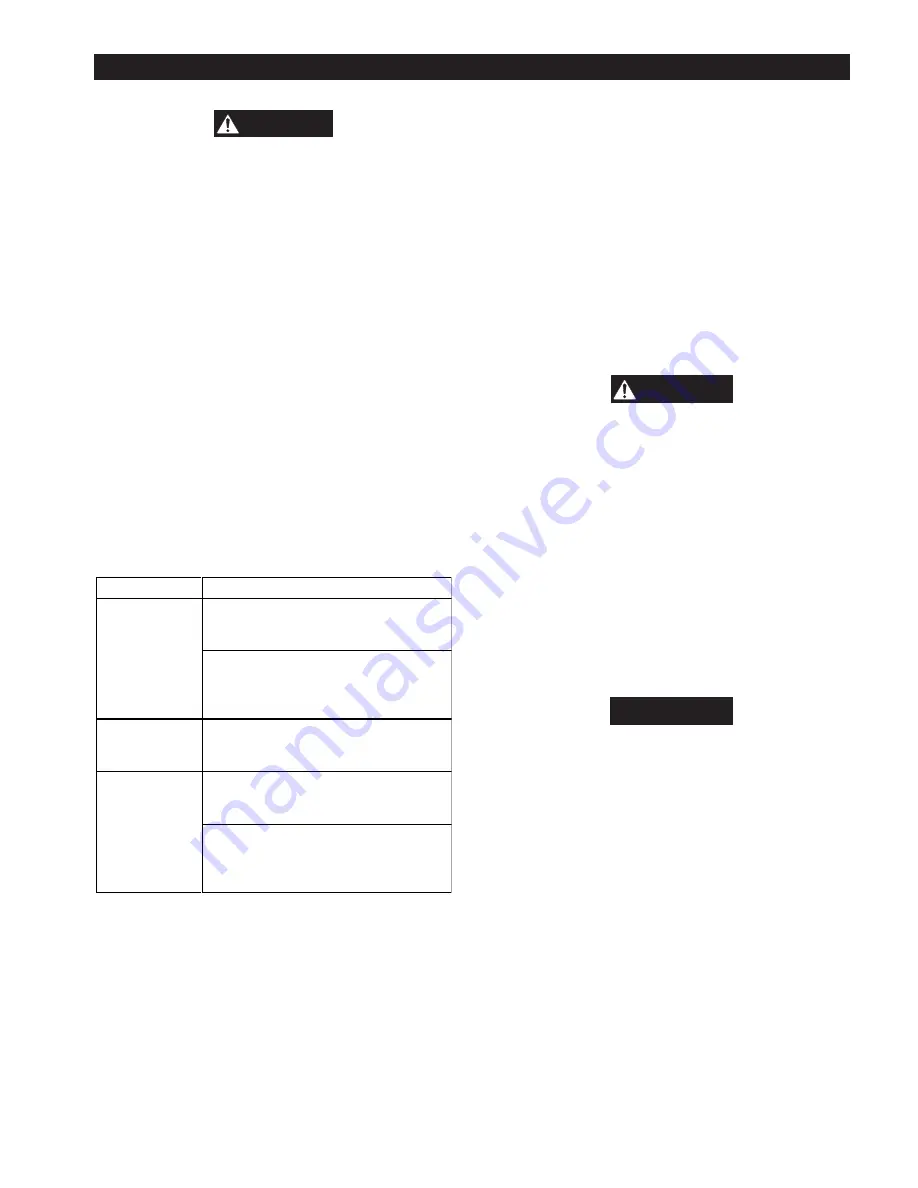
19
MAINTENANCE
WARNING
• Never perform maintenance on the winch while it is
supporting a load.
• Before performing maintenance, tag controls:
DANGER - DO NOT OPERATE -
EQUIPMENT BEING REPAIRED.
• Only allow personnel trained in safety and service on this
winch to perform maintenance.
• After performing any maintenance on the winch, test winch
to 125% of its rated line pull at mid drum before returning to
service. (Testing to more than 125% of rated line pull may be
required to comply with standards and regulations set forth
in areas outside the USA.)
• Turn off air system and depressurize air lines before
performing any maintenance.
Proper use, inspections and maintenance increase the life and
usefulness of your Ingersoll-Rand equipment. During assembly
lubricate gears, nuts, capscrews and all machined threads with
applicable lubricants. Use of antiseize compound and/or thread
lubricant on capscrew and nut threaded areas prevents corrosion
and allows for easy disassembly of components.
Maintenance Intervals
The Maintenance Interval chart below is based on intermittent
operation of equipment for eight hours each day, five days per
week. If equipment is in operation for more than eight hours a
day, or is operated in severe applications or environments, more
frequent maintenance should be performed.
