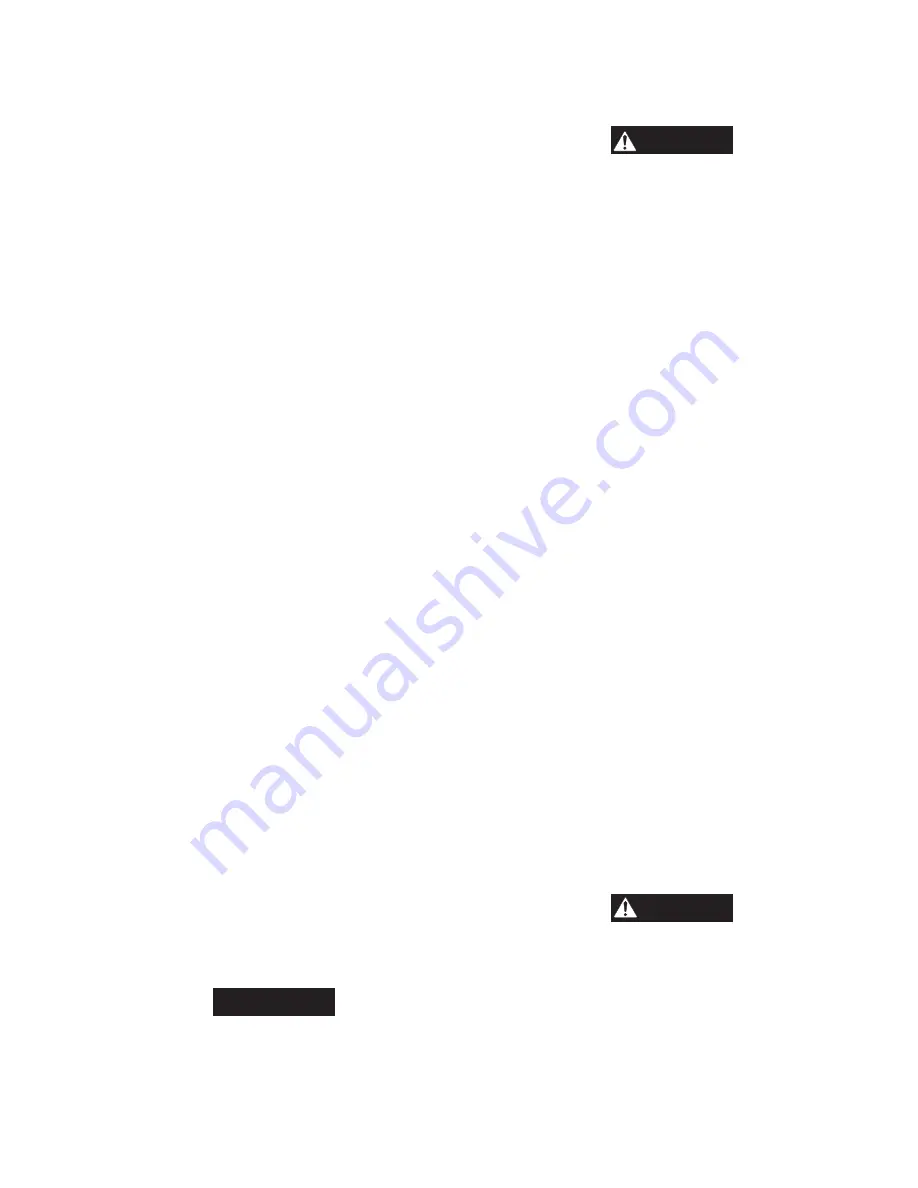
29
13. Place a housing gasket (3) on the motor end of the hoist
and install the valve chest plate (28) and screws (30).
Check that motor shaft (38) turns freely by hand without
sticking or binding.
14. Note the matchmarks ‘•’ on the ring gear (52) and on the
three planet gears (57). The planet frame assembly must be
inserted into the hoist such that the pinion gear (72)
internal splines align with the motor shaft (38) splines.
Also, the matchmarks ‘•’ on the planet gears must align
with the matchmarks ‘•’ on the ring gear.
15. Place the gear case gasket (66) on the end of the housing
with the gasket hole aligned with the air port.
16. If removed, install the fixed ring gear (67) and ring gear
pins (68) in the gear case cover.
17. Install the gear case assembly with gasket on the hoist
aligning the ring gear roll pins and brake port. Install the
four bolts and lockwashers.
18. Install the brake driver (73), brake seal (75), brake seal
retainer (74), and brake driver retainer screw (76). Apply a
small amount of silicone sealant to ‘O’ ring. The brake
driver retainer screw is a self-locking type screw that
should be replaced anytime the hoist is disassembled.
Torque the screw to 50 in lb (5.65 Nm).
19. Check that the brake driver turns freely by hand. If the
brake driver does not turn without restriction in both
directions the hoist must be inspected to determine the
cause of sticking or binding before further assembly.
20. If removed, assemble the upper suspension. On hook units,
inspect the hook and hook latch as described in the
“INSPECTION” section. Assemble the latch to the hook.
Lubricate the thrust bearing (106).
