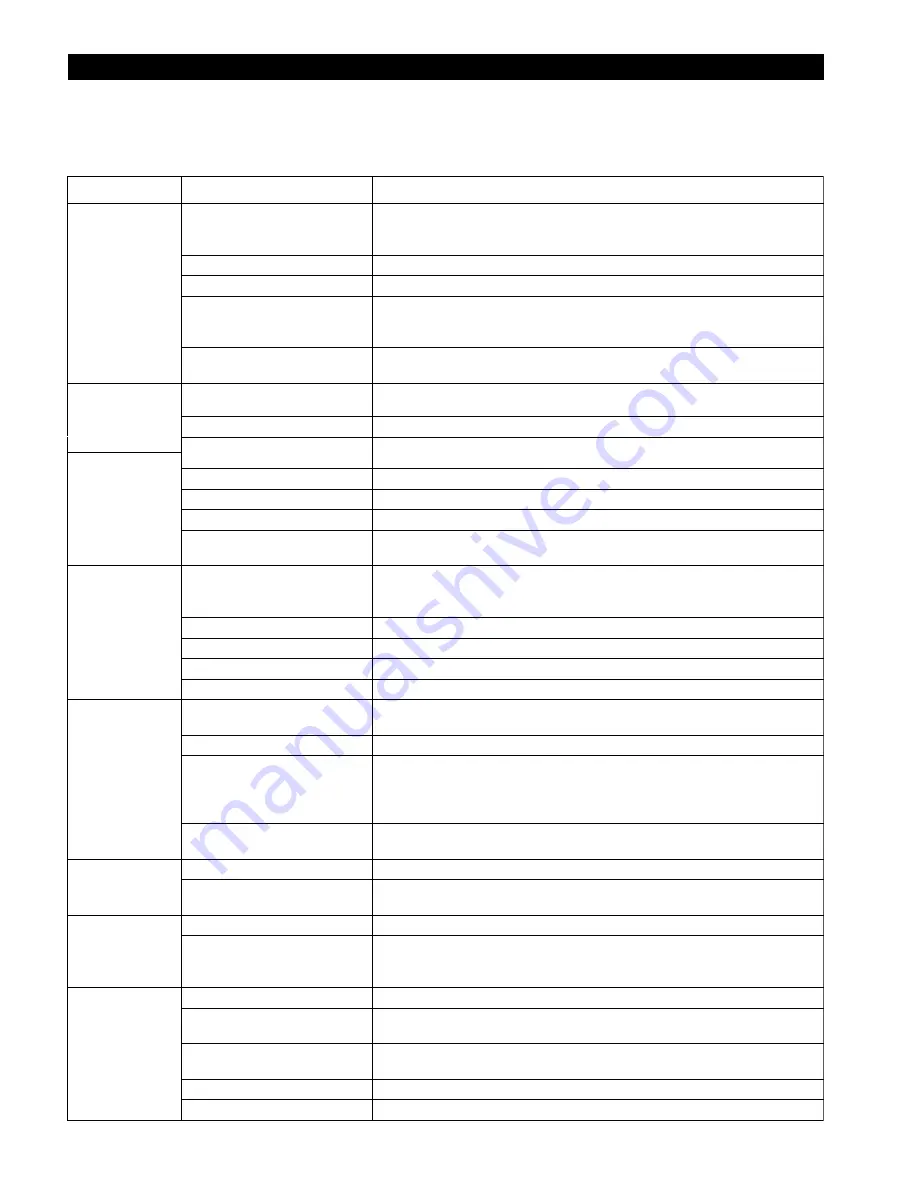
16
TROUBLESHOOTING
This section provides basic troubleshooting information. Specific causes to problems are best identified by thorough inspections
performed by personnel instructed in safety, operation and maintenance of this equipment. The chart below provides a brief guide to
common hoist symptoms, probable causes, and remedies.
SYMPTOM
CAUSE
REMEDY
Hoist will not
operate.
No air supply to hoist, or too little
flow or pressure.
Check air supply line connections and hoses. Check supply air at hoist motor
inlet. A minimum of 70 scfm (1.96 cu. m/m) air flow at 90 psig (6.3 bar/630 kPa)
at hoist motor inlet is required to provide rated performance.
Hoist is overloaded.
Reduce load to within rated capacity.
Motor is damaged.
Disassemble, inspect and replace parts. Refer to “MAINTENANCE” section.
Pendant malfunction.
Check pendant throttle lever for free movement. Check air pressure at pendant.
Minimum operating pressure in pendant line must be 55 psig (3.8 bar/380 kPa).
Check lubricator oil level. Fill if low.
Brake not releasing.
Check brake release circuit and pressure. Minimum operating pressure at brake
inlet must be 55 psig (3.8 bar/380 kPa).
