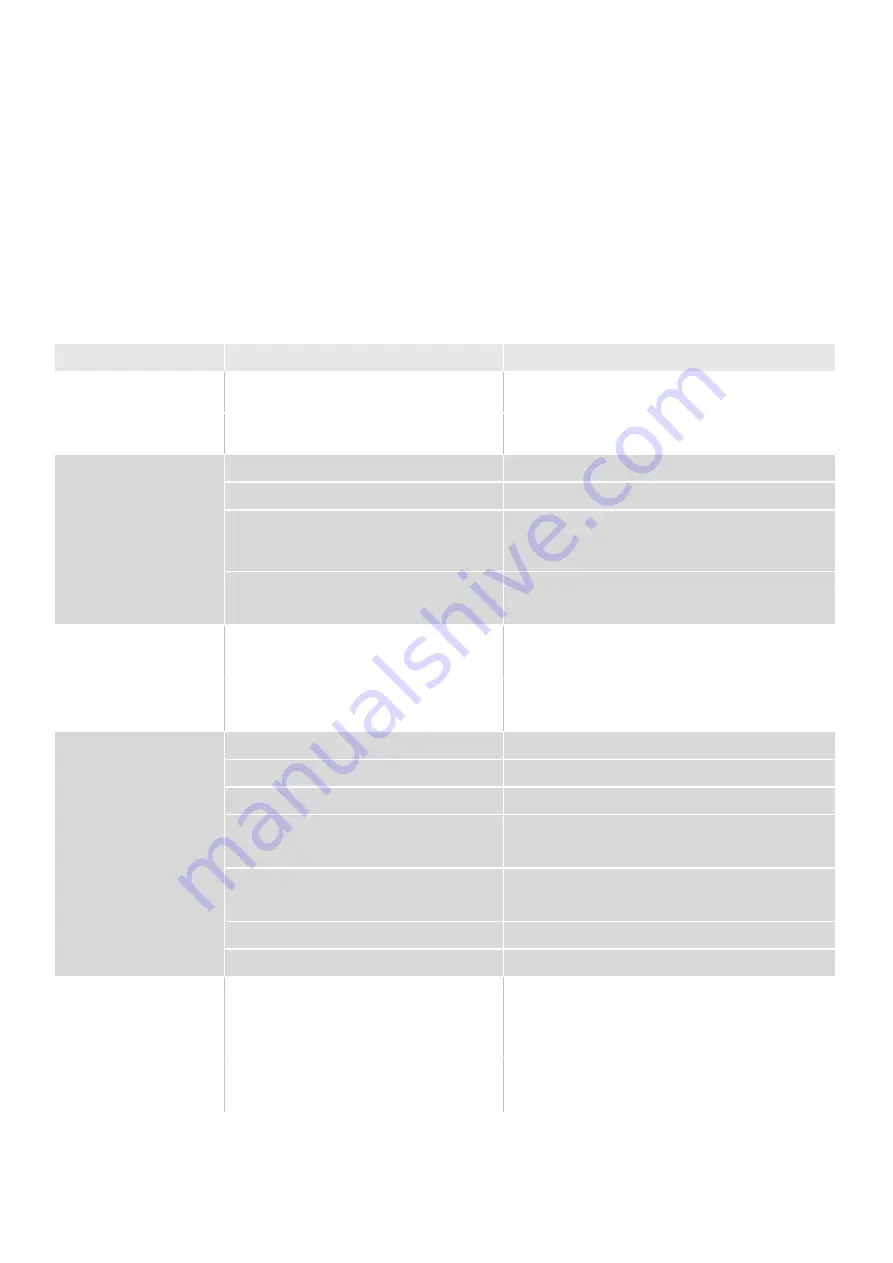
71
TIG TORCH TROUBLESHOOTING
TIG welding defects and prevention methods
The TIG torch used for lift TIG welding comprises of several items which ensure current flow and arc
shielding from the atmosphere.
Regular maintenance of the welding torch is one of the most important measures to ensure its normal
operation and extend lifespan.
In order to ensure normal maintenance, the wearing parts of the torch should have spares, including the
electrode holder, nozzle, sealing ring, insulating washer, etc.
Common faults of the welding torch include overheating, gas leakage, water leakage, poor gas protection,
electric leakage, nozzle burn out, and cracking. The causes of these faults and troubleshooting methods
are as shown in the following table:
Symptom
Reasons
Troubleshooting
The welding torch is
overheating
The welding torch capacity is too small
Replace with a welding torch with large
capacity
The collet fails to clamp the tungsten
electrode
Replace the collet or back cap
Gas leakage
The sealing ring is worn
Replace the sealing ring
The gas connection thread is loose
Tighten it
The gas inlet pipe joint is damaged or
not fastened
Cut off the damaged joint, reconnect and
tighten the replaced gas inlet pipe or wrap up
the damaged area
The gas inlet pipe has been damaged
by heat or aging
Replace the gas inlet pipe
Operator receiving a
shock from the torch
The torch head is wet due to leakage
or other reasons
Find the cause of water leakage, and fully dry
the torch head
The torch head is damaged or the live
metal part is exposed
Replace the torch head or wrap the exposed
electrified metal part with adhesive tape
Poor gas flow or
porosity in the weld
The welding torch is leaking
Locate the leakage
The nozzle diameter is too small
Replace with a nozzle of larger diameter
The nozzle is damaged or cracked
Replace with a new nozzle
The gas circuit in the welding torch is
blocked
Blow the circuit with compressed air to clear
the blockage
The gas screen has been damaged or
lost during disassembly and assembly
Replace with a new gas screen
The argon gas is impure
Replace with standard argon gas
The gas flow is too large or small
Adjust the gas flow properly
Arc started between
the collet/collet
holder or the tungsten
electrode/torch head
The collet and tungsten electrode have
poor contact, or arc is started when
the tungsten electrode contacts the
base metal
Replace the collet or repair
The collet and welding torch have poor
contact
Connect the collet and welding torch properly
Summary of Contents for EVO 2.0 EM-160C
Page 1: ...1...
Page 75: ...75 UKCA Declaration of Conformity...
Page 76: ...76 EC DECLARATION OF CONFORMITY...
Page 78: ...78 SCHEMATIC...
Page 82: ...82...