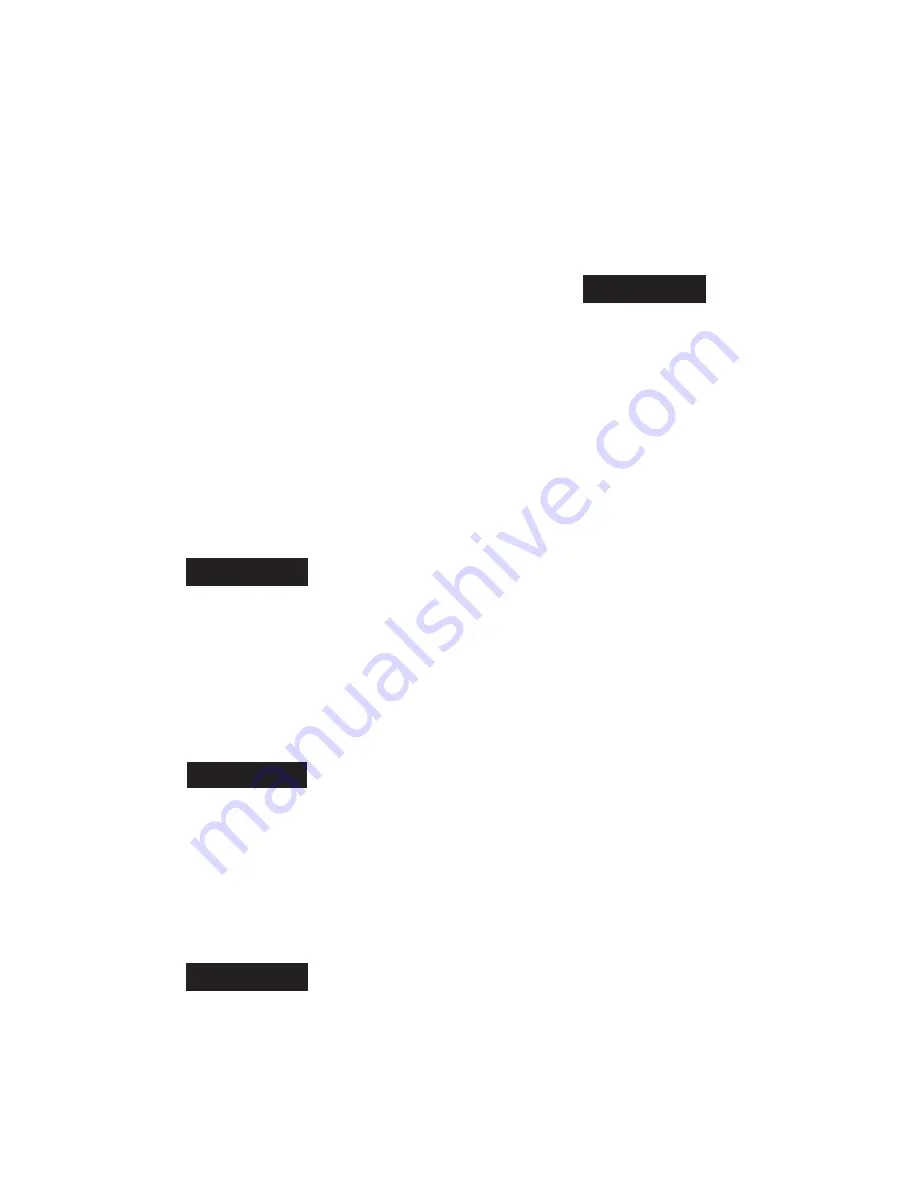
20
2.
Corrosion in damaged area must be removed. Sandblast or
wire brush the area to remove corrosion. If corrosion exists,
ensure the corrosion has not penetrated below the surface of
existing thermoplastic coating. This can usually be easily
determined by checking to see if the coating is loose around
the corroded area. Cut away coating as necessary to expose
corrosion for removal. If the damaged area is less than 1/16
inch (1.6 mm) wide the surrounding thermoplastic coating
can be heated until the material flows together. For surfaces
with damage greater than 1/16 inch (1.6 mm) heat the area
and then apply thermoplastic coating powder
(Ingersoll-Rand Part No. 71308902 [2 oz. (56.7 g)] to fill
the area. Continue heating until coating liquefies and flows
together with the existing coating.
3.
Allow the repaired area to cool. Quenching with water is
acceptable. Inspect the repair. Rough spots, minor
scorching and excess coating deposits can be wet sanded to
remove the imperfections. To return the gloss finish, reheat
the surface carefully.
For large bare surfaces or new parts:
Coating these components can be done more economically and
with better end results by using an electrostatic powder
application process or flamespray process. Contact
Ingersoll-Rand Technical Assistance for more information.
For specific disassembly and assembly information refer to
‘Assembly’ or ‘Disassembly’ in the “MAINTENANCE” section.
