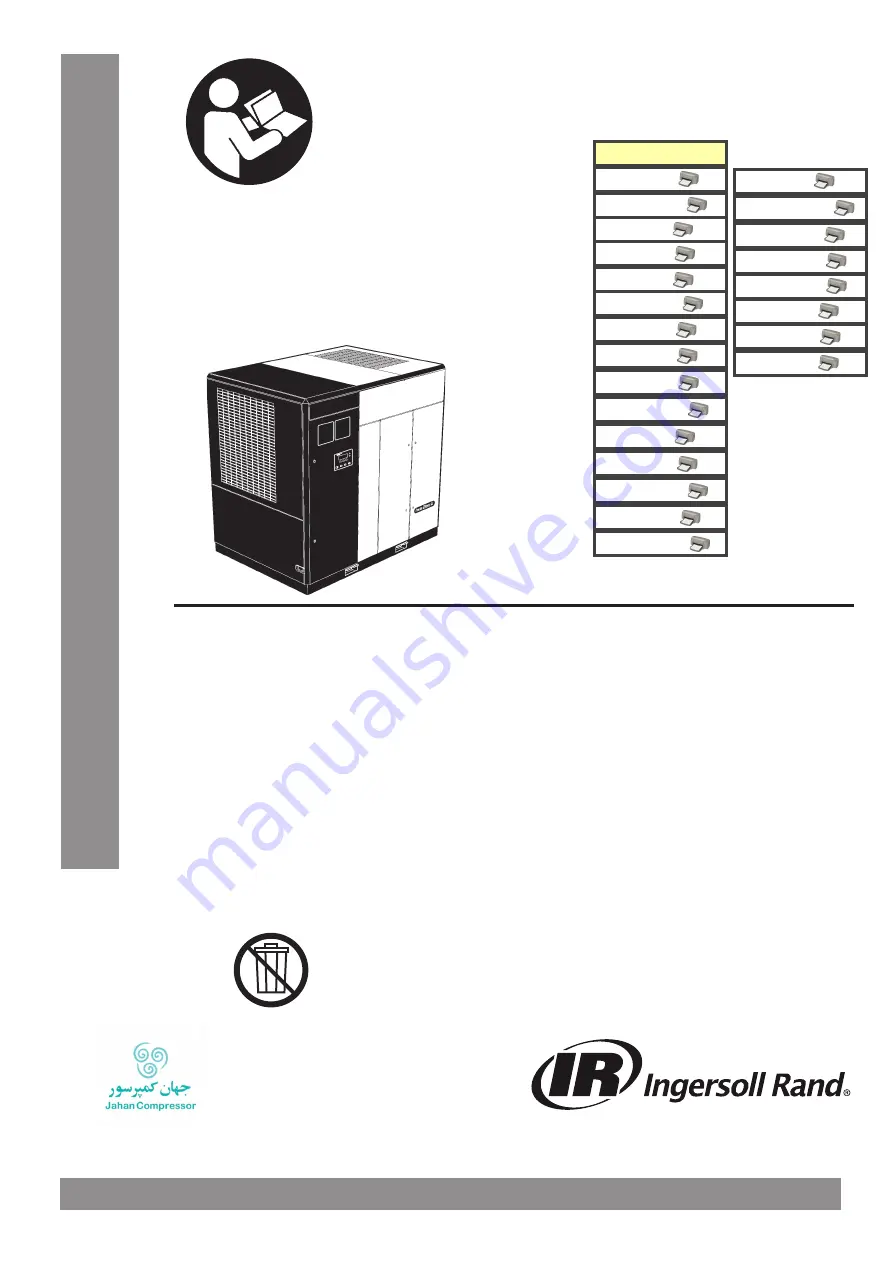
54719091
Revision K
November 2013
Save These Instructions
IRN37-160K - CC, IRN50-200H-CC,
IRN75-160K-2S, IRN100-200H-2S,
R190-225NE
Operation and Maintenance Manual
111213.14.59
ENGLISH
CZECH
DANISH
BULGARIAN
PRINT LANGUAGE
DUTCH
FINNISH
ESTONIAN
FRENCH
GERMAN
HUNGARIAN
ITALIAN
LATVIAN
LITHUANIAN
MALTESE
NORWEGIAN
POLISH
PORTUGUESE
ROMANIAN
SLOVAKIAN
SLOVENIAN
SPANISH
SWEDISH
TURKISH
Summary of Contents for IRN100-200H-2S
Page 101: ...111213 14 59 ...
Page 102: ...ingersollrandproducts com 2013 Ingersoll Rand 111213 14 59 ...