XJ SPECIFICATIONS Continued ...
Page 1984: ...BODY SIDE XJ BODY 23 97 SPECIFICATIONS Continued ...
Page 1985: ...BODY SIDE 23 98 BODY XJ SPECIFICATIONS Continued ...
Page 1986: ...BODY SIDE XJ BODY 23 99 SPECIFICATIONS Continued ...
Page 1987: ...BODY SIDE 23 100 BODY XJ SPECIFICATIONS Continued ...
Page 1988: ...UNDERBODY XJ BODY 23 101 SPECIFICATIONS Continued ...
Page 1989: ...UNDERBODY 23 102 BODY XJ SPECIFICATIONS Continued ...
Page 1990: ...UNDERBODY XJ BODY 23 103 SPECIFICATIONS Continued ...
Page 1991: ...UNDERBODY 23 104 BODY XJ SPECIFICATIONS Continued ...
Page 1992: ...UNDERBODY XJ BODY 23 105 SPECIFICATIONS Continued ...
Page 1993: ...UNDERBODY 23 106 BODY XJ SPECIFICATIONS Continued ...
Page 1994: ...UNDERBODY XJ BODY 23 107 SPECIFICATIONS Continued ...
Page 1995: ...UNDERBODY 23 108 BODY XJ SPECIFICATIONS Continued ...
Page 1996: ...UNDERBODY XJ BODY 23 109 SPECIFICATIONS Continued ...
Page 1997: ...UNDERBODY 23 110 BODY XJ SPECIFICATIONS Continued ...
Page 1998: ...UNDERBODY XJ BODY 23 111 SPECIFICATIONS Continued ...
Page 1999: ...BODY SEALING LOCATIONS APPLICATION METHODS 23 112 BODY XJ SPECIFICATIONS Continued ...
Page 2000: ...COWL AND DASH PANEL XJ BODY 23 113 SPECIFICATIONS Continued ...
Page 2001: ...DASH PANEL AND FLOOR PAN 23 114 BODY XJ SPECIFICATIONS Continued ...
Page 2002: ...FLOOR PAN XJ BODY 23 115 SPECIFICATIONS Continued ...
Page 2003: ...REAR INNER WHEELHOUSE 23 116 BODY XJ SPECIFICATIONS Continued ...
Page 2004: ...FRONT INNER WHEELHOUSE XJ BODY 23 117 SPECIFICATIONS Continued ...
Page 2005: ...BODY SIDE 23 118 BODY XJ SPECIFICATIONS Continued ...
Page 2006: ...BODY SIDE XJ BODY 23 119 SPECIFICATIONS Continued ...
Page 2007: ...BODY SIDE 23 120 BODY XJ SPECIFICATIONS Continued ...
Page 2008: ...ROOF PANEL XJ BODY 23 121 SPECIFICATIONS Continued ...
Page 2009: ...FUEL FILLER HOUSING 23 122 BODY XJ SPECIFICATIONS Continued ...
Page 2010: ...LIFTGATE OPENING XJ BODY 23 123 SPECIFICATIONS Continued ...
Page 2011: ...STRUCTURAL ADHESIVE LOCATIONS LEFT QUARTER PANEL 23 124 BODY XJ SPECIFICATIONS Continued ...
Page 2012: ...REAR WHEELHOUSE XJ BODY 23 125 SPECIFICATIONS Continued ...
Page 2013: ...ROOF BOWS 23 126 BODY XJ SPECIFICATIONS Continued ...
Page 2023: ......
Page 2071: ......