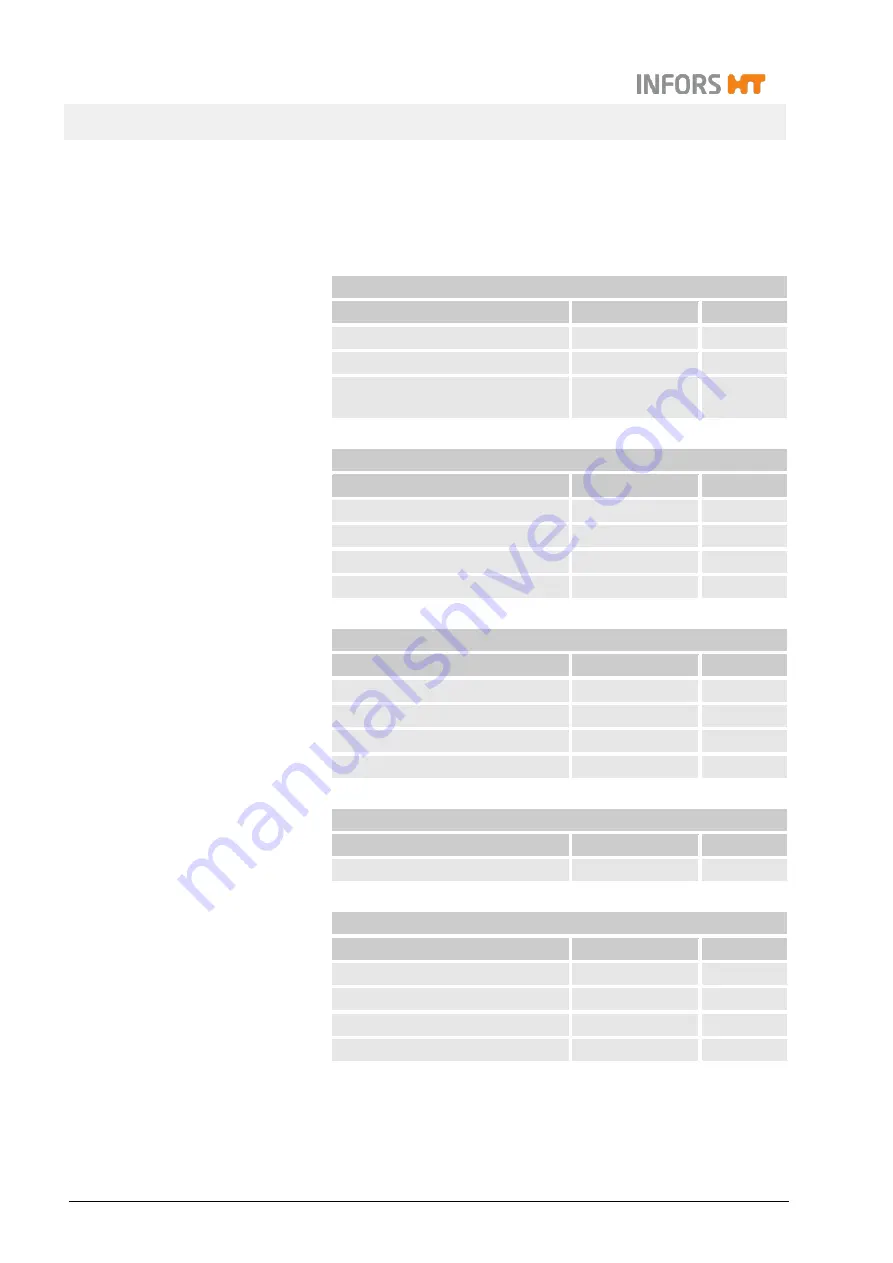
Ecotron - Incubation Shaker
Technical Data and Specifications
Page
80
of
90
03 May 2018
12.2 Specifications of the Basic Equipment
12.2.1 Weight and Dimensions
Mass
Description
Value Unit
Individual unit without cooling
63 kg
Individual unit with internal cooling
78 kg
Individual unit with external cool-
ing
65 kg
Exterior dimensions of individual unit without cooling
Description
Value Unit
Width
635 mm
Height
630 mm
Depth
(door closed)
630 mm
Depth
(door open)
830 mm
Exterior dimensions of individual unit with cooling system
Description
Value Unit
Depth
(internal cooling, door closed)
785 mm
Depth
(internal cooling, door open)
985 mm
Depth
(external cooling, door closed)
665 mm
Depth
(external cooling, door open)
870 mm
Exterior dimensions of equipment stacked in pairs
Description
Value Unit
Height
1260 mm
Interior dimensions (incubation chamber)
Description
Value Unit
Width
500 mm
Height
430 mm
Depth
580 mm
Volume
120 L