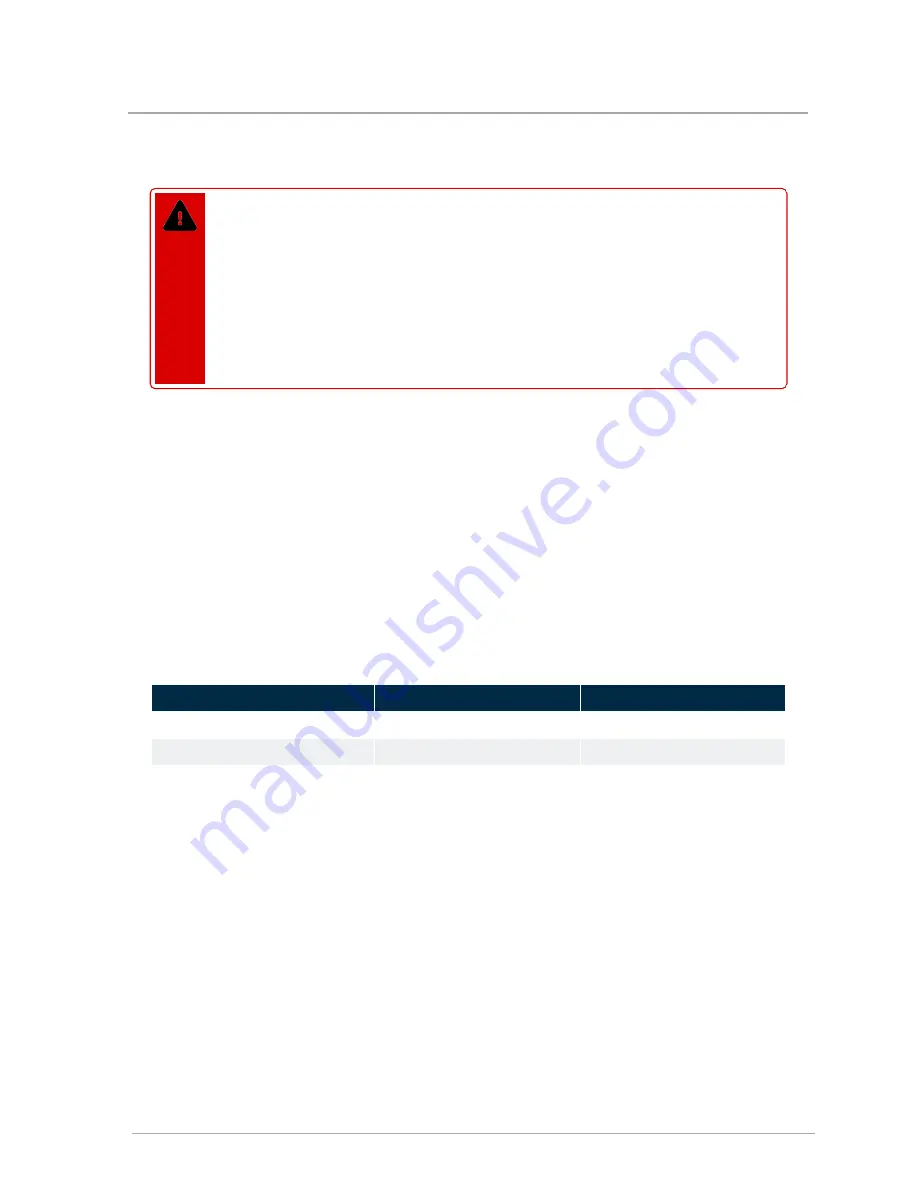
6.3.1 Checking a boiler's fuel source
Danger
Operating any IBC appliance using a fuel other than the fuel listed on its rating plate is
prohibited. Failure to follow the instructions on converting to alternate fuels can result
in a fire or explosion, which may cause property damage, personal injury, or loss of life.
Check the rating plate of the appliance to ensure it is configured for the fuel you are
using. If the fuel is incorrect for the appliance, a conversion kit must be ordered from
IBC and the gas valve adjusted accordingly. Failure to perform the required fuel
conversion can result in an immediate hazard.
This boiler model can burn either natural gas or propane if equipped with the correct fuel-air
metering device. Examine the rating plate of the boiler to ensure it is configured for the fuel you
are using. For example, if the boiler is configured for natural gas, but needs to be converted to
propane, use the conversion kit (sold separately by IBC) to install the appropriate fitting(s) and
adjust the gas valve accordingly. See
for the required conversion kit.
The
touchscreen controller
will automatically detect the installation’s altitude and make the
appropriate adjustments to operate the boiler up to 4,500 feet in elevation without de-ration. The
boiler will automatically de-rate at altitudes above 4,500 feet.
Fuel conversion kit numbers
Compare the boiler model number with the Kit # found in the table below:
Model Number
Natural Gas to Propane
Propane to Natural Gas
SL 10-85 G3, SL 14-115 G3
SL 20-160 G3
SL 30-199 G3
Table 10
Fuel Conversion Kits
6.3.2 Performing a fuel conversion
You must be a qualified heating professional to perform this procedure. In this fuel conversion,
you will be replacing the orifice, located between the gas valve and gas line to the fan, with the
fuel-appropriate orifice supplied in the kit.
69
6.3.1 Checking a boiler's fuel source
Summary of Contents for SL 10-85 G3
Page 8: ...Intentionally left empty ...
Page 14: ...Intentionally left empty ...
Page 66: ...Figure 49 Electric wiring connections 62 Section Installation ...
Page 78: ...Intentionally left empty ...
Page 92: ...Intentionally left empty ...
Page 106: ...Internal wiring diagram Figure 53 Internal wiring diagram 102 Section Appendices ...
Page 107: ...Sequence of Operation Figure 54 Sequence of Operation 103 Sequence of Operation ...
Page 109: ...105 Exploded views of boiler parts ...
Page 114: ...110 Section Appendices ...
Page 122: ...Intentionally left empty ...