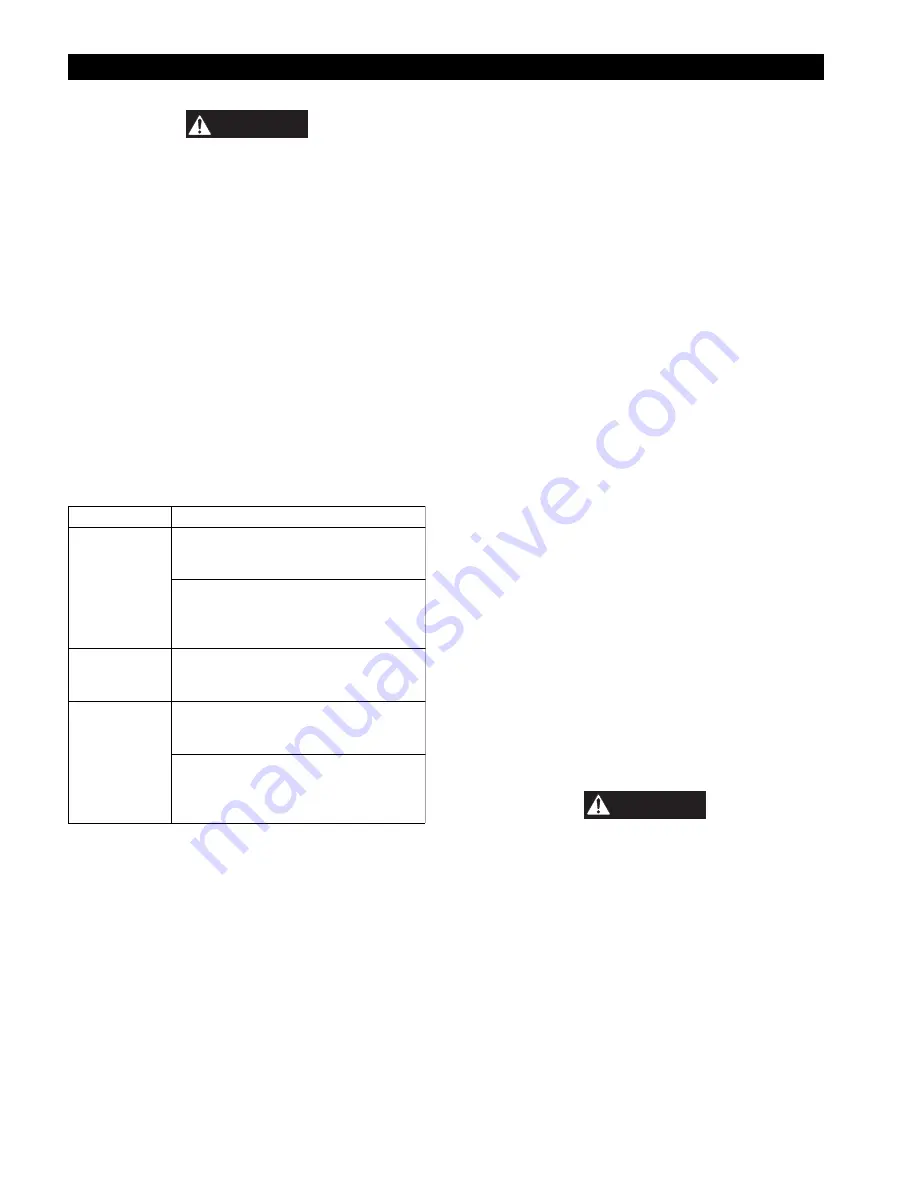
18
WARNING
• Never perform maintenance on the hoist while it is
supporting a load.
• Before performing maintenance, tag controls:
DANGER - DO NOT OPERATE -
EQUIPMENT BEING REPAIRED.
• Only allow personnel instructed in service and repair of this
hoist to perform maintenance.
• After performing any maintenance on the hoist,
dynamically test hoist to 100% of its rated capacity, in
accordance with ASME B30.16 standards, before returning
hoist to service. Testing to more than 100% of rated capacity
may be required to comply with standards and regulations
set forth in areas outside of the USA.
• Shut off air system and depressurize air lines before
performing any maintenance.
Maintenance Intervals
The maintenance interval chart is based on intermittent
operation of the hoist eight hours each day, five days per week,
in an environment relatively free of dust, moisture and corrosive
fumes. If the hoist is operated almost continuously or more than
eight hours each day, more frequent maintenance should be
performed.
INTERVAL
MAINTENANCE CHECK
Start of each shift
(Operator or
Maintenance
Personnel)
Make a thorough visual inspection of the
hoist for damage. Do not operate the hoist if
damaged.
Operate the hoist in both directions. Hoist
must operate smoothly without sticking,
binding or abnormal noises. Check the
operation of the brake.