INTERVAL
MAINTENANCE CHECK
Start of each shift
(Operator or
Maintenance
Personnel)
Make a thorough visual inspection of the
winch for damage. Do not operate the winch
if damaged.
Operate the winch at low RPM in both
directions. Winch must operate smoothly
without sticking, binding or abnormal noises.
Check the operation of the brake(s).
3 Months
(Maintenance
Personnel)
Inspect the drum brake friction linings.
Clean or replace parts as required. Adjust
drum brake as necessary.
Yearly
(Maintenance
Personnel)
Inspect the winch gearing, shafts and
bearings for wear and damage. Repair or
replace as necessary.
Check all the supporting members, including
the foundation, fasteners, nuts, sheaves and
rigging, etc. for indications of damage or
wear. Repair or replace as required.
Reduction Gear Assembly
It is recommend that the first oil change be done after
approximately 50 hours initial operation. Always inspect
removed oil for evidence of internal damage (metal shavings,
dirt, water, etc.).
Refer to the "LUBRICATION" section for recommended
lubricants.
Thermoplastic Coating
Thermoplastic coating is an extremely tough and durable coating
designed to take the toughest treatment without chipping or
peeling. Special steps must be taken to protect the coating when
parts are removed, replaced and if excessive environmental or
operational conditions have damaged the coating.
Cleaning Parts
The area to be coated must be clean and free from loose coating.
Remove any surface corrosion. To paint thermoplastic coated
parts, the parts must be sand blasted in order to ‘rough up’ the
surface for proper paint adhesion. Sand blasting will not remove
thermoplastic coating (abrasive material will bounce off).
Loose coating can be removed by cutting with a sharp cutting
tool (chisel, putty knife or knife).
Heat Source
WARNING
• When using an open flame be aware of the materials around
the work area. Some solvents, lubricants and materials are
extremely flammable.
• Drain all components of lubricants, water or any other
fluids. Remove, or open all vents and drains. Components
will be hot and may discharge hot fluids or gases. Allow
sufficient time for components to cool, or cool off
components, prior to handling. Gaskets, seals, ‘O’ rings, and
any components that may be damaged should be removed
prior to applying coating.
Thermoplastic coating is heat applied. The surface of the
component to which the thermoplastic coating is being applied
must be maintained at a temperature of a least 230º F (110º C),
but not over 450º F (232º C). Optimum temperature is 300º F
(149º C) for best results. A small propane torch (Ingersoll-Rand
Part No. 71308886) or heat gun (Ingersoll-Rand Part No.
71308894) can be used.
NOTICE
• When using a heat source always keep it moving. Small
circles work best. Failure to do so will result in a scorched
area at the repair.
The choice of heat gun or propane torch depends on the size of
the area to be coated and the amount of time available to
accomplish the task. The propane torch heats the surface faster,
but is hard to control and can scorch the coating. The heat gun is
slower, easier to control and generally results in a better looking
finish.
Repairing Surfaces
For minor repairs to the thermoplastic coating conduct the
following:
1.
If the under laying surface is not corroded and the scratch is
less than 1/16 inch (1.6 mm) wide the surrounding
thermoplastic coating can be heated until the material flows
together. For clean surfaces with damage greater than 1/16
inch (1.6 mm) heat the area and then apply thermoplastic
coating powder (Ingersoll-Rand Part No. 71308902 [2 oz.
(56.7 g)] to fill the area. Continue heating until coating
liquefies and flows together with the existing coating.
Summary of Contents for force5 FA5A-LAK1
Page 34: ...34 WINCH ASSEMBLY PARTS DRAWING ...
Page 36: ...36 MOTOR ASSEMBLY PARTS DRAWING ...
Page 38: ...38 DISC BRAKE ASSEMBLY PARTS DRAWING ...
Page 40: ...40 DRUM BAND BRAKE ASSEMBLY PARTS DRAWING ...
Page 42: ...42 LEVER OPERATED CONTROL VALVE ASSEMBLY PARTS DRAWING ...
Page 44: ...44 PENDANT OPERATED PILOT CONTROL VALVE ASSEMBLY PARTS DRAWING ...
Page 48: ...48 SHUTTLE VALVE ASSEMBLY PARTS DRAWING ...
Page 50: ...50 EMERGENCY STOP AND OVERLOAD ASSEMBLY PARTS DRAWING ...
Page 52: ...52 OPEN FRAME FACE WINCH ASSEMBLY PARTS DRAWING ...
Page 57: ...57 WINCH LABEL TAG LOCATION AND PART NUMBER REFERENCE DRAWING ...