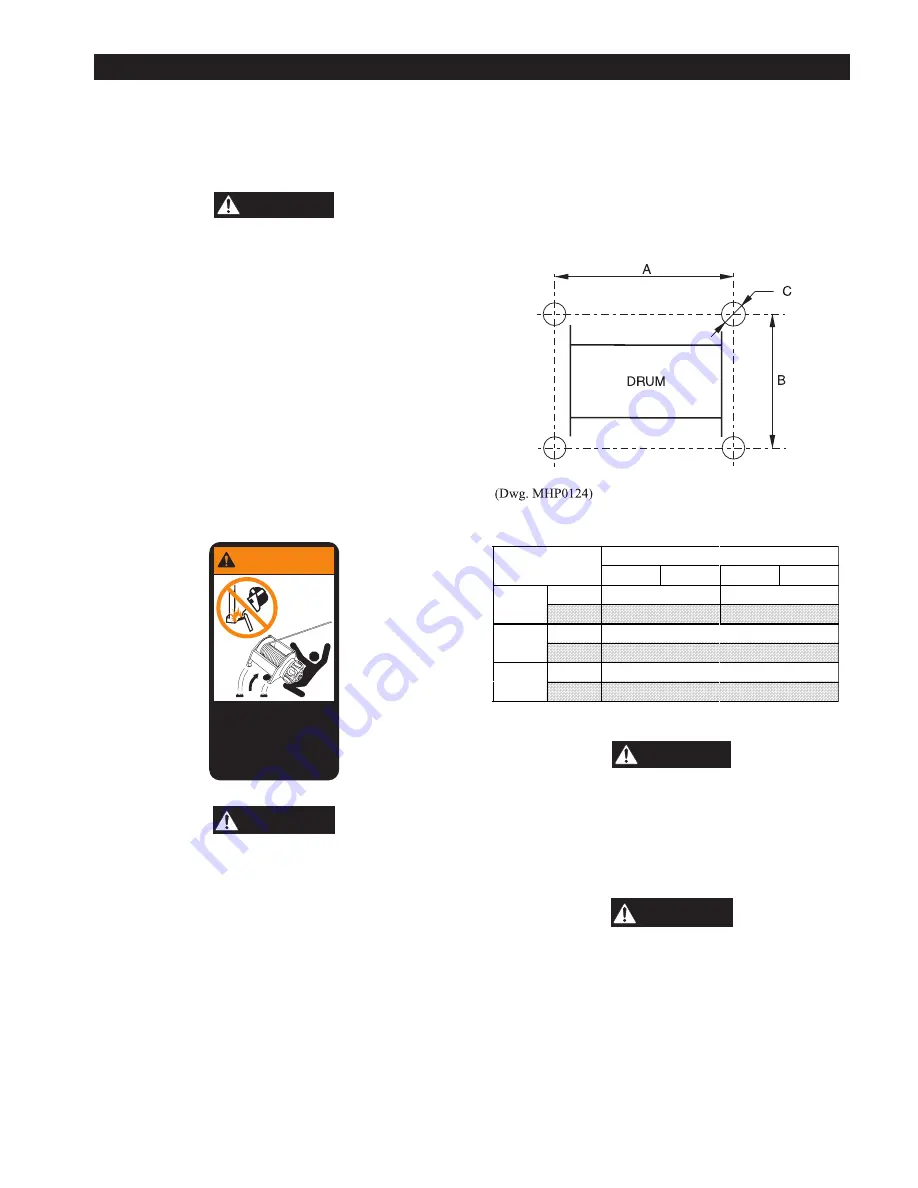
7
INSTALLATION
Prior to installing the winch, carefully inspect it for possible
shipping damage. Winches are supplied fully lubricated from the
factory. Check oil levels and adjust as necessary before
operating winch. Refer to "LUBRICATION" section for
recommended oils.
CAUTION
• Owners and users are advised to examine specific, local or
other regulations, including American National Standards
Institute and/or OSHA Regulations which may apply to a
particular type of use of this product before installing or
putting winch to use.