Load continues to
move when hoist is
stopped (UP
direction).
Valve or throttle lever sticking.
Check pendant throttle lever for free movement. Lubricate or repair as required.
Dump valves not releasing.
Check pendant hose dump valves.
Pendant lever sticking.
Check pendant throttle lever for free movement.
Load continues to
move when hoist is
stopped (DOWN
direction).
Dump valves not releasing.
Check pendant hose dump valves.
Hoist is overloaded.
Reduce load to within rated capacity.
Valve or throttle lever sticking.
Check pendant throttle lever for free movement.
Brake is slipping.
Check brake springs and brake disc linings for wear. Refer to “MAINTENANCE”
section.
Hoist does not lift
load.
No air supply to hoist, or too little
flow or pressure.
Check air supply line connections and hoses. Check supply air at hoist motor
inlet. A minimum of 70 scfm (1.96 cu. m/m) air flow at 90 psig (6.3 bar/630 kPa)
at hoist motor inlet is required to provide rated performance.
Hoist is overloaded.
Reduce load to within rated capacity.
Main air travel is restricted.
Check throttle lever and linkage for free, unobstructed movement.
Exhaust restricted.
Inspect vents and replace mufflers. Refer to “MAINTENANCE” section.
Motor is damaged.
Disassemble, inspect and replace parts. Refer to “MAINTENANCE” section.
Reduced speed
and/or capacity.
Inlet stud (24) screen plugged,
restricting air flow.
Replace old style inlet stud with screen with new style (without screen), or
remove screen.
Lubricator oil level low.
Fill lubricator.
No air supply to hoist, or too little
flow or pressure.
Check air supply line connections and hoses. Check supply air at hoist motor
inlet. A minimum of 70 scfm (1.96 cu. m/m) air flow at 90 psig (6.3 bar/630 kPa)
at hoist motor inlet is required to provide rated performance. Check pendant
control adjustment as described in the “INSTALLATION” section.
Bleed screws out of adjustment.
Adjust bleed screws as described in ‘Bleed Screw Adjustment’ procedure in
“INSTALLATION” section.
Hoist operates in
LOWER direction
but will not LIFT.
Hoist is overloaded.
Reduce load to within rated capacity.
Pendant malfunction.
Check pendant throttle lever for free movement. Check air pressure at pendant.
Minimum operating pressure in pendant line must be 55 psig (3.8 bar/380 kPa).
Hoist operates in
LIFT direction but
will not LOWER.
Brake piston seals leaking.
Install new seals. Refer to “MAINTENANCE” section.
No air supply to hoist, or too little
flow or pressure.
Check air supply line connections and hoses. Check supply air at hoist motor
inlet. A minimum of 70 scfm (1.96 cu. m/m) air flow at 90 psig (6.3 bar/630 kPa)
at hoist motor inlet is required to provide rated performance.
Load chain jumps
on sheave or makes
a “snapping”
sound.
Dirty or lack of oil on load chain. Clean and lubricate load chain. Refer to “LUBRICATION” section.
Worn or rusted load chain.
Inspect load chain. Refer to “INSPECTION” section. Clean and lubricate load
chain. Refer to “LUBRICATION” section.
Worn load sheave or incorrectly
reeved load chain.
Check load chain is correctly reeved. Disassemble, inspect and replace worn
parts. Refer to “MAINTENANCE” section.
Capsized hook.
Correct as described in “MAINTENANCE” section.
Hoist not in-line with load.
Align hoist with load. Do not side pull or “yard”.
Summary of Contents for HL1000K
Page 33: ...33 HOIST PARTS SECTION GUIDE ...
Page 34: ...34 HOIST HOUSING ASSEMBLY PARTS DRAWING ...
Page 36: ...36 HOIST VALVE CHEST ASSEMBLY PARTS DRAWING ...
Page 38: ...38 HOIST GEARING ASSEMBLY PARTS DRAWING ...
Page 40: ...40 HOIST BRAKE ASSEMBLY PARTS DRAWING ...
Page 44: ...44 HL1000K HL1000KR AND HL1500K HOOK ASSEMBLY PARTS DRAWING ...
Page 46: ...46 HL2000K AND HL3000K HOOK ASSEMBLY PARTS DRAWING ...
Page 48: ...48 HL4500K HOOK ASSEMBLY PARTS DRAWING ...
Page 50: ...50 HL6000K HOOK ASSEMBLY PARTS DRAWING ...
Page 52: ...52 PENDANT ASSEMBLY PARTS DRAWING ...
Page 54: ...54 FABRIC CHAIN CONTAINER ASSEMBLY PARTS DRAWING ...
Page 56: ...56 METAL CHAIN CONTAINER ASSEMBLY PARTS DRAWING ...