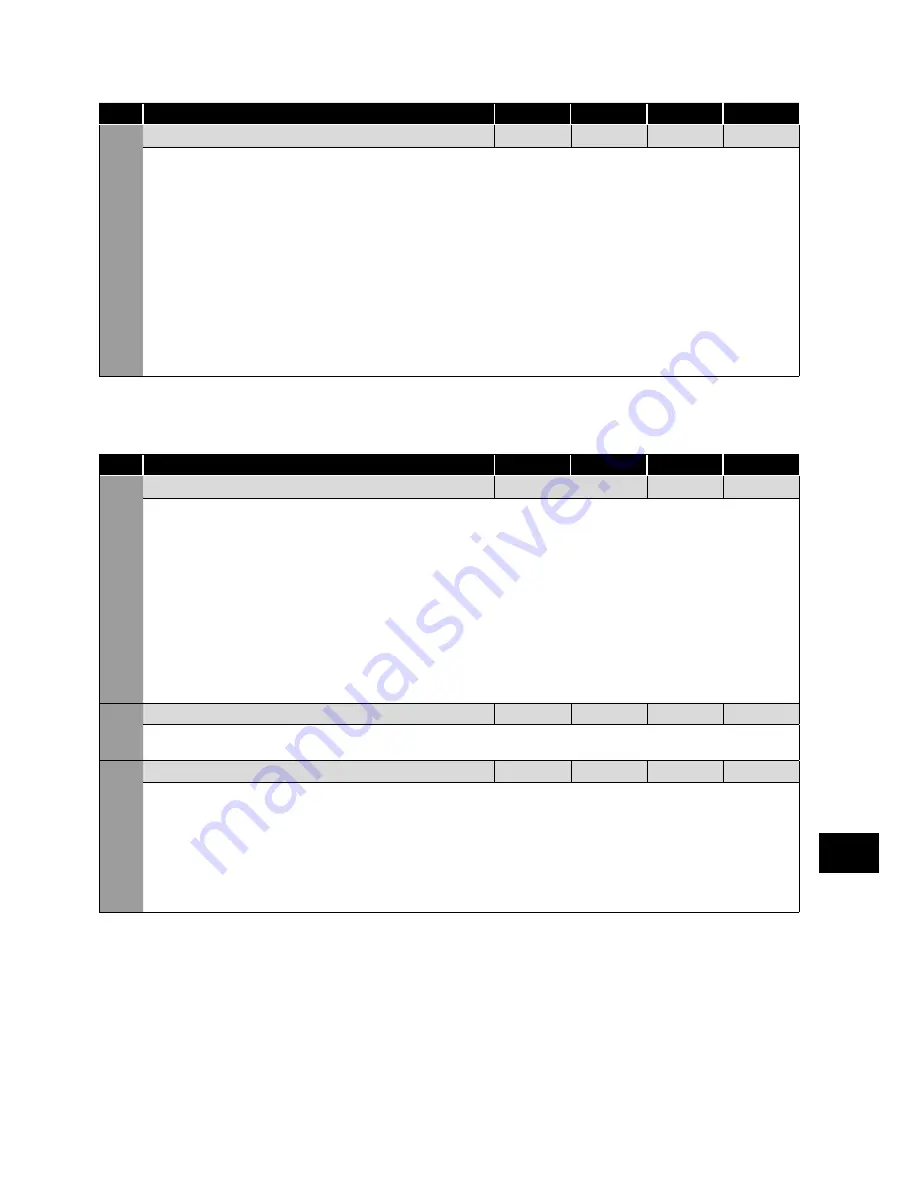
Version 1.00
| Optidrive ODE-3 IP66 Outdoor Rated User Guide |
25
www.invertekdrives.com
6.3.2 Control Modes
Par.
Description
Minimum
Maximum
Default
Units
P-12
Primary Command Source
0
9
0
-
0: Terminal Control.
The drive responds directly to signals applied to the control terminals.
1: Uni-directional Keypad Control.
The drive can be controlled in the forward direction only using the internal keypad, or an
external remote Keypad.
2: Bi-directional Keypad Control.
The drive can be controlled in the forward and reverse directions using the internal keypad, or an
external remote Keypad. Pressing the keypad START button toggles between forward and reverse.
3: Modbus Network Control.
Control via Modbus RTU (RS485) using the internal Accel / Decel ramps.
4: Modbus Network Control.
Control via Modbus RTU (RS485) interface with Accel / Decel ramps updated via Modbus.
5: PI Control.
User PI control with external feedback signal.
6: PI Analog Summation Control.
PI control with external feedback signal and summation with analog input 1.
7: CAN Control.
Control via CAN (RS485) using the internal Accel / Decel ramps.
8: CAN Control.
Control via CAN (RS485) interface with Accel / Decel ramps updated via CAN.
9: Slave Mode.
Control via a connected Invertek drive in Master Mode. Slave drive address must be > 1.
NOTE
When P-12 = 1, 2, 3, 4, 7, 8 or 9, an enable signal must still be provided at the control terminals, digital input 1.
6.3.3 Input and Output Functions
Analog Inputs - Format (relevant parameters)
Par.
Description
Minimum
Maximum
Default
Units
P-16
Analog Input 1 Signal Format
See Below
U0-10
-
= Uni-polar 0 to 10 Volt Signal. The drive will remain at minimum speed (P-02) if the analog reference after scaling and offset
are applied is =<0.0%. 100% signal means the output frequency / speed will be the value set in P-01.
= Uni-polar 0 to 10 Volt Signal, bi-directional operation. The drive will operate the motor in the reverse
direction of rotation if the analog reference after scaling and offset are applied is <0.0%. E.g. for bidirectional control from a 0 – 10 volt
signal, set P-35 = 200.0%, P-39 = 50.0%.
= 0 to 20mA Signal.
= 4 to 20mA Signal, the Optidrive will trip and show the fault code
if the signal level falls below 3mA.
= 4 to 20mA Signal, the Optidrive will run at Preset Speed 1 (P-20 if the signal level falls below 3mA.
= 20 to 4mA Signal, the Optidrive will trip and show the fault code
if the signal level falls below 3mA.
= 20 to 4mA Signal, the Optidrive will run at Preset Speed 1 (P-20 if the signal level falls below 3mA.
= 10 to 0 Volt Signal (Uni-polar). The drive will operate at Maximum Frequency / Speed if the analog
reference after scaling and offset are applied is =<0.0%.
P-17
Maximum Effective Switching Frequency
4
32
8
kHz
Sets maximum effective switching frequency of the drive. If “rEd” is displayed when the parameter is viewed, the switching frequency has
been reduced to the level in P00-32 due to excessive drive heatsink temperature.
P-47
Analog Input 2 Signal Format
-
-
-
U0-10
= 0 to 10 Volt Signal.
= 0 to 20mA Signal.
= 4 to 20mA Signal, the Optidrive will trip and show the fault code
if the signal level falls below 3mA.
= 4 to 20mA Signal, the Optidrive will run at Preset Speed 1 (P-20) if the signal level falls below 3mA.
= 20 to 4mA Signal, the Optidrive will trip and show the fault code
if the signal level falls below 3mA.
= 20 to 4mA Signal, the Optidrive will run at Preset Speed 1 (P-20) if the signal level falls below 3mA.
= Use for motor thermistor measurement, valid with any setting of P-15 that has Input 3 as E-Trip. Trip level: 1.5kΩ, reset 1kΩ.
Parameters
6