Mounting
Refer to Dwg. MHP0124 and Table 1.
Care must be taken when moving, positioning or mounting the
winch. Ensure that the winch, when lifted, will be properly
balanced. Determine the weight of the winch by referring to the
"SPECIFICATIONS" section. Lift the winch 3 to 4 inches (75 to
100 mm) off the ground. Verify winch is balanced and secure
before continuing lift. Mount the winch so the axis of the drum
is horizontal and that the motor vent cap is not more than 15° off
top vertical center. If the winch is to be mounted in an inverted
position, the motor case must be rotated to position the vent cap
at the top and adequate clearance must be provided for control
valve operation. The breather (8) and drain plug (21) on the disc
brake must be swapped.
WARNING
Welded mountings
can fail.
Can cause severe
injury or death.
Do not weld, braze or
solder to winch.
71270813
WARNING
• Winch frame material is not suitable for welding. FA5A
winches must only be mounted by bolting to a suitable
foundation. Do not attempt to mount the winch by welding to
a foundation structure.
1.
The winch mounting surface must be flat and of sufficient
strength to handle the rated load plus the weight of the
winch and attached equipment. An inadequate foundation
may cause distortion or twisting of the winch uprights and
side rails resulting in winch damage.
2.
Make sure the mounting surface is flat to within 1/32 inch
(0.8 mm). Shim if necessary.
3.
Mounting bolts must be 3/4 inch-NC (18 mm) Grade 8 or
better. Use self-locking nuts or nuts with lockwashers.
4.
Tighten mounting bolts evenly and torque to 380 ft lbs.
(515 Nm) for dry thread fasteners. If the fasteners are
plated, lubricated or a thread locking compound is used,
torque to 280 ft lbs. (380 Nm).
5.
Maintain a fleet angle between the lead sheave and winch
of no more than 1-1/2°. The lead sheave must be on a
center line with the drum and, for every inch (25 mm) of
drum length, be at least 1.6 feet (0.5 metre) from the drum.
Refer to Dwg. MHP0498.
6.
Do not weld to any part of the winch.
Table 1: Mounting Bolt Hole Dimensions
Dimension
Drum Length (inches)
12
15
24
27
“A”
in.
17.89
29.89
mm
455
760
“B”
in.
22
mm
559
“C”
in.
0.81
mm
21
Wire Rope
CAUTION
• Maintain at least 3 tight wraps of wire rope on the drum at
all times. Refer to Dwg. MHP0498.
Standard and Open Frame (Face) Winch
Install the winch such that the wire rope, when at the take-off
angle limits shown in Dwg. MHP1142, does not contact the
mounting surface.
DANGER
• Exceeding the wire rope take-off angles will cause the wire
rope to come into contact with the winch frame supports
resulting in damage to the wire rope and winch.
Summary of Contents for force5 FA5A-LAK1
Page 34: ...34 WINCH ASSEMBLY PARTS DRAWING ...
Page 36: ...36 MOTOR ASSEMBLY PARTS DRAWING ...
Page 38: ...38 DISC BRAKE ASSEMBLY PARTS DRAWING ...
Page 40: ...40 DRUM BAND BRAKE ASSEMBLY PARTS DRAWING ...
Page 42: ...42 LEVER OPERATED CONTROL VALVE ASSEMBLY PARTS DRAWING ...
Page 44: ...44 PENDANT OPERATED PILOT CONTROL VALVE ASSEMBLY PARTS DRAWING ...
Page 48: ...48 SHUTTLE VALVE ASSEMBLY PARTS DRAWING ...
Page 50: ...50 EMERGENCY STOP AND OVERLOAD ASSEMBLY PARTS DRAWING ...
Page 52: ...52 OPEN FRAME FACE WINCH ASSEMBLY PARTS DRAWING ...
Page 57: ...57 WINCH LABEL TAG LOCATION AND PART NUMBER REFERENCE DRAWING ...