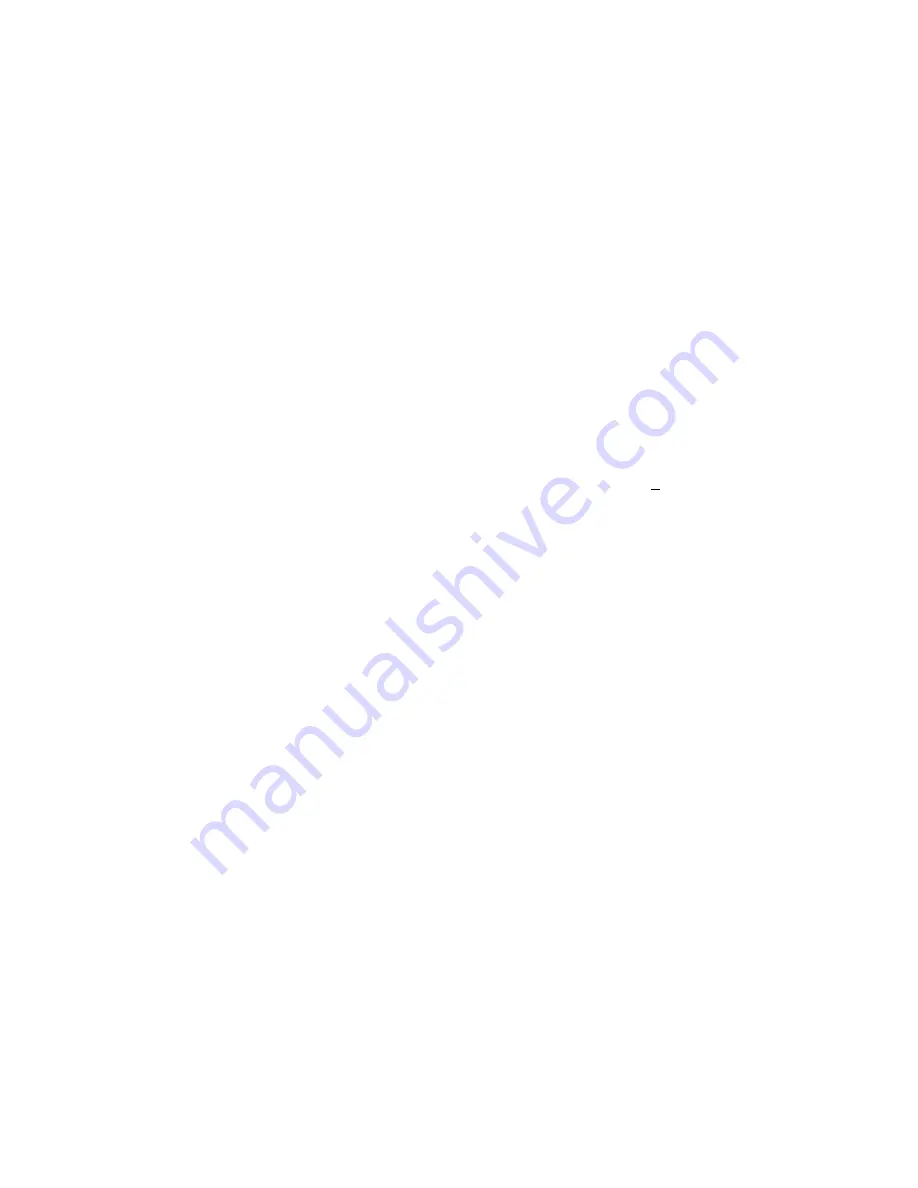
Installation and Maintenance Manual
51
Troubleshooting
Trouble With Gate Movement in General:
1. Review the HRG index arm adjustment and the flow control valve adjustment.
2. Inspect the operator for hydraulic leaks both in the control panel and the base of the operator
post, insure there is suf
ficient fluid in the reservoir, if not refill it to within 1‖ of the fill plug.
3. During operation listen for unusual sounds and investigate the source.
Electrical Problems in General:
NOTE
: The green LED (near terminal #24 on Classic Controllers o
r near the ―coin‖ battery on New Generation
Controllers) is the heartbeat of the processor. This LED should always blink brightly to indicate normal operation.
The Smart Touch Controller reports system malfunctions on its LCD display and the buzzer will emit a
series of chirps at defined intervals. Review the matrix of Alerts, Faults and Errors listed in the
Troubleshooting
chart. To disclose the status of all inputs on the terminal strip, the LED tact button must
be pushed. This button is in the upper left corner near the Stop input.
Specific Types of Problems:
"I pushed the open and close buttons, but nothing runs."
1. Verify that the line voltage is present and matches the operator v 10%.
2. In three phase applications insure that all three legs of line voltage pass though the power
disconnect switch to the motor contactor, in case one of the lines is dropped somewhere.
3. Verify that control voltage is present at the power supply Common and 24VDC terminals. It may
be necessary to reset the circuit breaker (black button) on the transformer.
4. Verify a jumper wire joins Common to Stop, if an external stop button is not used.
5. Verify there are no Faults or Errors reported on the LCD display.
6.
If the motor contactor chatters, voltage drop due to undersized wires is the likely cause. Check
Appendix 9 for maximum allowable length of wiring runs vs. wire size.
"The pump is running but the gate panels don’t move."
(Hydraulic pressure is between 0 - 700 PSI on the gauge)
1. If the power is three-phase, verify CCW motor rotation and reverse any two AC lines if needed.
2. Check the level of the hydraulic oil by removing the plug in the reservoir. If necessary, add oil at
this location to within one inch of the filler hole.
3. Unplug the hoses and run the pump, look at the pressure gauge to confirm the system pressure
reaches 1350 PSI. Re-attach the hoses when complete.
4. If relief pressure is not attained, remove the relief valve entirely and depress the plunger at the
nose end with a blunt tool (large Allen wrench) and blow it to remove any debris. Return the valve
to the power unit once cleaned.
“Hydraulic pressure is above 700 PSI”
1. Verify that the quick connectors at the hose ends are fully seated when connected.
2. Check the flow control valve, it must not be turned too far clock-wise. See adjustment
instructions.
Summary of Contents for SwingRiser 14
Page 2: ......
Page 18: ...Installation and Maintenance Manual 8 Tools Required for an Efficient Installation ...
Page 19: ...Installation and Maintenance Manual 9 Swing Gate Post Details ...
Page 20: ...Installation and Maintenance Manual 10 Swing Gate Post Details continued ...
Page 21: ...Installation and Maintenance Manual 11 Swing Gate Post Details continued ...
Page 22: ...Installation and Maintenance Manual 12 HRG 220 Pump Pack ...
Page 23: ...Installation and Maintenance Manual 13 HRG 222 Pump Pack ...
Page 24: ...Installation and Maintenance Manual 14 How Our Hydraulic Swing Gates Work ...
Page 32: ...Installation and Maintenance Manual 22 ...
Page 54: ...Installation and Maintenance Manual 44 Loop Layouts ...
Page 77: ...Installation and Maintenance Manual 67 ...
Page 83: ...Installation and Maintenance Manual 73 Smart Touch Controller Connections ...