Adjustments
Disc Brake
Brake adjustment is not required. If the disc brake does not hold
100% of rated load at mid drum, disassemble and repair.
NOTICE
• Winches are provided with a breather plug located at the
top of the disc brake housing. If the brake assembly is
removed or repaired ensure the breather is installed and
located at the top of the brake housing during reassembly.
Drum Band Brake
Refer to Dwg. MHP0631.
References to “clockwise” and “counterclockwise” directions, in
the text, refer to directions as viewed from the head end of
capscrew (120).
NOTICE
• If brake band cannot be adjusted to hold rated load, replace
the brake band assembly.
Manual Brake:
1.
Loosen capscrew (130) located in cam plate (131).
2.
Adjust band assembly using capscrew (120).
a.
To loosen band brake, turn capscrew (120) in the
counterclockwise direction.
b.
To tighten band brake, turn capscrew (120) in the
clockwise direction.
NOTICE
• If the capscrew (120) is not accessible, the jam nut (117)
may be used to adjust the band brake. Ensure capscrew turns
with nut.
3.
When adjustments are complete tighten capscrew (130)
located in cam plate (131). Capscrew (130) engages locking
pellet (129) to hold capscrew (120) in place. Check that
capscrew (120) cannot turn when capscrew (130) is
tightened. If capscrew (120) turns, replace locking pellet
(129).
Automatic Brake:
1.
Loosen jam nut (117) closest to plunger (114).
2.
Adjust band assembly using capscrew (120).
a.
To loosen band brake, turn capscrew (120) in the
counterclockwise direction.
b.
To tighten band brake, turn capscrew (120) in the
clockwise direction.
NOTICE
• If the capscrew (120) is not accessible, the jam nut (117)
[located closest to the head of capscrew (120)] may be used to
adjust the band brake. Ensure capscrew turns with nut.
3.
When adjustments are complete tighten jam nut (117)
closest to plunger (114).
Disassembly
General Disassembly Instructions
The following instructions provide the necessary information to
disassemble, inspect, repair, and assemble the winch. Parts
drawings are provided in the Parts Section.
If a winch is being completely disassembled for any reason,
follow the order of the topics as they are presented.
It is recommended that all maintenance work on the winch be
performed in a clean dust free work area.
In the process of disassembling the winch, observe the
following:
1.
Never disassemble the winch any further than is necessary
to accomplish the needed repair. A good part can be
damaged during the course of disassembly.
2.
Never use excessive force when removing parts. Tapping
gently around the perimeter of a cover or housing with a
soft hammer, for example, is sufficient to break the seal.
3.
Do not heat a part with a flame to free it for removal,
unless the part being heated is already worn or damaged
beyond repair and no additional damage will occur to other
parts.
In general, the winch is designed to permit easy disassembly and
assembly. The use of heat or excessive force should not be
required.
4.
Keep the work area as clean as practical, to prevent dirt and
other foreign matter from getting into bearings or other
moving parts.
5.
All seals and ‘O’ rings should be discarded once they have
been removed. New seals and ‘O’ rings should be used
when assembling the winch.
6.
When grasping a part in a vise, always use leather-covered
or copper-covered vise jaws to protect the surface of the
part and help prevent distortion. This is particularly true of
threaded members, machined surfaces and housings.
7.
Do not remove any part which is a press fit in or on a
subassembly unless the removal of that part is necessary for
repairs or replacement.
8.
When removing ball bearings from shafts, it is best to use a
bearing puller. When removing bearings from housings,
drive out the bearing with a sleeve slightly smaller than the
outside diameter of the bearing. The end of the sleeve or
pipe which contacts the bearing must be square. Protect
bearings from dirt by keeping them wrapped in clean
cloths.
Summary of Contents for force5 FA5A-LAK1
Page 34: ...34 WINCH ASSEMBLY PARTS DRAWING ...
Page 36: ...36 MOTOR ASSEMBLY PARTS DRAWING ...
Page 38: ...38 DISC BRAKE ASSEMBLY PARTS DRAWING ...
Page 40: ...40 DRUM BAND BRAKE ASSEMBLY PARTS DRAWING ...
Page 42: ...42 LEVER OPERATED CONTROL VALVE ASSEMBLY PARTS DRAWING ...
Page 44: ...44 PENDANT OPERATED PILOT CONTROL VALVE ASSEMBLY PARTS DRAWING ...
Page 48: ...48 SHUTTLE VALVE ASSEMBLY PARTS DRAWING ...
Page 50: ...50 EMERGENCY STOP AND OVERLOAD ASSEMBLY PARTS DRAWING ...
Page 52: ...52 OPEN FRAME FACE WINCH ASSEMBLY PARTS DRAWING ...
Page 57: ...57 WINCH LABEL TAG LOCATION AND PART NUMBER REFERENCE DRAWING ...