Semiannually
(Maintenance
Personnel)
Inspect the brake. Clean or replace parts as
required. Adjust brake as necessary.
Yearly
(Maintenance
Personnel)
Inspect the hoist gearing, shafts and bearings
for wear and damage. Repair or replace as
necessary.
Check all the supporting members, including
the suspension, fasteners, nuts, sheaves and
rigging, etc. for indications of damage or
wear. Repair or replace as required.
General Maintenance Instructions
All maintenance work performed on the hoist must be recorded
with the date in the inspection report.
Proper use, inspections and maintenance increase the life and
usefulness of your Ingersoll-Rand equipment. During assembly,
lubricate gears, nuts, capscrews and all machined threads with
applicable lubricants. Use of antiseize compound and/or thread
lubricant on capscrew and nut threaded areas prevents corrosion
and allows for ease of disassembly of components.
It is recommended that all maintenance work on the hoist be
performed on a bench in a clean, dust free work area. During the
process of disassembling the hoist, observe the following:
1.
Turn off air system and depressurize air lines before
performing any maintenance. Disconnect air line from
hoist.
2.
Never disassemble the hoist any further than is necessary to
accomplish the needed repair. A good part can be damaged
during the course of disassembly.
3.
Never use excessive force when removing parts. Tapping
gently around the perimeter of a cover or housing with a
soft hammer, for example, is sufficient to break the seal.
4.
Do not heat a part with a flame to free it for removal, unless
the part being heated is already worn or damaged beyond
repair and no additional damage will occur to other parts.
In general, the hoist is designed to permit easy disassembly and
assembly. The use of heat or excessive force should not be
necessary.
5.
Keep the work area clean to prevent dirt and other foreign
matter from getting into bearings and other moving parts.
6.
All seals, gaskets and ‘O’ rings should be discarded once
they have been removed. New seals, gaskets and ‘O’ rings
should be used when assembling the hoist.
7.
When grasping a part in a vise, always use leather or
copper covered vise jaws to protect the surface of the part
and help prevent distortion. This is particularly true of
threaded members, machined surfaces and housings.
8.
Do not remove any part which is press fit in or on a
subassembly unless the removal of the part is necessary for
repairs or replacement.
9.
To avoid damaging bearings during hoist assembly or
disassembly always tap or press on the bearing inner race
for shaft fit bearings or the outer race for bore fit bearings.
10. If repair work can only be conducted above body height,
suitable working platforms or ladders should be made
available.
Load Chain Care
Keep the chain well lubricated as instructed in the
“LUBRICATION” section. Never operate a hoist when the load
chain does not flow freely and smoothly into and out of the
chain wheel(s), or when it makes noises indicative of binding or
other malfunctions.
If the chain is visibly damaged replace the chain and examine
the chain wheel and chain guard. Install a new chain wheel if the
old one is visibly worn. Install a new guard if the old one is
broken or distorted.
Refer to “INSPECTION” section for information on load chain
inspection.
CAUTION
• The full extent of load chain wear cannot be determined by
visual inspection. At any indication of load chain wear
inspect chain and chain wheel. Refer to “INSPECTION”
section.
The standard chain provided with this hoist is case hardened to a
depth of 0.010 to 0.012 inch (0.25 to 0.35 mm). When the outer
hardened case layer is worn through, additional wear will
progress rapidly and the strength of the chain will be
considerably reduced.
Additionally, the chain will no longer fit the pockets in the hoist
chain wheel properly causing the chain wheel to wear rapidly.
This will greatly increasing the chance of hoist malfunction and
chain breakage.
The hoist chain wheel is designed to outlast several chain
replacement cycles if the chain is replaced as recommended.
MAINTENANCE
Summary of Contents for HL1000K
Page 33: ...33 HOIST PARTS SECTION GUIDE ...
Page 34: ...34 HOIST HOUSING ASSEMBLY PARTS DRAWING ...
Page 36: ...36 HOIST VALVE CHEST ASSEMBLY PARTS DRAWING ...
Page 38: ...38 HOIST GEARING ASSEMBLY PARTS DRAWING ...
Page 40: ...40 HOIST BRAKE ASSEMBLY PARTS DRAWING ...
Page 44: ...44 HL1000K HL1000KR AND HL1500K HOOK ASSEMBLY PARTS DRAWING ...
Page 46: ...46 HL2000K AND HL3000K HOOK ASSEMBLY PARTS DRAWING ...
Page 48: ...48 HL4500K HOOK ASSEMBLY PARTS DRAWING ...
Page 50: ...50 HL6000K HOOK ASSEMBLY PARTS DRAWING ...
Page 52: ...52 PENDANT ASSEMBLY PARTS DRAWING ...
Page 54: ...54 FABRIC CHAIN CONTAINER ASSEMBLY PARTS DRAWING ...
Page 56: ...56 METAL CHAIN CONTAINER ASSEMBLY PARTS DRAWING ...