For HL1000K to HL3000K Hoists:
Assemble the hook (102), thrust bearing (106), thrust
washers (107), hook nut (104) and top yoke (101). Be
sure to install the roll pin (105) to lock the hook nut
on the hook. Mount the top yoke assembly or the lug
mount kit to the hoist using lubricated capscrews and
locking tabs under the capscrews. Torque the
capscrews to 75 - 125 ft lb (100 - 170 Nm). Bend the
locking tabs over the capscrews flats to secure.
For HL4500K and HL6000K Hoists:
Lubricate the thrust bearing (131). Assemble the hook
(127), thrust bearing, hook nut (129) and upper
suspension housing (101). Be sure to install the hook
pin (130) to lock the hook nut on the hook. Mount the
top yoke assembly or the lug mount kit to the hoist
using lubricated capscrews and locking tabs under
the capscrews. Torque the capscrews to 75 - 125 ft lb
(100 - 170 Nm). Bend the locking tabs over the
capscrew flats to secure.
21. Place the throttle shaft spring (37) over the hub of the
throttle lever (35) with the bent leg of the spring on the
outer side of the throttle lever.
22. Hold the throttle lever in the housing recess beneath the
pocket wheel with the bent ends of the lever toward the
valve chest end of the hoist and the legs of the throttle shaft
spring engaging a rib on the bottom of the chain guide.
Insert the throttle shaft (32), round end first, through the
valve chest plate, housing and throttle lever. Install a thrust
washer (36A) against the hub of the throttle lever. Install a
thrust washer (36A) against the throttle shaft spring. Install
the throttle lever retaining pin (36).
NOTICE
• On hoist models HL4500K and HL6000K the throttle lever
(35) may require adjustment to provide adequate clearance
with the upper suspension block. Minor modifications to the
throttle lever are acceptable to establish throttle lever
clearance.
23. Stand the hoist upright on the brake end. Place the valve
chest gasket (25) on the valve chest plate, making certain
that the small flapper is properly positioned in the recess
between the two ports.
WARNING
• If the valve chest gasket (25) is installed incorrectly, the
small flapper will not be in the recess between the two ports.
The brake will not release and may cause damage to the
hoist.
24. Center the two round rubber discs in corresponding
recesses in the valve chest plate.
25. Place the assembled valve chest (6) on the valve chest
gasket. Secure using the valve chest screws (26) and (27).
26. Install hoist load chain as described in the ‘Initial Chain
Installation’ section.
27. Reposition hoist with brake end up. Place a brake plate (78)
followed by a brake disc (79), brake plate (78), brake disc
(79), and two brake plates (78) over the brake driver (73),
aligning the notches in the brake plates with the bolt holes
in the gear case cover (69).
28. Reposition hoist with brake end up. Install the assembled
brake spring and piston housing (80), making sure the ‘O’
ring (77) is installed at the air port. Install the four
shoulder bolts (89) and lockwashers (90).
29. Place the limit actuator (33) on the square end of the
throttle shaft, and install the limit actuator retaining pin
(34).
30. For new style hoists with second letter of the serial
number other than A through G or with second and third
letters of the serial number other than HA, HB or HC,
install the two pendant links (183) between the limit
actuator and the valve shafts.
For old style hoists with pendant control with second
letter of the serial number A through G or with second and
third letters of the serial number HA, HB or HC, install a
pendant link (183) between the limit actuator and the long
piston rod.
For old style hoists with pull chain control with second
letter of the serial number A through G or with second and
third letters of the serial number HA, HB or HC, no
pendant links are required.
31. Apply a thin film of ‘O’ ring lubricant to the swivel inlet
seals (24A). Install seals on inlet stud (24) grooves.
32. Carefully push the inlet stud into the inlet body (23). Take
care to prevent cutting seals.
33. Apply a thin film of ‘O’ ring lubricant to the swivel inlet
gasket (24B). Install the gasket on the inlet stud.
34. Thread the inlet assembly into the top of the valve chest
and tighten.
Pendant Installation
Refer to Dwg. TPA0882-3.
CAUTION
• Disconnect the hoist from the air supply before performing
maintenance on this hoist.
When installing a pendant assembly on HLK Hoists, a crimping
tool (Part No. ML50K-930AT or a Nicopress
®
Tool with
Groove Size G) must be used to install the clamping sleeve
(176) on the ends of the strain relief cable (175).
Summary of Contents for HL1000K
Page 33: ...33 HOIST PARTS SECTION GUIDE ...
Page 34: ...34 HOIST HOUSING ASSEMBLY PARTS DRAWING ...
Page 36: ...36 HOIST VALVE CHEST ASSEMBLY PARTS DRAWING ...
Page 38: ...38 HOIST GEARING ASSEMBLY PARTS DRAWING ...
Page 40: ...40 HOIST BRAKE ASSEMBLY PARTS DRAWING ...
Page 44: ...44 HL1000K HL1000KR AND HL1500K HOOK ASSEMBLY PARTS DRAWING ...
Page 46: ...46 HL2000K AND HL3000K HOOK ASSEMBLY PARTS DRAWING ...
Page 48: ...48 HL4500K HOOK ASSEMBLY PARTS DRAWING ...
Page 50: ...50 HL6000K HOOK ASSEMBLY PARTS DRAWING ...
Page 52: ...52 PENDANT ASSEMBLY PARTS DRAWING ...
Page 54: ...54 FABRIC CHAIN CONTAINER ASSEMBLY PARTS DRAWING ...
Page 56: ...56 METAL CHAIN CONTAINER ASSEMBLY PARTS DRAWING ...